DON'T LET THE TRAILER BE THE MAIN FEATURE
Page 100
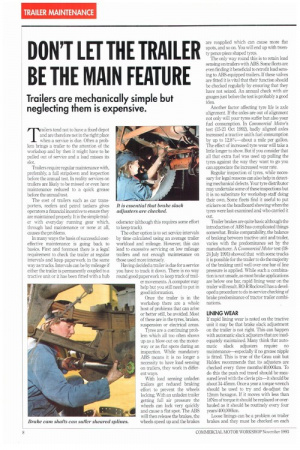
Page 101
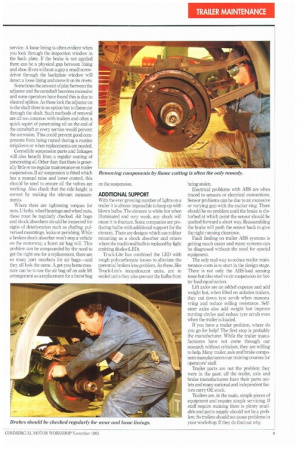
If you've noticed an error in this article please click here to report it so we can fix it.
Trailers are mechanically simple but neglecting them is expensive.
Ta.ailers tend not to have a fixed depot nd are therefore not in the right place when a service is due. Often a problem brings a trailer to the attention of the workshop and by then it might have to be pulled out of service and a load misses its slot.
Trailers require regular maintenance with, preferably, a full stripdowit and inspection before the annual test. In reality services on trailers are likely to be missed or even have maintenance reduced to a quick grease before the annual test.
The cost of trailers such as car transporters, reefers and petrol tankers gives operators a financial incentive to ensure they are maintained properly. It is the simple trailer with everyday running gear which, through bad maintenance or none at all, causes the problems.
In many ways the basis of successful costeffective maintenance is going back to basics. First and foremost there is a legal requirement to check the trailer at regular intervals and keep paperwork in the same way as trucks. Intervals can be by mileage if either the trailer is permanently coupled to a tractive unit or it has been fitted with a hub odometer (although this requires some effort to keep track).
The other option is to set service intervals by time calculated using an average trailer workload and mileage. However, this can lead to excessive servicing on low mileage trailers and not enough maintenance on those used more intensely.
Having decided a trailer is due for a service you have to track it down. There is no way round good paperwork to keep track of trailer movements. A computer may help but you still need to put in good information.
Once the trailer is in the workshop there are a whole host of problems that can arise or better still, be avoided. Most of these are in the tyres, brakes, suspension or electrical areas.
Tyres are a continuing problem which all too often shows up as a blow-out on the motorway or as flat spots during an inspection. While mandatory ABS means it is no longer a necessity to have load sensing on trailers, they work in different ways.
With load sensing unladen trailers get reduced braking effort to prevent the wheels locking. With an unladen trailer getting full air pressure the wheels can lock very quickly and cause a flat spot. The ABS will then release the brakes, the wheels speed up and the brakes are reapplied which can cause more flat spots, and so on. You will end up with twenty pence piece shaped tyres The only way round this is to retain load sensing on trailers with ABS. Some fleets are even finding it beneficial to retrofit load sensing to ABS-equipped trailers. If these valves are fitted it is vital that their function should be checked regularly by ensuring that they have not seized. An annual check with air gauges just before the test is probably a good idea.
Another factor affecting tyre life is axle alignment. If the axles are out of alignment not only will your tyres suffer but also your fuel consumption. In Commercial Motor's test (15-21 Oct 1992), badly aligned axles increased a tractive unit's fuel consumption by up to 12.8o—about a mile per gallon. The effect of increased tyre wear will take a little longer to show. But if you consider that all that extra fuel was used up pulling the tyres against the way they want to go you can appreciate the increased wear rate.
Regular inspection of tyres, while necessary for legal reasons can also help in detecting mechanical defects. Your tyre distributor may undertake some of these inspections but it is no substitute for workshop staff doing their own. Some fleets find it useful to put stickers on the headboard showing when the tyres were last examined and who carried it out.
