1
Page 108
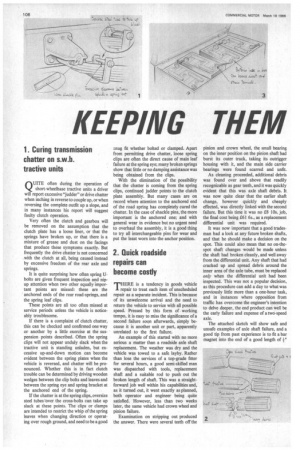
Page 109
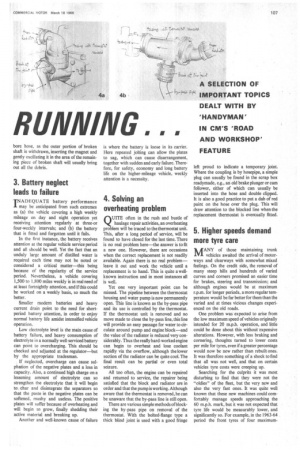
Page 110
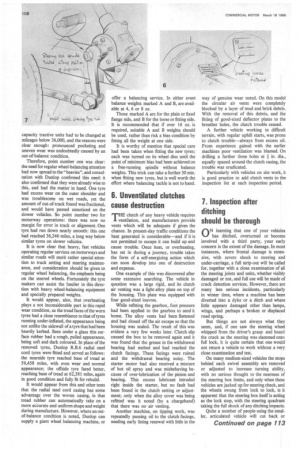
If you've noticed an error in this article please click here to report it so we can fix it.
KEEPING THEM
RUNNING .., QUITE often during the operation of short-wheelbase tractive units a driver will report excessive "judder" or drive chatter when inching in reverse to couple up, or when reversing the complete outfit up a slope, and in many instances his report will suggest faulty clutch operation.
Very often the clutch and gearbox will be removed on the assumption that the clutch plate has a loose liner, or that the springs have broken up, or that there is a mixture of grease and dust on the facings that produce these symptoms exactly. But frequently the drive chatter is not concerned with the clutch at all, being caused instead by excessive freedom of the rear axle and springs.
It is quite surprising how often spring Ubolts are given frequent inspection and nipup attention when two other equally important points are missed: these are the anchored ends of the rear road-springs, and the spring leaf clips.
These points are all too often missed at service periods unless the vehicle is noticeably troublesome.
If there is a complaint of clutch chatter, this can be checked and confirmed one way or another by a little exercise at the suspension points described. Often the spring clips will not appear unduly slack when the tractive unit is standing unladen, but excessive up-and-down motion can become evident between the spring plates when the vehicle is reversed, and chatter will be pronounced. Whether this is in fact clutch trouble can be determined by driving wooden wedges between the clip bolts and leaves and between the spring eye and spring bracket at the anchored end of the spring.
If the chatter is at the spring clips, oversize steel tubes lover the cross-bolts can take up slack at these points. The clips or clamps are intended to restrict the whip of the spring leaves when changing direction or operating over rough ground, and need to be a good snug fit whether bolted or clamped. Apart from permitting drive chatter, loose spring clips are often the direct cause of main leaf failure at the spring eye; many broken springs show that little or no damping assistance was being obtained from the clips.
With the elimination of the possibility that the chatter is coming from the spring clips, continued judder points to the clutch plate assembly. But many cases are on record where attention to the anchored end of the road spring has completely cured the chatter. In the case of shackle pins, the more important is the anchored one; and with general wear in evidence but no urgent need to overhaul the assembly, it is a good thing to try all interchangeable pins for wear and put the least worn into the anchor position.
THERE is a tendency in goods vehicle I repair to treat each item of unscheduled repair as a separate incident. This is because of its unwelcome arrival and the need to return the vehicle to service with all possible speed. Pressed by this form of working tempo, it is easy to miss the significance of a second failure soon afterwards, simply because it is another unit or part, apparently unrelated to the first failure.
