By P. A. C. Brockingion, A.M.I.Mech.E.
Page 34
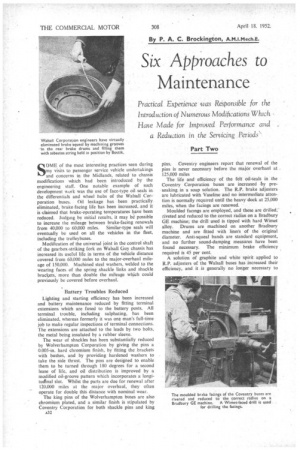
Page 35
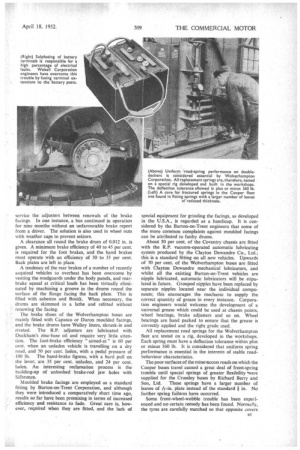
Page 36
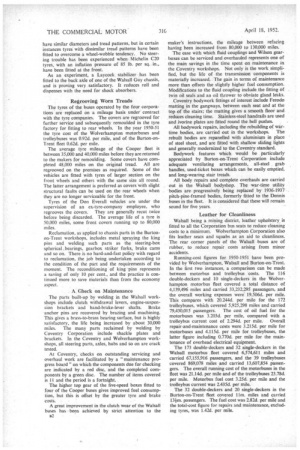
If you've noticed an error in this article please click here to report it so we can fix it.
Six Approaches to Maintenanceā¢
Practical Experience was Responsible for the Introduction of Numerous Modifications Which Have Made for Improved Performance and a Reduction in the Servicing Periods'
Part Two SOME of the most interesting practices seen during my visits to passenger service vehicle undertakings and concerns in the Midlands, related to chassis modifications which had been introduced by the engineering staff. One notable example of such development work was the use of face-type oil seals in the differentials and wheel hubs of the Walsall Corporation buses, Oil leakage has been practically eliminated, brake-facing life has been increased, and it is claimed that brake-operating temperatures have been reduced. Judging by initial results, it may be possible to increase the mileage between brake-facing renewals
from 40,000 to 60,000 miles. Similar-type seals will eventually be used on all the vehicles in the fleet, including the trolleybuses.
Modification of the universal joint in the control shaft of the gearbox-striking fork on Walsall Guy chassis has increased its useful life in terms of the vehicle distance covered from 60,000 miles to the major-overhaul mileage of 150,000. Machined steel washers, welded to the wearing faces of the spring shackle links and shackle brackets, more than double the mileage which could previously be covered before overhaul.
Battery Troubles Reduced
Lighting and starting efficiency has been increased and battery maintenance reduced by fitting terminal extensions which are fused to the battery posts. All terminal trouble, including sulphating, has been eliminated, whereas formerly it was one man's full-time job to make regular inspections of terminal connections. The extensions are attached to the leads by two bolts, the metal being insulated by a rubber sleeve.
The wear of shackles has been substantially reduced by Wolverhampton Corporation by giving the pins a 0.005-in, hard chromium finish, by fitting the brackets with bushes, and by providing hardened washers to take the side thrust. The pins are designed to enable them to be turned through 180 degrees for a second lease of life, and oil distribution is improved by a modified oil-groove pattern which incorporates a longitudinal slot. Whilst the parts are due for renewal after 120,000 miles at the major overhaul, they often operate for double this distance with nominal wear.
The king pins of the Wolverhampton buses are also chromium plated, and a similar finish is stipulated by Coventry Corporation for both shackle pins and king A32 pins. Coventry engineers report that renewal of the pins is never necessary before the major overhaul at 125,000 miles The life and efficiency of the felt oil-seals in the Coventry Corporation buses are increased by presoaking in a soap solution. The R.P. brake adjusters are lubricated with Vaseline and no intermediate attention is normally required until the heavy dock at 25,000 miles, when the facings are renewed.
Moulded facings are employed, and these are drilled, riveted and reduced to the correct radius on a Bradbury GE machine; the drill used is tipped with hard Wimet alloy. Drums are machined on another Bradbury machine and are fitted with liners of the original diameter. Anti-squeal bands are standard equipment, and no further sound-damping measures have been found necessary. The minimum brake efficiency required is 45 per cent.
A solution of graphite and white spirit applied to R.P. adjusters of the Walsall buses has increased their efficiency, and it is generally no longer necessary to service the adjusters between renewals of the brake facings. In one instance, a bus continued in operation for nine months without an unfavourable brake report from a driver. The solution is also used in wheel nuts with weather caps to prevent seizure.
