ESSO TOPS TANK T ENDS
Page 68
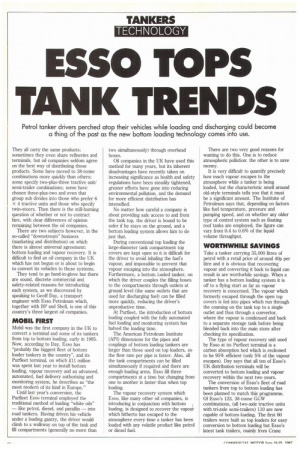
Page 69
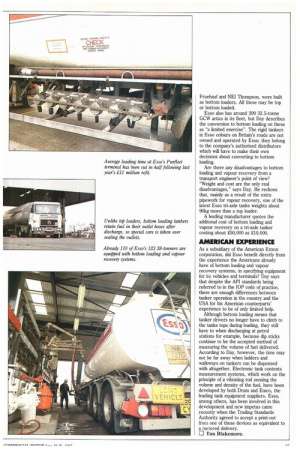
If you've noticed an error in this article please click here to report it so we can fix it.
Petrol tanker drivers perched atop their vehicles while loading and discharging could become a thing of the past as the new bottom loading technology comes into use.
They all carry the same products; sometimes they even share refineries and terminals, but oil companies seldom agree on the best way of distributing those products. Some have moved to 38-tonne combinations more quickly than others; some specify two-plus-three tractive unit/ semi-trailer combinations; some have chosen three-plus-two and even that group sub divides into those who prefer 6 x 4 tractive units and those who specify twin-steers. Then there is the still-burning question of whether or not to contract hire, with clear differences of opinion remaining between the oil companies.
There are two subjects however, in the so-called "downstream" business (marketing and distribution) on which there is almost universal agreement: bottom loading and vapour recovery. It is difficult to find an oil company in the UK which has not begun or is about to begin to convert its vehicles to these systems.
They tend to go hand-in-glove but there are sound, discrete commercial and safety-related reasons for introducting each system, as we discovered by speaking to Geoff Day, a transport engineer with Esso Petroleum which, together with BP and Shell, is one of this country's three largest oil companies.
MOBIL FIRST
Mobil was the first company in the UK to convert a terminal and some of its tankers from top to bottom loading, early in 1985. Now, according to Day. Esso has "probably the biggest fleet of bottom loader tankers in the country", and its Purfleet terminal, on which Lii million was spent last year to install bottom loading, vapour recovery and an advanced, automated, fuel delivery authorising and monitoring system, he describes as "the most modern of its kind in Europe."
Until last year's conversion, the Purfleet Ease terminal employed the traditional method of loading "white oils" — like petrol, diesel, and paraffin — into road tankers. Having driven his vehicle under a loading gantry, the driver would climb to a walkway on top of the tank and fill compartments (generally no more than
two simultaneously) through overhead hoses.
Oil companies in the UK have used this method for many years, but its inherent disadvantages have recently taken on increasing significance as health and safety regulations have been steadily tightened, greater efforts have gone into reducing environmental pollution, and the demand for more efficient distribution has intensified.
No matter how careful a company is about providing safe access to and from the tank top, the driver is bound to be safer if he stays on the ground, and a bottom loading system allows him to do just that.
During conventional top loading the large-diameter tank compartment top covers are kept open so it is difficult for the driver to avoid inhaling the fuel's vapour, and impossible to prevent that vapour escaping into the atmosphere. Furthermore, a bottom loaded tanker, on which the driver couples the filling hoses to the compartments through outlets at ground level (the same outlets that are used for discharging fuel) can be filled more quickly, reducing the driver's unproductive time.
At Purfleet, the introduction of bottom loading coupled with the fully automated fuel loading and monitoring system has halved the loading time.
