Ford takes on board a Cargo of new ideas
Page 70
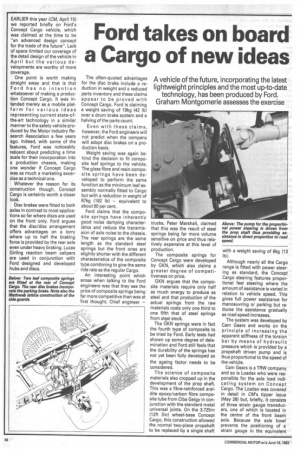
Page 71
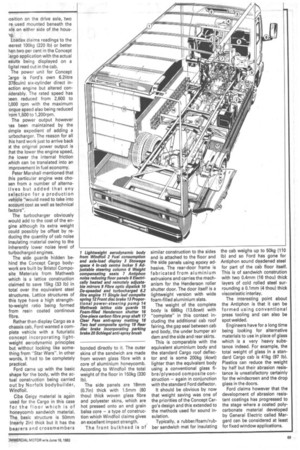
If you've noticed an error in this article please click here to report it so we can fix it.
A vehicle of the future, incorporating the latest lightweight principles and the most up-to-date technology, has been produced by Ford. Graham Montgomerie assesses the exercise
EARLIER this year (CM, April 15) we reported briefly on Ford's Concept Cargo vehicle, which was claimed at the time to be "an advanced design concept for the trade of the future". Lack of space limited our coverage of the detail design of the vehicle in April but the various developments are worthy of more coverage.
One point is worth making straight away and that is that Ford has no intention whatsoever of making a production Concept Cargo. It was intended merely as a mobile platform for various ideas representing current state-ofthe-art technology in a similar manner to the safety vehicle produced by the Motor Industry Research Association a few years ago. Indeed, with some of the features, Ford was noticeably reticent about predicting a time scale for their incorporation into a production chassis, making one wonder if Concept Cargo was as much a marketing excercise as a technical one.
Whatever the reason for its construction though, Concept Cargo is certainly worth a closer look.
Disc brakes were fitted to both axles in contrast to most applications so far where discs are used on the front only. Ford argues that the disc/disc arrangement offers advantages on a lorry where up to half the braking force is provided by the rear axle even under heavy braking. Lucas Girling reaction beam calipers are used in conjunction with Ford designed and developed hubs and discs. The often-quoted advantages for the disc brake include a reduction in weight and a reduced parts inventory and these claims appear to be proved with Concept Cargo. Ford is claiming a weight saving of 19kg (42 lb) over a drum brake system and a halving of the parts count.
Even with these claims, however, the Ford engineers will not predict when the company will adopt disc brakes on a production basis.
Weight saving was again behind the decision to fit composite leaf springs to the vehicle. The glass fibre and resin composite springs have been developed to perform the same function as the minimum leaf assembly normally fitted to Cargo but with a reduction in weight of 87kg (192 lb) — equivalent to about 60 per cent.
Ford claims that the composite springs have inherently good noise damping characteristics and reduce the transmission of axle noise to the chassis. The rear springs are the same length as the standard steel springs but the front ones are slightly shorter with the different characteristics of the composite type combining to give the same ride rate as the regular Cargo.
An interesting point which arose when talking to the Ford engineers was that they see the price of composite springs being far more competitive than was at first thought. Chief engineer — trucks, Peter Marshall, claimed that this was the result of steel springs being far more volume sensitive on price and thus relatively expensive at this level of production.
The composite springs for Concept Cargo were developed by GKN, which also claims a greater degree of corn petitiveness on price.
GKN argues that the composite materials require only half as much energy to produce as steel and that production of the actual springs from the raw materials costs only one third to one fifth that of steel springs from steel stock.
The GKN springs were in fact the fourth type of composite to be tried by Ford. Early tests had shown up some degree of delamination and Ford still feels that the durability of the springs has not yet been fully developed as the ageing factor needs to be considered.
The science of composite materials also cropped up in the development of the prop shaft. This was a fibre-reinforced araldite epoxy/carbon fibre composite tube from Ciba Geigy in conjunction with the standard metal universal joints. On the 3.725m (12ft 3in) wheel-base Concept Cargo, this construction allowed the normal two-piece propshaft to be replaced by a single shaft with a weight saving of 6kg (13 lb).
Although nearly all the Cargo range is fitted with power steering as standard, the Concept Cargo steering features proportional feel steering where the amount of assistance is varied in relation to vehicle speed. This gives full power assistance for manoeuvring or parking but reduces the assistance gradually as road speed increases.
