M ISSIONARY doctors and priests are sometimes included in the groups
Page 102
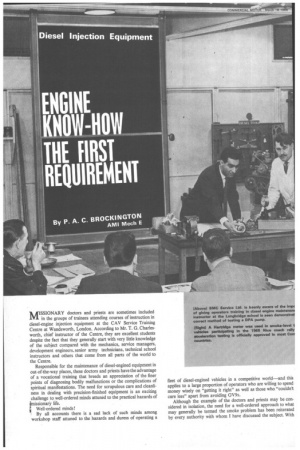
Page 103
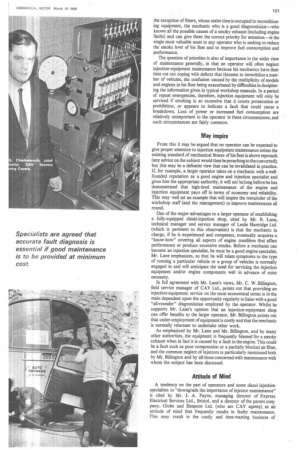
Page 104
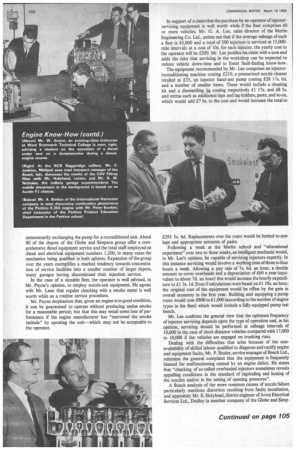
If you've noticed an error in this article please click here to report it so we can fix it.
of trainees attending courses of instruction in diesel-engine injection equipment at the CAV Service Training Centre at Wandsworth, London. According to Mr. T. G. Charlesworth, chief instructor of the Centre, they are excellent students despite the fact that they generally start with very little knowledge of the subject compared with the mechanics, service managers, development engineers, senior army technicians, technical school instructors and others that come from all parts of the world to the Centre.
Responsible for the maintenance of diesel-engined equipment in out-of-the-way places, these doctors and priests have the advantage of a vocational training that breeds an appreciation of the finer points of diagnosing bodily malfunctions or the complications of spiritual manifestations. The need for scrupulous care and cleanliness in dealing with precision-finished equipment is an exciting challenge to well-ordered minds attuned to the practical hazards of 4tnissionarY life.
Well-ordered minds!
By all accounts there is a sad lack of such minds among workshop staff attuned to the hazards and duress of operating a fleet of diesel-engined vehicles in a competitive world—and this applies to a large proportion of operators who are willing to spend money wisely on "getting it right" as well as those who "couldn't care less" apart from avoiding GV9s.
Although the example of the doctors and priests may be considered in isolation, the need for a well-ordered approach to what may generally be termed the smoke problem has been reiterated by every authority with whom I have discussed the subject. With the exception of fitters, whose entire time is occupied in reconditioning equipment, the mechanic who is a good diagnostician—who knows all the possible causes of a smoky exhaust (including 'engine faults) and can give them the correct priority for attention—is the single most valuable asset to any operator who is seeking to reduce the smoke level of his fleet and to improve fuel consumption and performance.
The question of priorities is also of importance in the wider view of maintenance generally, in that an operator will often neglect injection-equipment maintenance because his mechanics have their time cut out coping with defects that threaten to immobilize a number of vehicles, the confusion caused by the multiplicity of models and engines in his fleet being exacerbated by difficulties in deciphering the information given in typical workshop manuals. In a period of repeat emergencies, therefore, injection equipment will only be serviced if smoking is so excessive that it courts prosecution or prohibition, or appears to indicate a fault that could cause a breakdown. Loss of power or increased fuel consumption are relatively unimportant to the operator in these circumstances, and such circumstances are fairly common.
May inspire
From this it may be argued that no operator can be expected to give proper attention to injection equipment maintenance unless the existing standard of mechanical fitness of his fleet is above reproach (any advice on the subject would then be preaching to the converted); but this may be a defeatist view that can be invalidated in practice. If, for example, a larger operator takes on a mechanic with a wellfounded reputation as a good engine and injection specialist and gives him the appropriate authority, it will n6t belong before he has demonstrated that high-level maintenance of the engine and injection equipment pays off in terms of economy and reliability. This may well set an example that will inspire the remainder of the workshop staff (and the management) to improve maintenance all round.
One of the major advantages to a larger operator of establishing a fully-equipped diesel-injection shop, cited by Mr. R. Lane, technical manager and service manager of Leslie Hartridge Ltd. (which is pertinent to this observation) is that the mechanic in charge, if he is experienced and competent, eventually acquires a "know-how" covering all aspects of engine condition that affect performance or produce excessive smoke. Before a mechanic can become an injection specialist, he must be a good engine specialist, Mr. Lane emphasizes, so that he will relate symptoms to the type of running a particular vehicle or a group of vehicles is normally engaged in and will anticipate the need for servicing the injection equipment and/or engine components well in advance of strict necessity.
