Cheapen Production by Substitution
Page 32
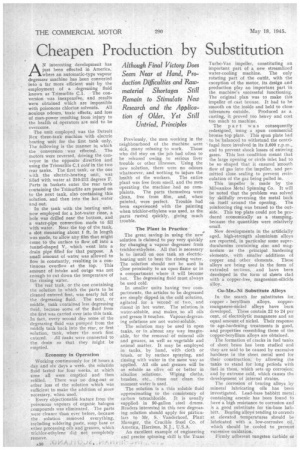
Page 35
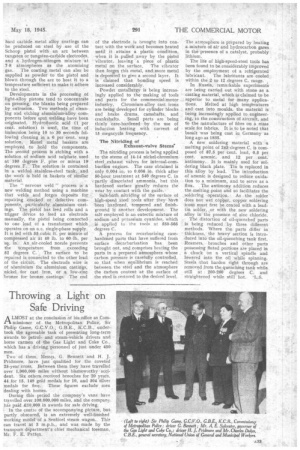
If you've noticed an error in this article please click here to report it so we can fix it.
Although Final Victory Does Sean Near at Hand, Production Difficulties and Rawmaterial Shortages Still Remain to Stimulate New Research and the Application of Older, Yet Still Untried, Principles
AN interesting development has just been effected in America, where an automatic-type vapour degreaser machine has been converted into a far more efficient unit by the employment of a degreasing fluid known as Trimurlite C.1. The conversion was inexpensiere, and results were obtained which are impossible with poisonous chlorine solvents. All noxious odours, toxic effects, and loss of man-power resulting from injury to the health of operators are said to be overcome.
The unit employed was the Detroit Rex three-tank machine with electric heating unit for the first tank only, The following is the manner in, which the conversion was effected. The motors were reversed, driving the conveyor in the opposite direction and using the Trimurlite C.1 cold in the two rear tanks. The first tank, or the one w ith the electric-heating unit, was filled with water at 210-212 degrees F. Parts in baskets enter the rear tank containing the Trimurlite are passed on to the next tank, also containing this• solution, and then into the hot water and out.
In the tank with the heating unit, now employed for a hot-water rinse, a hole was drilled near the bottom, and a water-pipe connection made to fill with water. Near the top of the tank, a slot measuring about 1 ft. in length was made, to allow any film that might come to the surface to flow off into a funnel-shaped V. which went into a drain pipe filled for that purpose. A small amount of water was allowed to flow in constantly, resulting in a continuous overflow at the top. . This amount of intake and outgo was not enough to cut clown the temperature of the rinsing water. The rear tank, or the one containing the solution in which the parts to be 'cleaned entered first, was nearly full of the degreasing fluid. The next, or middle, tank contained less degreasing fluid, because some of the fluid from the first was carried over into this tank. In fact, every second day some of 'the degreasing fluid was pumped from the middle tank back into the rear, or first solution, tank, where the work first entered. All tanks were connected to the drain so that they might be emptied.
Economy in Operation
Working continuously for 16 hours e day and six days a week, the solutiOn fluid lasted for four weeks, at which time all were emptied and then refilled. There was no drag-out or other loss of the solution which was sufficient to make the addition of more necessary, when used.
Every objectionable feature from the poisonous vapours of organic halogen compounds was eliminated. The parts were cleaner than ever before, -because the solution removed everything, ineluding soldering paste, soap base or other prOcessing oils and greases, which trichlor-ethylene did not completely remove.
e30 •4.,-;'• r?--' ,--. , e ! :', 1, 1 ,,
Previously, the men working in the neighbourhood of the machine were sick, many refusing to work. Those who did stay on the job had often to be released owing to serious liver trouble or other illnesses. Using the new solution, there were no odours whatsoever, and nothing to injure the health of the workers. The entire plant was free from smell, and the men operating the machine had no com plaints. The parts themselves were clean, free from film, and, when painted, were perfect. Trouble had been experienced with the painting when trichlor-ethylene was used, as the parts rusted quickly, giving much trouble.
