Preventive maintenance: the PPM system of A. Packham and Co. Ltd.
Page 67
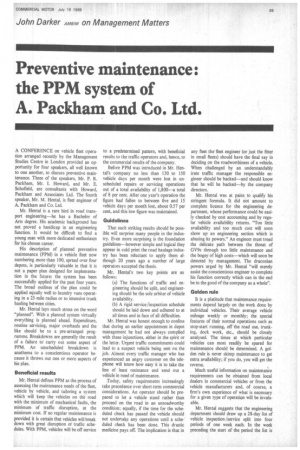
Page 68
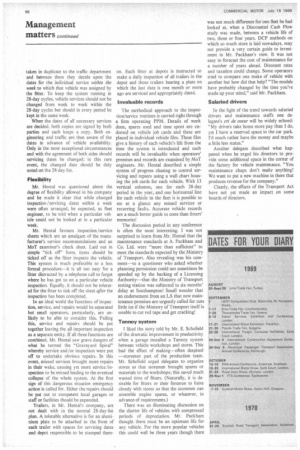
If you've noticed an error in this article please click here to report it so we can fix it.
A CONFERENCE on vehicle fleet operation arranged recently by the Management Studies Centre in London provided an opportunity for four speakers, all well known to one another, to discuss preventive maintenance. Three of the speakers. Mr. P. R. Packham, Mr. I. Howard, and Mr. E. Schofield. are consultants with Howard, Packham and Associates Ltd. The fourth speaker, Mr. M. Hental. is fleet engineer of A. Packham and Co. Ltd.
Mr. Hental is a rare bird in road transport engineering—he has a Bachelor of Arts degree. His academic background has not proved a handicap in an engineering function. It would be difficult to find a young man with more dedicated enthusiasm for his chosen career.
His description of planned preventive maintenance (PPM) in a vehicle fleet now numbering more than 100. spread over four depots, is particularly valuable in that it is not a paper plan designed for implementation in the future: the system has been successfully applied for the past four years. The broad outlines of the plan could be applied equally well to laundry vans operating in a 25-mile radius or to intensive trunk hauling between cities.
Mr. Hental lays much stress on the word "planned". With a planned system virtually everything is planned ahead. Expenditure, routine servicing, major overhauls and the like should be to a pre-arranged programme. Breakdowns are generally the result of a failure to carry out some aspect of PPM. An unscheduled breakdown is anathema to a conscientious operator because it throws out one or more aspects of his plan.
Beneficial results Mr. Hental defines PPM as the process of assessing the maintenance needs of the fleet, vehicle by vehicle, and tailoring a system which will keep the vehicles on the road with the minimum of mechanical faults, the minimum of traffic disruption, at the minimum cost. If no regular maintenance is provided it is certain that vehicles will break down with great disruption ot traffic schedules. With PPM, vehicles will be off service
to a predetermined pattern, with beneficial results to the traffic operators and, hence, to the commercial results of the company.
Before PPM was introduced in Mr. Hental's company no less than 130 to 150 vehicle days per month were lost in unscheduled repairs or servicing operations out of a total availability of l.800—a total of 8 per cent. After one year's operation the figure had fallen to between five and 15 vehicle days per month lost, about 0.57 per cent, and this low figure was maintained.
Guidelines
That such striking results should be possible will surprise many people in the industry. Even more surprising is the foundation guidelines—however simple and logical they appear in cold print the road haulage industry has been reluctant to apply them although 20 years ago a number of large operators accepted the thesis.
Mr. Hental's two key points are as follows: (a) The functions of traffic and engineering should be split, and engineering should be the sole arbiter of vehicle availability.
(b) A rigid service/inspection schedule should be laid down and adhered to at all times and in face of all difficulties.
Mr. Hental was honest enough to confess that during an earlier appointment in depot management he had not always complied with these injunctions, either in the spirit or the letter. Urgent traffic commitments could lead to a suspect vehicle being sent on the job. Almost every traffic manager who has experienced an angry customer on the telephone will know how easy it is to take the line of least resistance and send out a vehicle in need of maintenance.
Today, safety requirements increasingly take precedence over short-term commercial considerations. An operator should be prepared to let a vehicle stand rather than proceed on the road in an unroadworthy condition; equally, if the time for the scheduled check has passed the vehicle should not undertake any operations until a sche-' duled check has been done. This drastic medicine pays off. The implication is that in any fleet the fleet engineer (or just the fitter in small fleets) should have the final say in deciding on the roadworthiness of a vehicle. When challenged by an understandably irate traffic manager the responsible engineer should be backed—and should know that he will be backed—by the company directors.
Mr. Hental was at pains to qualify his stringent formula. It did not amount to complete licence for the engineering department, whose performance could be easily checked by cost accounting and by regular vehicle availability returns. "Too little availability and too much cost will soon show up an engineering section which is abusing its powers." An engineer must tread the delicate path between the threat of GV9s through too little maintenance and the bogey of high costs—which will soon be detected by management. The draconian powers urged by Mr. Hental "will merely assist the conscientious engineer to complete his function correctly which can in the end be to the good of the company as a whole".
Golden rule
It is a platitude that maintenance requirements depend largely on the work done by individual vehicles. Their average vehicle mileage weekly or monthly; the special features of their normal operations such as stop-start running, off the road use, trunking, dock work, etc., should be closely analysed. The times at which particular vehicles can most readily be spared for maintenance should be determined. A golden rule is never skimp maintenance to get extra availability; if you do, you will get the reverse.