The system was developed by Cam Gears and works on the principle of increasing the apparent stiffness of the torsion bar by means of hydraulic pressure which is provided by a propshaft driven pump and is thus proportional to the speed of the vehicle.
Cam Gears is a TRW company and so is Loadax who were responsible for the axle load indicating system on Concept Cargo. The Loadax was covered in detail in CM's tipper issue (May 28) but, briefly, it consists of three strain gauge transducers, one of which is located in the centre of the front beam axle, Because the axle bowl prevents the positioning of a strain gauge in the equivalent )osition on the drive axle, two re used mounted beneath the xle on either side of the hous Loadax claims readings to the learest 100kg (220 lb) or better han two per cent in the Concept :argo application with the actual esults being displayed on a ligital read out in the cab.
The power unit for Concept :ergo is Ford's own 6.2Iitre 378cuin) six-cylinder direct inection engine but altered con;iderably. The rated speed has 3een reduced from 2,600 to ?.,000 rpm with the maximum :orque speed also being reduced :rom 1,500 to 1,200rpm.
The power output however las been maintained by the iimple expedient of adding a :urbocharger. The reason for all this hard work just to arrive back at the original power output is that the lower the engine speed, the lower the internal friction which can be translated into an improvement in fuel economy.
Peter Marshall mentioned that this particular engine was chosen from a number of alternatives but added that any selection for a production vehicle "would need to take into account cost as well as technical factors".
The turbocharger obviously would add to the cost of the engine although its extra weight could possibly be offset by reducing the quantity of cab noise insulating material owing to the inherently lower noise level of turbocharged engines.
The side guards hidden behind the Concept Cargo bodywork are built by Bristol Composite Materials from Mathweb which is a lattice construction claimed to save 15kg (33 lb) in total over the equivalent steel structures. Lattice structures of this type have a high strengthto-weight ratio being formed from resin coated continous fibre.
Rather than display Cargo as a chassis cab, Ford wanted a complete vehicle with a futuristic concept incorporating lightweight aerodynamic principles but without looking like something from "Star Wars". In other words, it had to be completely practical.
Ford came up with the basic shape for the body, with the actual construction being carried out by Norfolk bodybuilder, Windfoil.
Ciba Geigy material is again used for the Cargo in this case for the floor which is of honeycomb sandwich material. The basic structure is 50mm (nearly 2in) thick but it has the bearers and crossmembers bonded directly to it. The outer skins of the sandwich are made from woven glass fibre with a core of aluminium honeycomb. According to Windfoil the total weight of the floor in 150kg (330 lb).
The side panels are 18mm (0.7in) thick with 1.5mm (60 thou) thick woven glass fibre and polyester skins, which are hot pressed onto an end grain balsa core — a type of construction which Windfoil claims gives an excellent impact strength.
The front bulkhead is of similar construction to the sides and is attached to the floor and the side panels using epoxy adhesive. The rear-door frame is fabricated from aluminium extrusions and carries the mechanism for the Henderson roller shutter door. The door itself is a lightweight version with wide foam-filled aluminium slats.
The weight of the complete body is 686kg (13.6cwt) with "complete" in this context including the additional cab roof fairing, the gap seal between cab and body, the under bumper air dam and the side and rear skirts.
This is comparable with the equivalent aluminium body and the standard Cargo roof deflector and is some 200kg (4cwt) lighter than the equivalent body using a conventional glass fibre/plywood composite construction — again in conjunction with the standard Ford deflector.
It should be obvious by now that weight saving was one of the priorities of the Concept Cargo's design and this extended to the methods used for sound insulation.
Typically, a rubber/foam/rubber sandwich mat for insulating the cab weighs up to 50kg (110 lb) and so Ford has gone for Antiphon sound deadened steel for part of the cab floor itself. This is of sandwich constrution with two 0.4mm (16 thou) thick layers of cold rolled steel surrounding a 0.1mm (4 thou) thick viscoelastic interlay.
The interesting point about the Antiphon is that it can be formed using conventional press tooling and can also be spot welded.
Engineers have for a long time being looking for alternative materials to use in place of glass which is a very heavy substance indeed. For example, the total weight of glass in a standard Cargo cab is 41kg (97 lb). Plastics can reduce the weight by half but their abrasion resistance is unsatisfactory certainly for the windscreen and the drop glass in the doors.
Ford claims however that the development of abrasion resistant coatings has progressed to the stage where a coated polycarbonate material developed by General Electric called Margard can be considered at least for fixed window applications.