Engine Know-How
Page 107
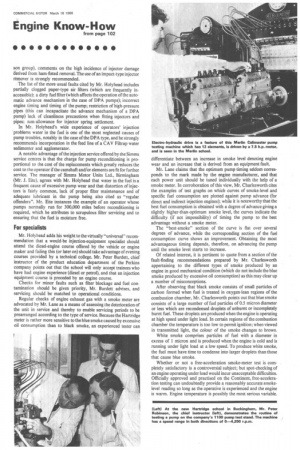
If you've noticed an error in this article please click here to report it so we can fix it.
son group), comments on the high incidence of injector damage derived from ham-fisted removal. The use of an impact-type injector remover is strongly recommended.
The list of the more usual faults cited by Mr. Holyhead includes partially clogged paper-type air filters (which are frequently inaccessible): a dirty fuel filter (which affects the operation of the automatic advance mechanism in the case of DPA pumps); incorrect engine timing and timing of the pump; restriction of high-pressure pipes (this can incapacitate the advance mechanism of a DPA pump) lack of cleanliness precautions when fitting injectors and pipes; non-allowance for injector spring settlement.
In Mr. Holyhead's wide experience of operators' injection 'problems water in the fuel is one of the most neglected causes of pump troubles, notably in the case of the DPA type, and he strongly recommends incorporation in the feed line of a CA V Entrap water sedimenter and agglomerator.
A notable advantage of the injection service offered by the Simms service centres is that the charge for pump reconditioning is proportional to the cost of the replacements which greatly reduces the cost to the operator if the camshaft and/or elements are fit for further service. The manager of Simms Motor Units Ltd., Birmingham (Mr. J. Eite). agrees with Mr. Holyhead that water in the fuel is a frequent cause of excessive pump wear and that distortion of injectors is fairly common, lack Of proper filter maintenance and of adequate lubricant in the pump being also cited as "regular offenders". Mr. Eite instances the example of an operator whose pumps normally run for 300,000 miles before reconditioning is required, which he attributes to scrupulous filter servicing and to ensuring that the fuel is moisture free.
For specialists Mr. Holyhead adds his weight to the virtually "universal" recommendation that a would-be injection-equipment specialist should attend the diesel-engine course offered by the vehicle or engine maker and failing this (or later on) should take advantage of evening courses provided by a technical college. Mr. Peter Burdett, chief instructor of the product education department of the Perkins company points out that the school will only accept trainees who have had engine experience (diesel or petrol), and that an injection equipment course is preceded by an engine course.
Checks for minor faults such as filter blockage and fuel contamination should be given priority, Mr. Burdett advises, and servicing should be matched to operational conditions.
Regular checks of engine exhaust gas with a smoke meter are advocated by Mr. Lane as a means of assessing the deterioration of the unit in service and thereby to enable servicing periods to be prearranged according to the type of service. Because the Hartridge meter is rather more sensitive to the blue smoke caused by excessive oil consumption than to black smoke, an experienced tester can differentiate between an increase in smoke level denoting engine wear and an increase that is derived from an equipment fault.
Mr. Lane claims that the optimum pump timing seldom corresponds to the mark made by the engine manufacturer, and that each power unit should be tuned individually with the help of a smoke meter. In corroboration of this view, Mr. Charlesworth cites the examples of test graphs on which curves of smoke-level and specific fuel consumption are plotted against pump advance (for direct and indirect injection engines); while it is noteworthy that the best fuel consumption is obtained with a degree of advance giving a slightly higher-than-optimum smoke level, the curves indicate the difficulty (if not impossibility) of timing the pump to the best advantage without a smoke meter.
The "best-smoke" section of the curve is flat over several degrees of advance, while the corresponding section of the fuel consumption curve shows an improvement. Obtaining the most advantageous timing depends, therefore, on advancing the pump until the smoke level starts to increase.
Of related interest, it is pertinent to quote from a section of the fault-finding recommendations prepared by Mr. Charlesworth appertaining to the different types of smoke produced by an engine in good mechanical condition (which do not include the blue smoke produced by excessive oil consumption) as this may clear up a number of misconceptions.
After observing that black smoke consists of small particles of carbon formed when fuel is treated in oxygen-lean regions of the combustion chamber, Mr. Charlesworth points out that blue smoke consists of a large number of fuel particles of 0.5 micron diameter or less which are recondensed droplets of unburnt or incompletely burnt fuel. These droplets are produced when the engine is operating at high speed under light load. In certain regions of the combustion chamber the temperature is too low to permit ignition; when viewed in transmitted light, the colour of the smoke changes to brown.
White smoke comprises particles of fuel with a diameter in excess of 1 micron and is produced when the engine is cold and is running under light load at a low speed. To produce white smoke, the fuel must have time to condense into larger droplets than those that cause blue smoke.
Whether or not a free-acceleration smoke-meter test is completely satisfactory is a controversial subject; but spot-checking of an engine operating under load would incur unacceptable difficulties. Officially approved and practised on the Continent, free-acceleration testing can undoubtedly provide a reasonably accurate smokelevel reading so long as the operative is experienced and the engine is warm. Engine temperature is possibly the most serious variable.