FOR
Page 32
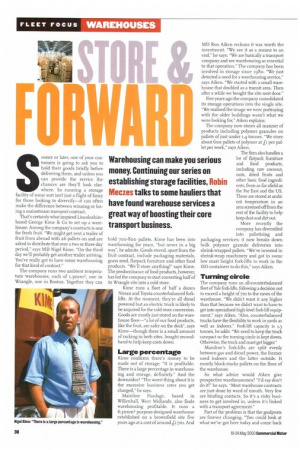
Page 33

If you've noticed an error in this article please click here to report it so we can fix it.
Sooner or later, one of your customers is going to ask you to hold their goods briefly before delivering them, and unless you can provide the service the chances are they'll look elsewhere. So running a storage facility of some sort isn't just a flight of fancy for those looking to diversify—it can often make the difference between winning or losing a mainstream transport contract.
That's certainly what inspired Lincolnshirebased George Kime & Co to set up a warehouse. Among the company's contracts is one for fresh fruit. "We might get sent a trailer of fruit from abroad with 26 pallets on and are asked to distribute that over a two or three-day period," says MD Nigel Kime. "On the third day we'll probably get another trailer arriving. You've really got to have some warehousing for that kind of contract."
The company runs two ambient temperature warehouses, each of 1,3oom2, one in Wrangle, one in Boston. Together they can
hold 700-800 pallets. Mine has been into warehousing for years, "but never in a big way", he admits. Goods stored, apart from the fruit contract, include packaging materials, grass seed, flatpack furniture and other food products. "We'll store anything!" says Kime. The predominance of food products, however, has led the company to start converting half of its Wrangle site into a cold store.
Kime runs a fleet of half a dozen Nissan and Toyota counterbalanced forklifts. At the moment, they're all diesel powered but an electric truck is likely to be acquired for the cold store conversion. Goods are mostly just stored on the warehouse floor—"a lot of our food products, like the fruit, are safer on the deck", says Kime—though there is a small amount of racking in both sites, bought secondhand to help keep costs down.
Large percentage
Kirne confirms there's money to be made out of storage: "It is profitable. There is a large percentage in warehousing and storage, definitely." And the downsides? "The worst thing about it is the excessive business rates you get charged," he says.
Mainline Haulage, based in Willenhall, West Midlands, also finds warehousing profitable. It runs a 6,5 oom2: purpose-designed warehouse established on a brownfield site five years ago at a cost of around fi.7m. And
MD Ron Aiken reckons it was worth the investment. "We see it as a means to an end," he says. "We are basically a transport company and see warehousing as essential to that operation." The company has been involved in storage since I980. "We just detected a need for a warehousing service," says Aiken. 'We started with a small warehouse that doubled as a transit area. Then after a while we bought the site next door."
Five years ago the company consolidated its storage operations into the single site. "We realised the image we were portraying with the older buildings wasn't what we were looking for," Aiken explains.
The company now stores all manner of products including polymer granules on p—...fiets of just under 1.4 tonnes. "We store about Goo pallets of polymer at Li per pallet per week," says Aiken.
The firm also handles a lot of flatpack furniture and food products, induding raw coconut, nuts, dried fruits and other basic food ingredients, from as far afield as the Far East and the US. These are stored at ambient temperature in an area screened off from the rest of the facility to help keep dust and dirt out.
More recently the company has diversified into palletising and packaging services; it now breaks down bulk polymer granule deliveries into shrink-wrapped pallets. "We've invested in shrink-wrap machinery and got in some low mast height fork-lifts to work in the ISO containers to do this," says Aiken.
Timing circle
The company runs an all-counterbalanced fleet of Yale fork-lifts, following a decision not to exceed a height of 7m to the eaves of the warehouse. "We didn't want it any higher than that because we didn't want to have to get into specialised high-level fork-lift equipment," says Aiken. "Also, counterbalanced trucks have the flexibility to work in yards as well as indoors." Fork-lift capacity is 1.5 tonnes, he adds: "We need to keep the truck compact so the turning cirde is kept down. Otherwise, the truck and mast get bigger" Mainline's fork-lifts are split evenly between gas and diesel power, the former used indoors and the latter outside. It mostly block-stacks pallets on the floor of the warehouse.
So what advice would Aiken give prospective warehousemen? "I'd say don't do it!" he says. "Most warehouse contracts are just done by word of mouth. Very few are binding contacts. So it's a risky business to get involved in, unless it's linked with a transport agreement."
Part of the problem is that the goalposts are forever changing. "You could look at what we've got here today and come back
in six months and the setup would be totally different," he says.
But it is a revenue earner. Aiken says the storage facility has generated around £95,000 in the first quarter of this year roughly 10% of total turnover for the period—"and its rising all the time." Should the company decide to sell up, it will also make money that way: Aiken says the site was recently valued for around Lim more than Mainline paid for it.
After joining the Palletways network in 1994, Ford, West Sussex-based Page Croup found warehousing a necessary evil, as MD Derek Page explains: "At first freight was just coming in and going straight out but then we started having to hold stock." A small building on the existing site soon proved inadequate, "so we took a decision to take the bull by the horns and set up a proper warehouse".
Space previously used for vehicle parking had to be used for this, which has given Page a subsequent parking headache, but there wasn't much choice: "More and more customers started asking us to store their freight. It's a good thing as you can derive a revenue from it and build better customer partnerships."
Vehicle loading
Page first got into storage in 1997 with this 1,4o om2 site, which it has since extended with a canopy that covers 46ornz for goods marshalling and vehicle loading/unloading.
"We were very surprised when we built the warehouse," he says. "We only just had the shell in place and the roof on and we were already being pressurised to take freight." Within a few months, the warehouse was half full and these days, he says, 'utilisation is generally high—so high, in fact, that the group has just acquired a second 1,400m2 building a couple of miles away to increase capacity
Both sites are racked; together they provide around 2,700 pallet positions with goods stacked up to six-high.
Page has a small fleet of counterbalanced (Toyota) and reach trucks (Barlow) and also runs a JCB Teletruk—a counterbalanced unit with a boom in place of a standard mast which is particularly useful for trailer loading.
The company handles a wide variety of goods including stationery, electrical goods, food and even palletised cast iron fireplaces. Finding warehouse staff hasn't been difficult, says Page, and running a warehouse has opened up a lot more doors with customers".
"It's a good addition to the business," he says. "We've all got to look at giving a complete service to customers and there's a lot of extra traffic that can come out of it once you get that relationship with your customers."
So beneficial is the storage side to the business that the Page Group is now looking at acquiring yet another site of around 1,60=2 to give another 2,00 o or so pallet positions later this year. And, like the other hauliers we spoke to, Page confirms that storage pays its way. Of the company's £4m turnover, around £150,000 a year is generated by the warehouse facilities at gross profit of around 30%.
Now how does that sound compared to straight haulage?