In full agreement with Mr. Lane's views, Mr. C. W. Billington, field service manager of CAV Ltd., points out that providing an injection-equipment service on the most economical terms is in the main dependent upon the opportunity regularly to liaise with a good "all-rounder" diagnostician employed by the operator. Whilst he supports Mr. Lane's opinion that an injection-equipment shop can offer benefits to the larger operator, Mr. Billington points out that under-employment of equipment is costly and that the mechanic is normally reluctant to undertake other work.
As emphasized by Mr. Lane and Mr. Billington, and by many other authorities, the equipment is frequently blamed for a smoky exhaust when in fact it is caused by a fault in the engine. This could be a fault such as poor compression or a partially blocked air filter, and the common neglect of injectors is particularly mentioned both by Mr. Billington and by all those concerned with maintenance with whom the subject has been discussed.
Attitude of Mind
A tendency on the part of operators and some diesel injection specialists to "downgrade the importance of injector maintenance" is cited by Mr. J. A. Payne, managing director of Express Electrical Services Ltd., Bristol, and a director of the parent company, Globe and Simpson Ltd. (who are CAV agents), as an attitude of mind that frequently results in faulty maintenance. This may result in the costly and time-wasting business of unnecessarily exchanging the pump for a reconditioned unit. About 80 of the depots of the Globe and Simpson group offer a comprehensive diesel equipment service and the total staff employed on diesel and electrical equipment numbers 1,200, in many cases the mechanics being qualified in both spheres. Expansion of the group over the years exemplifies a marked tendency towards concentration of service facilities into a smaller number of larger depots, many garages having discontinued their injection service.
In the case of a sizeable fleet, the operator is well advised, in Mr. Payne's opinion, to employ nozzle-test equipment. He agrees with Mr. Lane that regular checking with a smoke meter is well worth while as a routine service procedure.
Mr. Payne emphasizes that, given an engine is in good condition, it can be guaranteed to operate without producing undue smoke for a reasonable period; but that this may entail some loss of performance if the engine manufacturer has "narrowed the smoke latitude" by uprating the unit—which may not be acceptable to the operator. In support of a claim that the purchase by an operator of injectorservicing equipment is well worth while if the fleet comprises 40 or more vehicles, Mr. G. A. Lee, sales director of the Merlin Engineering Co. Ltd., points out that if the average mileage of such a fleet is 45,000 and a total of 200 injectors is serviced at 15,000mile intervals at a cost of 10s. for each injector, the yearly cost to the operator will be £300. Mr. Lee justifies his claim with a sum and adds the rider that servicing in the workshop can be expected to reduce vehicle down-time and to foster fault-finding know-how.
The equipment recommended by Mr. Lee comprises an injectorreconditioning machine costing £210, a pressurized nozzle cleaner retailed at £35, an injector hand-test pump costing £28 17s. 6d. and a number of smaller items. These would include a cleaning kit and a dismantling jig costing respectively £.1 17s. and £8 5s. and extras such as additional laps and lap holders, paste, and so on, which would add £7 6s. to the cost and would increase the total to £291 5s. 6d. Replacements over the years would be limited to new laps and appropriate amounts of paste.
Following a week at the Merlin school and "educational experience" over two to three weeks, an intelligent mechanic would, in Mr. Lee's opinion, be capable of servicing injectors expertly. In this instance servicing would involve a working time of three to four hours a week. Allowing a pay rate of 7s. 6d. an hour, a double amount to cover overheads and a depreciation of £60 a year (equivalent to about 7d. an hour) this would increase the hourly expenditure to £1 3s. ld. Even if calculations were based on £1 10s. an hour, the original cost of the equipment would be offset by the gain in overall economy in the first year. Building and equipping a pump room would cost £800 to £1,000 (according to the number of engine types in the fleet) which would include a fully-equipped pump test bench.
Mr. Lee confirms the general view that the optimum frequency of injector servicing depends upon the type of operation and, in his opinion, servicing should be performed at mileage intervals of 10,000 in the case of short-distance vehicles compared with 17,000 to 18,000 if the vehicles are engaged on trunking runs.
Dealing with the difficulties that arise because of the nonavailability of skilled labour qualified to diagnose and rectify engine and equipment faults, Mr. P. Studer, service manager of Bosch Ltd., reiterates the general complaint that the equipment is frequently blamed for malfunctioning caused by an engine defect. He states that "checking of so-called overhauled injectors sometimes reveals appalling conditions in the standard of regrinding and honing of the nozzles and/or in the setting of opening pressures".
A Bosch analysis of the more common causes of nozzle failure particularly mentions distortion resulting from faulty installation, and appositely Mr. E. Holyhead, district engineer of Avon Electrical Services Ltd., Dudley (a member company of the Globe and Simp