Know Your Air Brakes
Page 57
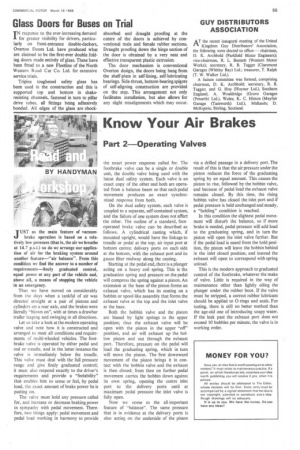
If you've noticed an error in this article please click here to report it so we can fix it.
Part 2—Operating Valves
JUST as the main feature of vacuumbrake operation is based on a relatively low pressure (that is, the air we breathe at 14.7 p.s.i.) so do we arrange our application of air for the braking system around another feature—"air balance". From this condition we find the answer to a number of requirements—finely graduated control, equal power at any part of the vehicle and, above all, a means of stopping the vehicle in an emergency.
Thus we have moved on considerably from the days when a tankful of air was directed straight at a pair of pistons and cylinders on a rear axle, and the brakes were literally "blown on", with at times a drawbar trailer leaping and swinging in all directions.
Let us take a look at the modern operating valve and note how it is constructed and arranged to meet all conditions and requirements of multi-wheeled vehicles. The footbrake valve is operated by either pedal and rod or treadle, and in the latter instance the valve is immediately below the treadle. This valve must deal with the full pressure range and give finely graduated control; it must also respond exactly to the driver's requirements and provide a "feelability" that enables him to sense or feel, by pedal load, the exact amount of brake power he is putting on.
The valve must hold any pressure called for, and increase or decrease braking power in sympathy with pedal movement. Therefore, two things apply: pedal movement and pedal load working in harmony to provide the exact power response called for. The footbrake valve can be a single or double unit, the double valve being used with the latest dual safety system. Each valve is an exact copy of the other and both are operated from a balance beam so that each pedal movement produces an exact synchronized response from both.
On the dual safety system, each valve is coupled to a separate, self-contained system, and the failure of one system does not affect the other. The outline of a standard, footoperated brake valve can be described as follows. A cylindrical casting which, if mounted upright, would have the linkage to treadle or pedal at the top; air input port at bottom centre; delivery ports on each side at the bottom, with the exhaust port and its gauze filter midway along the casting.
Starting at the pedal end, there is a plunger acting on a heavy coil spring. This is the graduation spring and pressure on the pedal will compress the spring against a piston. An extension at the base of the piston forms an exhaust valve, which has its seating on a bobbin or spool-like assembly that forms the exhaust valve at the top and the inlet valve at the base.
Both the bobbin valve and the piston are biased by light springs to the upper position; thus the exhaust valve will be open with the piston in the upper "off" position, and air will exhaust up the hollow piston and out through the exhaust port. Therefore, pressure on the pedal will load the graduating spring, which in turn will move the piston. The first downward movement of the piston brings it in contact with the bobbin valve and the exhaust is then closed; from then on further pedal movement carries the bobbin down against its own spring, opening the centre inlet port to the delivery ports until at maximum pedal pressure the inlet valve is fully open.
Now we come to the all-important feature of "balance". The same pressure that is in evidence at the delivery ports is also acting on the underside of the piston
via a drilled passage in a delivery port. The result of this is that the air pressure under the piston reduces the force of the graduating spring by an equal amount. This causes the piston to rise, followed by the bobbin valve, and because of pedal load the exhaust valve remains closed. By this time, the rising bobbin valve has closed the inlet port and if pedal pressure is held unchanged and steady, a "holding" condition is reached.
In this condition the slightest pedal movement will disturb the balance, so if more brake is needed, pedal pressure will add load to the graduating spring, and in turn the piston will open the inlet valve farther. But if the pedal load is eased from the hold position, the piston will leave the bobbin behind in the inlet closed position, and instead the exhaust will open to correspond with spring unload.
This is the modern approach to graduated control of the footbrake, whatever the make of valve. Little is required in the way of maintenance other than lightly oiling the plunger under the rubber boot. If the valve must be stripped, a correct rubber lubricant should be applied to 0-rings and seals. For testing, there is still no better method than the age-old one of introducing soapy water. If the leak past the exhaust port does not exceed 10 bubbles per minute, the valve is in working order.