On-vehicle shoe grinder from Italy
Page 23
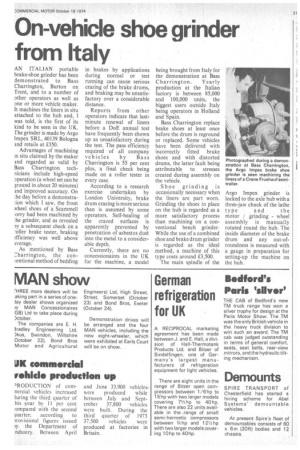
If you've noticed an error in this article please click here to report it so we can fix it.
AN ITALIAN portable brake-shoe grinder has been demonstrated to Bass Charrington, Burton on Trent, and to a number of other operators as well as one or more vehicle maker. It machines the liners in situ attached to the hub and, I was told, is the first of its kind to be seen in the UK. The grinder is made by Argo Impex SRL, 40139 Bologna and retails at E350.
Advantages of machining in situ claimed by the maker and regarded as valid by Bass Charrington technicians include high-speed Dperation (a wheel set can be ground in about 20 minutes) and improved accuracy. On .he day before a demonstra:ion which I saw, the front wheel shoes of a Scammell orry had been machined by he grinder, and as revealed Dy a subsequent check on a .oller brake tester, braking fficiency was well above average.
As mentioned by Bass 2.harrington, the conientio nal method of bedding in brakes by applications during normal or test running can cause serious crazing of the brake drums, and braking may be unsatisfactory over a considerable distance.
Reports from other operators indicate that lastminute renewal of liners before a DoE annual test have frequently been shown up as unsatisfactory during the test. The pass efficiency required of all company vehicles by Bass Charrington is 55 per cent plus, a final check being made on a roller tester in every case.
According to a research exercise undertaken by London University, brake drum crazing is more serious than is assumed by some operators. Self-healing of the crazed surfaces is apparently prevented by penetration of asbestos dust into the metal to a considerable depth.
Currently, there are no concessionaires in the UK for the machine, a model being brought from Italy for the demonstration at Bass Charrington. Yearly production at the Italian factory is between 85,000 and 100,000 units, the biggest users outside Italy being operators in Holland and Spain.
Bass Charrington replace brake shoes at least once before the drum is reground or replaced. Some vehicles have been delivered with incorrectly fitted brake shoes and with distorted drums, the latter fault being attributable to stresses created during assembly on the vehicle.
Shoe grinding is occasionally necessary when the liners are part worn. Grinding the shoes in place on the hub is regarded as a more satisfactory process than machining on a conventional bench grinder. While the use of a combined shoe and brake drum grinder is regarded as the ideal method, a machine of this type costs around £3,500.
The main spindle of the Argo Impex grinder is locked to the axle hub with a three-jaw chuck of the lathe type and the motor grinding wheel assembly is manually rotated round the hub. The inside diameter of the brake drum and any out-ofroundness is measured with a gauge in preparation for setting-up the machine on the hub.