An example of this started with no more serious a matter than a roadside axle shaft replacement. The weather was dry and the vehicle was towed to a safe layby. Rather than lose the services of a top-grade fitter for several hours, a good semi-skilled man was dispatched with tools, replacement shaft and a suitable rod to push out the broken length of shaft. This was a straightforward job well within his capabilities and, as it turned out, it went exactly as planned, both operator and engineer being quite satisfied. However, less than two weeks later, the same vehicle had crown wheel and pinion failure.
Examination on stripping out produced the answer. There were several teeth off the pinion and crown wheel, the small bearing on the inner position on the pinion shaft had burst its outer track, taking its outrigger housing with it, and the main side carrier bearings were found scarred and unfit.
As cleaning proceeded, additional debris was found over and above that readily recognizable as gear teeth, and it was quickly evident that this was axle shaft debris. It was now quite clear that the earlier shaft change, however quickly and cheaply effected, was directly linked with the second failure. But this time it was no £8 10s. job, the final cost being £61 6s., as a replacement differential unit was required.
It was now important that a good tradesman had a look at any future broken shafts, and that he should make a decision on the spot. This could also mean that no on-thespot shaft changes would be made unless the shaft had broken cleanly, and well away from the differential unit. Any shaft that had cracked up and spread debris around the inner area of the axle tube, must be replaced only when the differential unit had been inspected. This was not a popular decision, as this procedure can add a day to what was previously little more than a one-hour task, and in instances where opposition from traffic has overcome the engineer's intention to delve deeper, the end product can well be the early failure and expense of a two-speed axle.
The attached sketch will show safe and unsafe examples of axle shaft failure, and a good tip from past experience is to fit a bar magnet into the end of a good length of
3. Battery neglect leads to failure
TNADEQUATE battery performance .I. may be anticipated from such extremes as (a) the vehicle covering a high weekly mileage on day and night operation yet receiving attention regularly at three-or four-weekly intervals; and (b) the battery that is fitted and forgotten until it fails.
In the first instance, the battery receives attention at the regular vehicle service period and all should be well. Yet the fact that an unduly large amount of distilled water is required each time may not be noted or considered a critical matter—this being because of the regularity of the service period. Nevertheless, a vehicle covering 1,500 to 1,800 miles weekly is in real need of at least fortnightly attention, and if this could be worked on a weekly basis, so much the better.
Smaller modern batteries and heavy current drain point to the need for shortperiod battery attention, in order to enjoy normal battery life amidst intensified vehicle operation.
Low electrolyte level is the main cause Of battery failure, and heavy consumption of electrolyte in a normally well-serviced battery can point to overcharging. This should be checked and adjusted at the regulator—but by the appropriate tradesman.
If neglected, overcharge can cause sulphation of the negative plates and a loss in capacity. Also, a continued high charge on a lessening amount of electrolyte can so strengthen the electrolyte that it will begin to . char and disintegrate the separators so that the paste in the negative plates can be softened, mushy and useless. The positive plates will suffer because of overheating and will begin to grow, finally shedding their active material and breaking up.
Another and well-known cause of failure
4. Solving an overheating problem
QUITE often in the rush and bustle of haulage repair activities, an overheating problem will be traced to the thermostat unit. This, after a long period of service, will be found to have closed for the last time. There is no real problem here—the answer is to fit a new one. However, there are occasions when the correct replacement is not readily available. Again there is no real problem— leave it out and work the vehicle until a replacement is to hand. This is quite a wellknown instruction and in most instances all is well.
Yet one very important point can be missed. The pipeline between the thermostat housing and water pump is now permanently open. This line is known as the by-pass pipe and its use is controlled by the thermostat. If the thermostat unit is removed and no move made to close the by-pass line, this line will provide an easy passage for water to circulate around pump and engine block—and the value of the radiator is reduced very considerably. Thus the really hard-worked engine can begin to overheat and lose coolant rapidly via the overflow, although the lower section of the radiator can be quite cool. The final result can be partial or even total seizure.
All too often, the engine can be repaired and returned to service, the repairer being satisfied that the block and radiator are in order and that the pump is working. Although aware that the thermostat is removed, he can be unaware that the by-pass line is still open.