Trailer brakes are quite basic although the introduction of ABS has complicated things somewhat. Brake compatability, the balance of braking between tractive unit and trailer, varies with the predominance set by the manufacturer. A Commercial Motor test (1824 July 1991) showed that with some trucks it is possible for the trailer to do the majority of the braking until well over one bar of line pressure is applied. While such a combination is not unsafe, as most brake applications are below one bar, rapid lining wear on the trailer will result. RO-R Rockwell has a developed a procedure to do in-service checking of brake predominance of tractor trailer combinations.
LINING WEAR if rapid lining wear is noted on the tractive unit it may be that brake slack adjustment on the trailer is not right. This can happen with automatic slack adjusters that are inadequately maintained. Many think that automatic slack adjusters require no maintenance—especially if no grease nipple is fitted. This is true of the Grau unit but Haldex recommends that its adjusters are checked every three months/40,000km. To do this the push rod travel should be measured level with the clevis pin—it should be about 34-45mm. Once a year a torque wrench should be used to try and de-adjust the 12mm hexagon. If it moves with less than 18Nm of torque it should be replaced or overhauled as it should be routinely every four years/400,0001cm.
Loose linings can be a problem on trailer brakes and they must be checked on each service. A loose lining is often evident when you look through the inspection window in the back plate. If the brake is not applied there can be a physical gap between lining and shoe. Even without a gap a small screwdriver through the backplate window will detect a loose lining and move it on its rivets.
Sometimes the amount of play between the adjuster and the camshaft becomes excessive and some operators have found this is due to sheared splines. As these lock the adjuster on to the shaft there is no option but to flame cut through the shaft. Such methods of removal are all too common with trailers and often a quick squirt of penetrating oil on the end of the camshaft at every service would prevent the corrosion. This could prevent good components from being ruined during a routine stripdown or when replacements are needed.
Corrodible suspension parts and linkages will also benefit from a regular coating of penetrating oil. Other than that there is generally little or no regular maintenance on trailer suspensions. If air suspension is fitted which has a manual raise and lower control, this should be used to ensure all the valves are working Also check that the ride height is correct by making the relevant measurements.
Where there are tightening torques for nuts, U-bolts, wheel bearings and wheel nuts, these must be regularly checked. Air bags and shock absorbers should be inspected for signs of deterioration such as chafing, pulverised mountings, leaks or perishing. While a broken shock absorber won't stop a vehicle on the motorway, a burst air bag will. This problem can be compounded by the need to get the right one for a replacement, there are so many part numbers for air bags—and they all look the same. A get-you-home measure can be to use the air bag off an axle lift arrangement as a replacement for a burst bag on the suspension.
ADDITIONAL SUPPORT With the ever growing number of lights on a trailer it is almost impossible to keep up with blown bulbs. The element is white hot when illuminated and very weak, any shock will cause it to fracture. Some companies are producing bulbs with additional support for the element. There are designs which use rubber mounting as a shock absorber and others where the traditional bulb is replaced by light emitting diodes (LED).
Truck-Lite has combined the LED with tough polycarbonate lenses to alleviate the perennial broken lens problem. As these, like Truck-Lite's incandescent units, are in sealed units they also prevent the bulbs from being stolen.
Electrical problems with ABS are often traced to sensors or electrical connections. Sensor problems can be due to an excessive or varying gap with the exciter ring. There should be no problem until the brake is disturbed at which point the sensor should be pushed forward a short way. Reassembling the brake will push the sensor back to give the right running clearance.
Fault finding on trailer ABS systems is getting much easier and many systems can be diagnosed without the need for special equipment.
The only real way to reduce trailer maintenance costs is to start in the design stage. There is not only the ABS/load sensing issue but also steel vs air suspension for better load equalisation.
Lift axles are an added expense and add weight but, when lifted on unladen trailers, they cut down tyre scrub when manoeuvring and reduce rolling resistance. Selfsteer axles also add weight but improve turning circles and reduce tyre scrub even when the trailer is loaded.
If you have a trailer problem, where do you go for help? The first stop is probably the manufacturer. While the trailer manufacturers have not come through our research without criticism, they are willing to help. Many trailer, axle and brake component manufacturers run training courses for operators' staff.
Trailer parts are not the problem they were in the past: all the trailer, axle and brake manufacturers have their parts outlets and many national and independent factors carry OE stock.
Trailers are, in the main, simple pieces of equipment and require simple servicing. If staff require training there is plenty available and parts supply should not be a problem. So trailers should not cause problems in your workshop, if they do find out why.