Beating
Page 58
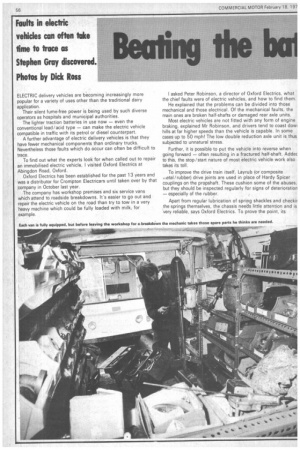
Page 59
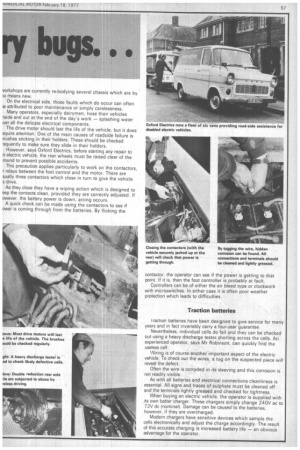
If you've noticed an error in this article please click here to report it so we can fix it.
tite bid
ry bugs. .
ELECTRIC delivery vehicles are becoming increasingly more popular for a variety of uses other than the traditional dairy application.
Their silent fume-free power is being used by such diverse operators as hospitals and municipal authorities.
The lighter traction batteries in use now — even the conventional lead/acid type — can make the electric vehicle compatible in traffic with its petrol or diesel counterpart.
A further advantage of electric delivery vehicles is that they have fewer mechanical components than ordinary trucks. Nevertheless those faults which do occur can often be difficult to trace.
To find out what the experts look for when called out to repair an immobilised electric vehicle, I visited Oxford Electrics at Abingdon Road, Oxford. Oxford Electrics has been established for the past 13 years and was a distributor for Crompton Electricars until taken over by that .company in October last year.
The company has workshop premises and six service vans which attend to roadside breakdowns. It's easier to go out and repair the electric vehicle on the road than try to tow in a very heavy machine which could be fully loaded with milk, for example. I asked Peter Robinson, a director of Oxford Electrics, what the chief faults were of electric vehicles, and how to find them.
He explained that the problems can be divided into those mechanical and those electrical. Of the mechanical faults, the main ones are broken half shaftsor damaged rear axle units.
Most electric vehicles are not fitted with any form of engine braking, explained Mr Robinson, and drivers tend to coast dowi hills at far higher speeds than the vehicle is capable. In some cases up to 50 mph! The low double reduction axle unit is thus subjected to unnatural stress.
Further, it is possible to put the vehicle into reverse when going forward — often resulting in a fractured half-shaft. Addec to this, the stop/start nature of most electric vehicle work also takes its toll.
To improve the drive train itself, Layrub (or composite wetal/rubber) drive joints are used in place of Hardy Spicer couplings on the propshaft. These cushion some of the abuses, but they should be inspected regularly for signs of deterioration — especially of the rubber.
Apart from regular lubrication of spring shackles and checkir the springs themselves, the chassis needs little attention and is very reliable, says Oxford Electrics. To prove the point, its vorkshops are currently re-bodying several chassis which are by io means new.
On the electrical side, those faults which do occur can often )e attributed to poor maintenance or simply carelessness.
Many operators, especially dairymen, hose their vehicles iside and out at the end of the day's work — splashing water iver all the delicate electrical components.
The drive motor should last the life of the vehicle, but it does equire attention. One of the main causes of roadside failure is gushes sticking in their holders. These should be checked -equently to make sure they slide in their holders.
However, says Oxford Electrics, before starting any repair to n electric vehicle, the rear wheels must be raised clear of the round to prevent possible accidents.
This precaution applies particularly to work on the contactors, r relays between the foot control and the motor. There are sually three contactors which close in turn to give the vehicle s drive.
As they close they have a wiping action which is designed to eep the contacts clean, provided they are correctly adjusted. If owever, the battery power is down, arcing occurs.
A quick check can be made using the contactors to see if ower is coming through from the batteries. By flicking the contactor, the operator can see if the power is getting to that point. If it is, then the foot controller is probably at fault.
Controllers can be of either the air bleed type or clockwork with microswitches. In either case it is often poor weather protection which leads to difficulties.
Traction batteries
I raction batteries have been designed to give service for many years and in fact invariably carry a four-year guarantee.
Nevertheless, individual cells do fail and they can be checked out using a heavy discharge tester shorting across the cells. An experienced operator, says Mr Robinson, can quickly find the useless cell.
Wiring is of course another important aspect of the electric vehicle. To check out the wires, a tug on the suspected piece will reveal the defect.
Often the wire is corroded in its sleeving and this corrosion is not readily visible.
As with all batteries and electrical connections cleanliness is essential. All signs and traces of sulphate must be cleaned off and the terminals lightly greased and checked for tightness.
When buying an electric vehicle, the operator is supplied with its own batter charger. These chargers simply change 240V ac to 72V dc (nominal). Damage can be caused to the batteries, however, if they are overcharged.
Modern chargers have sensitive devices which sample the cells electronically and adjust the charge accordingly. The result of this accurate charging is increased battery life — an obvious advantage for the operator.