There are various simple methods of blocking the by-pass pipe on removal of the thermostat. With the bolted-flange type a thick blind joint is used with a good fringe left proud to indicate a temporary joint. Where the coupling is by hosepipe, a simple plug can usually be found in the scrap box readymade, e.g., an old brake plunger or cam follower, either of which can usually be inserted into the hose and double clipped. It is also a good practice to put a dab of red paint on the hose over the plug. This will draw attention to the blocked line when the replacement thermostat is eventually fitted.
5. Higher speeds demand more tyre care
MANY of those maintaining trunk vehicles awaited the arrival of motorways and clearways with somewhat mixed feelings. On the credit side, the removal of many steep hills and hundreds of varied curves and corners promised an easier time for brakes, steering and transmission; and although engines would be at maximum r.p.m. for longer periods, a more regular temperature would be far better for them than the varied and at times vicious changes experienced on the old roads.
One problem was expected to arise from the low maximum speed of vehicles originally intended for 20 m.p.h, operation, and little could be done about this without expensive alterations. However, with less braking and cornering, thoughts turned to lower costs per mile for tyres, even if a greater percentage would now be new rather than rebuilt ones. It was therefore something of a shock to find that all was not well, and that on certain vehicles tyre costs were creeping up.
Searching for the culprits it was most disturbing to find that they were not the "oldies" of the fleet, but the very new and also the very fast ones. It was quite well known that these new machines could comfortably manage speeds approaching the 60 m.p.h. mark, but it was not expected that tyre life would be measurably lower, and significantly so. For example, in the 1963-64 period the front tyres of four maximum
capacity tractive units had to be changed at mileages below 36,000, and the reasons were clear enough: pronounced pocketing and uneven wear was undoubtedly caused by an out-of-balance condition. Therefore, point number one was clear: the need for regular wheel-balancing attention had now spread to the "heavies", and consultation with Dunlop confirmed this need: it also confirmed that they were already wise to this, and had the matter in hand. One tyre had excess wear on the outer shoulder and was troublesome on wet roads, yet the amount of out-of-track found was fractional, and would have passed unnoticed on the slower vehicles. So point number two for motorway operations: there was now no margin for error in track or alignment. One tyre had run down nearly smooth: this one had reached 36,246 miles, a long way below similar tyres on slower vehicles. It is now clear that heavy, fast vehicles operating regular services on motorways and similar roads will merit rather special attention to track setting and steering maintenance, and consideration should be given to regular wheel balancing, the emphasis being on the steered wheels. Fortunately the tyre makers can assist the haulier in this direction with heavy wheel-balancing equipment and specially prepared weights. It would appear, also, that overheating plays a not inconsiderable part in this rapid wear condition, as the tread faces of the worn tyres had a close resemblance to that of tyres running under-inflated, the appearance being not unlike the sidewall of a tyre that had been heavily kerbed. Seen under a glass this surface rubber had a rough, pulled appearance, being soft and dark coloured. In place of the removed tyres, Dunlop R.B.6 radial steel cord tyres were fitted and served as follows: the nearside tyre reached base of tread at 59,458 miles, with even wear and normal appearance; the offside tyre fared better, reaching base of tread at 62,381 miles, again in good condition and fully fit for rebuild. It would appear from this and other tests that the radial steel cord casing has some advantage over the woven casing, in that tread rubber can automatically take on a more accurate and uniform shape and weight during manufacture. However, where an outof-balance condition is noted, Dunlop can supply a giant wheel balancing machine, or offer a balancing service. In either event balance weights marked A and B, are available at 4, 6 or 8 oz. Those marked A are for the plain or fixed flange side, and B for the loose or fitting side. It is recommended that if over 16 oz. is required, suitable A and B weights should be used, rather than risk a bias condition by fitting all the weight at one side. It is worthy of mention that special care had been taken when fitting the new tyres; each was turned on its wheel disc until the point of minimum bias had been achieved on a free-running spindle without balance weights. This trick can take a further 30 min. when fitting new tyres, but is well worth the effort where balancing tackle is not to hand.