Much useful information on maintenance requirements can be obtained from local dealers in commercial vehicles or from the vehicle manufacturers and, of course, a firm's own experience of what is necessary for a given type of operation will be invaluable.
Mr. Hental suggests that the engineering department should draw up a 28-day list of vehicle inspection /service split into four periods of one week each. In the week preceding the start of the period the list is
taken in duplicate to the traffic department and between them they decide upon the dates for the individual service within the week to which that vehicle was assigned by the fitter. To keep the system running in 28-day cycles, vehicle services should not be changed from week to week within the 28-day cycles but should in every period be kept in the same week.
When the dates of all necessary services are decided, both copies are signed by both parties and each keeps a copy. Both engineering and traffic are then aware of the dates in advance of vehicle availability. Only in'the most exceptional circumstances and with the agreement of both sides should servicing dates be changed; in this rare event, the changed date should be duly noted on the 28-day list.
Flexibility
Mr. Hental was questioned about the degree of flexibility allowed in his company and he made it clear that while changed inspection /servicing dates within a week were often arranged, he expected, as fleet engineer, to be told when a particular vehicle could not be looked at in a particular week.
Mr. Hental favours inspection /service sheets which are an amalgam of the manufacturer's service recommendations and an MoT examiner's check sheet. Laid out in simple "tick or form, items should be ticked off as the fitter inspects the vehicle. This system is much preferable to a less formal procedure—it is all too easy for a fitter distracted by a telephone call to forget where he has got to on a particular vehicle inspection. Equally, it should not be tolerated for the fitter to tick off the sheet after the inspection has been completed.
In an ideal world the functions of inspection, service, and repairs would be separated but small operators, particularly, are unlikely to be able to consider this. Failing this, service and repairs should be put together leaving the all important inspection as a separate entity. If all three functions are combined, Mr. Rental saw grave dangers of what he termed the "Graveyard Spiral" whereby service and/or inspection were put off to undertake obvious repairs. In this event, missed services brought more repairs in their wake, causing yet more service/inspection to be missed leading to the eventual collapse of the whole system. At the first sign of this dangerous situation emergency action is called for. Either the repairs should be put out to competent local garages or staff or facilities sliould be expanded.
Trailers, in Mr. Hanes company, are not dealt with in the normal 28-day-list plan. A tolerable alternative is for an aluminium plate to be attached to the front of each trailer with spaces for servicing dates and depot responsible to be stamped there on. Each fitter at depots is instructed to make a daily inspection of all trailers in the depot and those trailers bearing a plate on which the last date is one month or more ago are serviced and appropriately dated.
Invaluable records
The methodical approach to the inspection/service routines is carried right through a firm operating PPM. Details of work done, spares used and time spent are endorsed on vehicle job cards and these are placed in individual vehicle files. These files give a history of each vehicle's life from the time the system is introduced and such records will be invaluable when operators' premises and records are examined by MoT engineers. Mr. Hental described a simple system of progress chasing to control servicing and repairs using a wall chart housing the job cards for each vehicle. With 13 vertical columns, one for each 28-day period in the year, and one horizontal line for each vehicle in the fleet it is possible to see at a glance any missed services or recurring faults. Accurate vehicle records are a much better guide to costs than fitters' memories!
The discussion period in any conference is often the most interesting. I was not surprised to learn from Mr. Hental that the maintenance standards at A. Peckham and Co. Ltd. were "more than sufficient" to meet the standards expected by the Ministry of Transport. Also revealing was his com ment—to a questioner who asked whether planning permission could not sometimes be speeded up by the backing of a Licensing Authority—that the Ministry of Transport testing station was subjected to six months' delay at Southampton! Small wonder that an endorsement from an LA that new maintenance premises are urgently called for cuts little ice if the Ministry of Transport itself is unable to cut red tape and get cracking!
Tenney system
I liked the story told by Mr. E. Schofield of the dramatic improvement in preductivity when a garage installed a Tannoy system between vehicle workshops and stores. This had the effect of making—often despised —storemen part of the production team. Mr. Schofield urged delegates to organize stores so that storemen brought spares or materials to the workshops; this saved much wasted time of fitters. (Naturally, it is desirable for fitters or their foremen to liaise closely with stores so that the storemen can assemble engine spares, or whatever, in advance of requirements.) There was an illuminating discussion on the shorter life of vehicles with compressed periods of depreciation. Mr. Packham thought there must be an optimum life for any vehicle. For the more popular vehicles this could well be three years though there was not much difference for one fleet he had looked at, when a Discounted Cash Flow study was made, between a vehicle life of two, three or four years. DCF methods on which so much store is laid nowadays, may not provide a very certain guide to investment in Mr. Packham's view. It was not easy to forecast the cost of maintenance for a number of years ahead. Discount rates and taxation could change. Some operators tried to compare one make of vehicle with another but how did that help? "The models have probably changed by the time you've made up your mind," said Mr_ Packham.
Salaried drivers
In the light of the trend towards salaried drivers and maintenance staffs one delegate's cri de coeur will be widely echoed: "My drivers take home more pay than I do, yet I have a reserved space in the car park. I'd much rather have the money and maybe a little less status."
Another delegate described what happened when he urged his directors to provide some additional space in the corner of the factory for vehicle maintenance. "You maintenance chaps don't make anything! We want to put a new machine in there that produces revenue for the company."
Clearly, the effects of the Transport Act have not yet made an impact on some boards of directors.