SAFER BETTER
Page 62
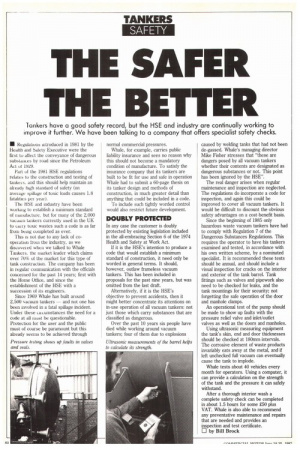
If you've noticed an error in this article please click here to report it so we can fix it.
larikers have a good safety record, but the HSE and industry are continually working to improve it further. We have been talking to a company that offers specialist safety checks.
El Regulations introduced in 1981 by the Health and Safety Executive were the first to affect the conveyance of dangerous substances by road since the Petroleum Act of 1929.
Part of the 1981 HSE regulations relates to the construction and testing of tankers, and this should help maintain an already high standard of safety (on avelage spillage of toxic loads causes 1.8 fatalities per year).
The HSE and industry have been wurkuig to establish a minimum standard of manufacture, but for many of the 2,000 villcutlill tankers currently used in the UK to wily toxic wastes such a code is as far from being completed as ever.
'Ibis is not due to any lack of coopeiation from the industry, as we discovered when we talked to Whale Tankeis, the market leader which claims over 70% of the market for this type of tank construction. The company has been in regular communication with the officials concerned for the past 14 years; first with the Home Office, and since the establishment of the HSE with a succession of its engineers.
Since 1969 Whale has built around 2,500 vacuum tankers — and not one has been involved in a fatal spillage incident. Under these circumstances the need for a code at all must be questionable. Protection for the user and the public must of course be paramount but this already seems to be achieved through normal commercial pressures.
Whale, for example, carries public liability insurance and sees no reason why this should not become a mandatory condition of manufacture. To satisfy the insurance company that its tankers are built to be fit for use and safe in operation Whale had to submit a 60-page thesis on its tanker design and methods of construction, in much greater detail than anything that could be included in a code.
To include such tightly worded control would also restrict future development.
DOUBLY PROTECTED In any case the customer is doubly protected by existing legislation included in the all-embracing Section 6 of the 1974 Health and Safety at Work Act.
If it is the HSE's intention to produce a code that would establish a minimum standard of construction, it need only be worded in general terms. It should, however, outlaw frameless vacuum tankers. This has been included in proposals for the past nine years, but was omitted from the last draft.
Alternatively, if it is the HSE's objective to prevent accidents, then it might better concentrate its attentions on in-use operation of all vacuum tankers: not just those which carry substances that are classified as dangerous.
Over the past 10 years six people have died while working around vacuum tankers; four of them due to explosions caused by welding tanks that had not been de-gassed. Whale's managing director Mike Fisher stresses that "these are dangers posed by all vacuum tankers whether their contents are designated as dangerous substances or not. This point has been ignored by the HSE".
The real danger arises when regular maintenance and inspection are neglected. The regulations do incorporate a code for inspection, and again this could be improved to cover all vacuum tankers. It would be difficult to discount the obvious safety advantages on a cost-benefit basis.
Since the beginning of 1985 only hazardous waste vacuum tankers have had to comply with Regulation 7 of the Dangerous Substances Regulations. This requires the operator to have his tankers examined and tested, in accordance with his own written scheme, by a nominated specialist. It is recommended these tests should be annual, and should include a visual inspection for cracks on the interior and exterior of the tank barrel. Tank fittings such as valves and pipework also need to be checked for leaks, and the tank mountings for their security; not forgetting the safe operation of the door and manhole clamps.
An operational test of the pump should be made to show up faults with the pressure relief valve and inlet/outlet valves as well as the doors and manholes.
Using ultrasonic measuring equipment the tank's skin, end and door thicknesses should be checked at 180mm intervals. The corrosive element of waste products invariably eats away at the metal, and if left unchecked full vacuum can eventually cause the tank to implode.
Whale tests about 40 vehicles every month for operators. Using a computer, it can provide a calculation on the strength of the tank and the pressure it can safely withstand.
After a thorough interior wash a complete safety check can be completed in about 1.5 hours for some 250 plus VAT. Whale is also able to recommend any preventative maintenance and repairs that are needed and provides an inspection and test certificate.
LI by Bill Brock