k Service that Keeps the Wheels Turning
Page 49
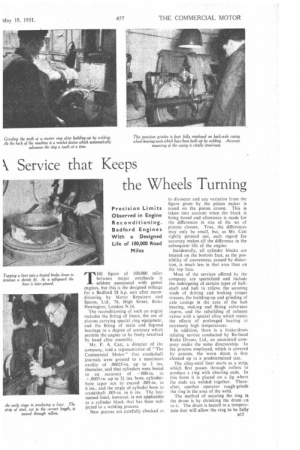
Page 50
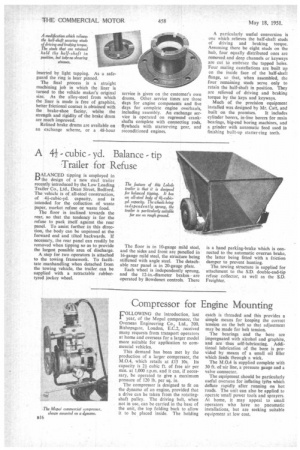
If you've noticed an error in this article please click here to report it so we can fix it.
THE figure of 100,000 miles between major overhauls is seldom associated with petrol engines, but this is the designed mileage for a Bedford 28 h.p. unit after reconditioning by Motor Repairers and Spares, Ltd.. 76. High Street, Stoke Newington, London N.16.
The reconditioning of such an engine includes the fitting of liners, the use of pistons carrying special ring equipment. and the fitting of main and big-end bearings to a degree of accuracy which permits the engine to be freely revolved by hand after assembly.
Mr. F. A. Catt, a director of the company, told a representative of "The Commercial Motor" that crankshaft journals were ground to a maximum ovality of .00025-in, up to 3 ins. diameter, and that cylinders were bored to an accuracy of —000-in. to + .0005-in, up to 3f ins, bore, cylinderbore taper not to exceed .005-in. in 6 ins., and the angle of cylinder bore to crankshaft .003-in. in 6 ins. The lastnamed limit, however, is not applicable to a cylinder block that has been subjected to a welding process.
New pistons are carefully checked es to diameter and any variation from the figure given by the piston maker is noted on the piston crown. This is taken into account when the block is being bored and allowance is made for the differences in size of the set of pistons chosen. True, the differences may only be small, but, as Mr. Catt rightly pointed out, such regard for accuracy makes all the difference in the subsequent life of the engine.
Incidentally, all cylinder blocks are located on the bottom face, as the possibility of unevenness, caused by distortion, is much less in that area than on the top face.
Most of the services offered by the company aro specialized and include the redesigning of certain types of halfshaft and hub to relieve the securing studs of driving and braking torque stresses, the building-up and grinding of axle casings in the area of the hub bearing, making and fitting valve-seat inserts, and the rebuilding of exhaust valves with a special alloy which resists the effects of prolonged heating at extremely high temperatures.
In addition, there is a brake-drum relining service conducted by Re-lined Brake Drums, Ltd., an associated company under the same directorship. lathe process employed, which is covered by patents, the worn drum is first cleaned up to a predetermined size.
The alloy-steel liner starts as a strip, which first passes through rollers to produce a ring with abutting ends. In this form it is placed on a jig where the ends are welded together. Thereafter, another operator rough-grinds the ring in the area of the weld.
The method of securing the ring in the drum is by shrinking the drum en to it. The drum is heated to a temperature that will allow the ring to be fully
inserted by light tapping. As a safeguard the ring is later pinned.
The final process is a straight machining job in which the liner is turned to the vehicle maker's original size. As the alloy-steel from which the liner is made is free of graphite, better frictional contact is obtained with the brake-shoe facing, whilst the strength and rigidity of the brake drum are much improved.
Relined brake drums are available on an exchange scheme, or a 48-hour service is given on the customer's own drums. Other service times are three days for engine components and five days for complete engine overhauls, including assembly. An exchange service is operated on reground crankshafts complete with connecting rods, flywheels with starter-ring gear, and reconditioned engines. A particularly useful conversion is one which relieves the half-shaft studs of driving and braking torque. Assuming there be eight studs on the hub, four equally distributed ones are removed and deep channels or keyways are cut to embrace the tapped holes. Four mating castellations are built up on the inside face of the half-shaft flange, so that, when assembled, the four remaining studs serve only to retain the half-shaft in position. They are relieved of driving and braking torque by the keys and keyways.
Much of the precision equipment installed was designed by Mr. Catt, and built on the premises. It includes cylinder borers, in-line borers for main bearings, big-end boring machines, and a grinder with automatic feed used in finishing built-up starter-ring teeth.