The Plant in Practice
The great savingin using the new solution is claimed to pay very quickly for changing a vapour degreaser from trichlor-ethylene. All that is necessary is to install on one tank an electricheating unit to heat the rinsing water. The solution should not be used in close proximity to an openflame or in a compartment where it will become hot. The degreasing fluid must always be used cold.
In smaller units having twocompartments, the articles to be degreased are simply dipped in the cold solution, agitated for a second • or two, and rinsed in hot water. The solution. is water-soluble, and makes, so all oils and grease it touches. Vapour-degreasing solutions are not water-soluble.
The solution may be used in open tanks, or in almost any way imaginable, for the removal of mineral oils and greases, as well as vegetable and animal matter. It may be employed in tanks, by hand, with cloth or brush, or by surface spraying, and rinsing with water in the same way as applied. All oils and greases will be as soluble as olive oil or better in alkaline solutions. Wiping cloths, brushes, etc., rinse out clean the moment water is used.
The solution is a thin soluble fluid approximating to the consistency of carbon tetrachloride. It is usually supplied in 50-gallon steel drums. Readers interested in this new degreasing solution should apply fOr particulars to Mr. S. Vanderhoof, Plant Manager, the Crucible Steel Co. of America, Harrison, N. J., U.S.A.
An excellent example of engineering and precise spinning skill is the Trane .• Turbo-Vac impeller, constituting an important part of a new streamlined water-cooling machine. The only rotating part of the outfit, with the exception of the motor, its design and production play an important part in the machine's successful functioning. The original plan was to make this impeller of cast bronze. It had to be smooth on the inside and held to close tolerances outside. Produced as a casting, it proved too heavy and cost too much to machine.
'The part was consequently redesigned, using a spun commercial bronze top plate. This spun plate had to be balanced to withstand the centri' fugal force involved in its 3,600 r,p.m„ and to prevent shock losses of entering gases. This last condition meant that the large opening or circle inlet had to be so shaped that it ensured 'smooth flow of gas into the impeller, and permitted close sealing to prevent recirculation of the gas being pulled in.
This impeller is made by the Milwaukee Metal Spinning Co. It will be noted that the problem was solved by skilfully reversing the metal back on itself around the opening. The reinforcing ring was brazed to the outside. This top plate could not be produced economically as a stamping, because 'the quantities were relatively New developments in the artificially aged, high-strength aluminium alloys are reported, in particular some superduralumins containing zinc and magnesium as the principal hardening elements, with smaller additions of copper and other elements. These alloys are being used in the form of extruded sections, and have been developed in the form of sheets clad with copper-free, magnesium-silicide
a
with copper-free, magnesium-silicide
a Cu-Mn.-Ni Substitute Alloys
In the search for substitutes for
copper beryllium alloys, coppermanganese-nickel alloys have been developed. These contain 22 to 24 per cent, of electrolytic manganese and an equal amount of nickel. Their response to age-hardening treatments is good, and properties resembling those of the copper-beryllium alloys are obtained.
The formation of cracks in fuel tanks of sheet brass has been studied and they are said to be caused by excessive hardness in the sheet metal used for their construction; by allowing the tanks to stand for long periods with fuel in them, which sets -up corrosion; and by extreme cold, which causes the development "of internal strains.
The corrosion of bearing alloys by mineral lubricating oils has been investigated. Lead-base babbitt metal. containing arsenic has been found to have a-high resistance to corrosion and is a good substitute for tin-base babbitt. Bearing alloys tending to corroth at elevated temperatures should be lubricated with a low-corrosive oil,' which should be cooled to ,prevent excessive oxidation.
Firmly adherent tungsten carbide or hard carbide metal alloy coatings can be produced on steel by use of the Schoop pistol with an arc between tungsten or tungsten-carbide electrodes, and a hydrogen-nitrogen mixture at 7-8 atmospheres as the atomizing gas. The coating metal can also be supplied as powder to the pistol and blown through the arc to heat it to a temperature sufficient to make it adhere to the steel.