The American Petroleum Institute (API) dimensions for the pipes and couplings of bottom loading tankers are larger than those used on top loaders, so the flow rate per pipe is faster. Also, all the tank compartments can be filled simultaneously if required and there are enough loading arms. Esso fill three compartments at a time but changing from one to another is faster than when top loading.
The vapour recovery system which Esso, like many other oil companies, is introducing in conjunction with bottom loading, is designed to recover the vapour which hitherto has escaped to the atmosphere every time a tanker has been loaded with any volatile product like petrol or diesel fuel. There are two very good reasons for wanting to do this. One is to reduce atmospheric pollution: the other is to save money.
It is very difficult to quantify precisely how much vapour escapes to the atmosphere while a tanker is being loaded, but the characteristic smell around old-style terminals tells you that it must be a significant amount. The Institute of Petroleum says that, depending on factors like fuel temperature, pressure and pumping speed, and on whether any older type of control system such as floating roof tanks are employed, the figure can vary from 0.4 to 0.6% of the liquid volume throughput.
WORTHWHILE SAVINGS
Take a tanker carrying 35,000 litres of petrol with a retail price of around 40p per litre and it is obvious that recovering vapour and converting it back to liquid can result in are worthwhile savings. When a tanker has a bottom loading system it is off to a flying start as far as vapour recovery is concerned. The vapour which formerly escaped through the open top covers is fed into pipes which run through the coaining on the tank top to a single outlet and thus through a convertor, where the vapour is condensed and back to a separate storage tank before being blended back into the main store after checking its specification.
The type of vapour recovery unit used by Esso at its Purfleet terminal is a carbon absorption bed which is reckoned to be 95% efficient (only 5% of the vapour escapes). Day says that all ten of Esso's UK distribution terminals will be converted to bottom loading and vapour recovery within the next two years.
The conversion of Esso's fleet of road tankers from top to bottom loading has been planned to match this programme. Of Esso's 123, 38-tonne GCW combinations, (all two-axle tractive units with tri-axle semi-trailers) 110 are now capable of bottom loading. The first 60 trailers were built as top loaders for easy conversion to bottom loading but Esso's latest tank trailers, mainly from Crane Fruehauf and NEI Thompson, were built as bottom loaders. All these may be top or bottom loaded.
Esso also has around 200 32.5-tonne GCW artics in its fleet, but Day describes the conversion to bottom loading on these as "a limited exercise". The rigid tankers in Esso colours on Britain's roads are not owned and operated by Esso; they belong to the company's authorised distributors which will have to make their own decisions about converting to bottom loading.
Are there any disadvantages to bottom loading and vapour recovery from a transport engineer's point of view? "Weight and cost are the only real disadvantages," says Day. He reckons that, mainly as a result of the extra pipework for vapour recovery, one of the latest Esso tri-axle tanks weights about 90kg more than a top loader.
A leading manufacturer quotes the additonal cost of bottom loading and vapour recovery on a tri-axle tanker costing about £50,000 as £10,000.
AMERICAN EXPERIENCE
As a subsidiary of the American Exxon corporation, did Esso benefit directly from the experience the Americans already have of bottom loading and vapour recovery systems, in specifying equipment for its vehicles and terminals? Day says that despite the API standards being referred to in the 1OP code of practice, there are enough differences between tanker operation in ths country and the USA for his American counterparts' experience to be of only limited help.
Although bottom loading means that tanker drivers no longer have to climb to the tanks tops during loading, they still have to when discharging at petrol stations for example, because dip sticks continue to be the accepted method of measuring the volume of fuel delivered. According to Day, however, the time may not be far away when ladders and walkways on tankers can be dispensed with altogether. Electronic tank contents measurement systems, which work on the principle of a vibrating rod sensing the volume and density of the fuel, have been developed by both Drum and Emco, the leading tank equipment suppliers. Esso, among others, has been involved in this development and new impetus came recently when the Trading Standards Authority agreed to accept a print-out from one of these devices as equivalent to a metered delivery.
LI Tim Blakemore.