Developments in the processing of light-alloy pistons tend to concentrate on pressing, the blanks being prepared by extrusion. Two methods of cleaning and etching aluminium-alloy components before spot welding have been originated. Hydrofluoric acid (1 per cent. solution) is used, the time of iminersion being 10 to 30 seconds following cleaning in a 6 per cent. soap solution_ Monel metal baskets are employed to bold the components. The second process is etching with a solution of sodium acid sulphate used at 180 degrees F. plus or minus 10 degrees F. The solution is contained in a welded stainless-steel tank, and tbe work is held in baskets of similar material.
The " nervous weld " process is a new welding method using a machine that welds and .forges deposits for repairing cracked or defective components, particularly aluminium 'castings. The pistol has feed rolls and a trigger device to feed an electrode manually, the pistol being connected to one lead of a transformer which operates on an a.c. single-phase supply. It is fed with 55 cubic ft. per minute of compressed air at 40 lb. to 60,1h. per sq. in. An air-cooled nozzle prevents the temperature from exceeding 52 degrees C.. The surface to be repaired is connected to the other lead of the circuit. The electrode wire is of aluminiiim for aluminium castings, nickel for cast iron, or •a low-zinc bronze for bronze castings. The end
of the electrode is brought into contact with the work and becomes heated until it attains a plastic condition, when it is pulled away by the pistol vibrator, leaving a piece of plastic metal on the surface. The vibrator then forges this metal, and more metal is deposited to give a second layer. It is claimed that bonding speed is increased Considerably.
, Powder metallurgy is being increasingly applied to the making of tools and parts for the cornmercial=motor industry. Chromium-alloy cast irons are being developed for cylinder blocks and brake drums, camshafts, and crankshafts. Small parts are being thinly case-hardened by the use of induction heating with current of 15 megacycle frequency.
The Nitridina of Exhaust-valve Stems` The nitriding process is being applied to the stems of 14-14 nickel-chromium steel exhaust valves for internal-combustion engines. The case obtained is only 0.004 in. .to 0.008 in: thick after 50-hour treatment at 540 degrees C. in . partly dissociated ammonia, but this hardened surface greatly reduces the wear by contact with the guide.
Salt-bath nitriding of the surface of high-speed steel tools after they have been hardened, tempered and finishground is another development. The salt employed is an eutectic mixture of sodium and potassium cyanides, which is applied to tile tools at 550-565 degrees C.
A process for recarburizing casehardened parts that have suffered from surface decarburization has been brought out, and comprises heating the parts in a prepared atmosphere whose carbon pressure is carefully controlled, so that when equilibrium is reached between. the steel and the atmosphere the carbon content at the surface of the steel is restored to the desired level. The atmosphere is prepared by heating a mixtuie of air and hydrocarbon gases in the presence of a catalyst, probably lithium, The life of high-speed-steel tools has been found to be considerably improved by the employment of a refrigerated lubricant, . The lubricants are cooled within the 2 to 12 degrees C. range. In Russia, remarkable experiments are being carried out with stone as a casting material, which is claimed to be superior to metal for many applica tions. Melted at high temileratures and cast into moulds, the material is being increasingly applied to engineering, to the construction of aircraft, and
to the manufacture of fibre on a mass scale for fabrics. It is.to be noted that basalt -was being cast in Germany as long ago-as 1935.
A new soldering material with a melting point of 243 degrees C. is com posed of 87.5 per cent. lead, 0.5 per cent, arsenic, and 12 per cent. antimony. It is mainly used for sol dering black plate. Tin is replaced in this alloy by lead. The introduction of arsenic is designed to reduce oxida tion to a minimum, and to serve as a flux. The antimony addition reduces the melting point and so facilitates the soldering operation. As the solder does not wet copper, copper soldering irons must first be coated with a lead tin so/der, or with the new soldering alloy in the presence of zinc chloride. The distortion of oil-quenched parts is being reduced by three different methods. Where the parts differ in thickness, the heavy section is introduced into the oil-quenching tank first. Reamers, broaches and other parts possessing fluted portions are placed in a chuck on a vertical spindle and lowered into the oil while spinning. Steels that harden right through are removed from the quenching tank while still at : 200-260 degrees C. and straightened while still hot.