A clearance all round the brake drum of 0.012 in. is given. A minimum brake efficiency of 40 to 45 per cent. is required for the foot brakes, and the hand brakes must operate with an efficiency of 30 to 35 per cent. Back plates are left in place.
A tendency of the rear brakes of a number of recently acquired vehicles to overheat has been overcome by venting the mudguards under the body panels, and rearbrake squeal at critical loads has been virtually eliminated by machining a groove in the drums round the surface of the flange facing the back plate. This is filled with asbestos and Bostik. When necessary, the drums are skimmed in a lathe and refitted without renewing the facing.
The brake shoes of the Wolverhampton buses are mainly fitted with Capasco or Duron moulded facings, and the brake drums have Walloy liners, shrunk-in and riveted. The R.P. adjusters are lubricated with Duckham's zinc-base oil and require very little attention. The foot-brake efficiency " aimed-at " is 60 per cent. when an unladen vehicle is travelling on a dry road, and 50 per cent. laden, with a pedal pressure of 100 lb. The hand-brake figures, with a hard pull on the lever, are 35 per cent. unladen, and 24 per cent. laden. An interesting reclamation process is the building-up of uribushed brake-rod jaw holes with S ifbronze.
Moulded brake facings are employed as a standard fitting by Burton-on-Trent Corporation, and although they were introduced a comparatively short time ago, results so far have been promising in terms of increased efficiency and resistance to fade. Great care is, however, required when they are fitted, and the lack of
special equipment for grinding the facings, as developed in the U.S.A., is regarded as a handicap. It is considered by the Burton-on-Trent engineers that some of the more common complaints against moulded facings can be attributed to faulty drums.
About 50 per cent, of the Coventry chassis are fitted with the R.P. vacuum-operated automatic lubricating system produced by the Clayton Dewandre Co., Ltd.; this is a standard fitting on all new vehicles. Upwards of 70 per cent. of the Wolverhampton buses are fitted with Clayton Dewandre mechanical lubricators, and whilst all the existing Burton-on-Trent vehicles are nipple lubricated, automatic lubricators will be stipulated in future. Grouped nipples have been replaced by separate nipples located near the individual components; this encourages the mechanic to supply the correct quantity of grease in every instance. Corporation engineers would welcome the development of a universal grease which could be used at chassis points, wheel bearings, brake adjusters and so on. Wheel bearings are hand packed to ensure that the grease is correctly applied and the right grade used.
All replacement road springs for the Wolverhampton fleet are tested on a rig, developed in the workshops. Each spring must have a deflection tolerance within plus or minus 560 lb. It is considered that uniform spring performance is essential in the interests of stable roadbehaviour characteristics.
The poor surfaces of the mine-access roads on which the Cooper buses travel caused a great deal of front-spring trouble until special springs of greater flexibility 'were supplied for the Crossley buses by Richard Berry and Son, Ltd. These springs have a larger number of leaves of 1.5-6--in. plate instead of the standard in. No further spring failures have occurred.
Some front-wheel-wobble trouble has been experienced and no certain remedy has been found. Normally, the tyres are carefully matched so that opposite covers 131 have similar diameters and tread patterns, but in certain instances tyres with dissimilar tread patterns have been fitted to overcome a wheel-wobble tendency. No steering trouble has been experienced when Michelin C20 tyres, with an inflation pressure of 85 lb. per sq. in., have been fitted at the front.
As an experiment, a Laycock stabilizer has been fitted to the back axle of one of the Walsall Guy chassis, and is proving very satisfactory. It reduces roll and dispenses with the need for shock absorbers.
Regrooving Worn Treads The tyres of the buses operated by the four corporations are replaced on a mileage basis under contract with the tyre companies. The covers are regrooved for further service and subsequently remoulded in the tyre factory for fitting to rear wheels. In the year 1950-51 the tyre cost of the Wolverhampton motorbuses and trolleybuses was 0.92d. per mile, and of the Burton-onTrent fleet 0.62d. per mile.
The average tyre mileage of the Cooper fleet is between 35,000 and 40,000 miles before they are returned to the makers for remoulding. Some covers have completed 48,000 miles on the original tread. All are regrooved on the premises as required. Some of the vehicles are fitted with tyres of larger section on the front wheels and others with the same size all round. The latter arrangement is preferred as covers with slight structural faults can be used on the rear wheels when they are no longer serviceable for the front.
Tyres of the Don Everall vehicles are under the supervision of an ex-tyre-company employee, who regrooves the covers. They are generally recut twice before being discarded. The average life of a tyre is 50.000 miles, some front covers running up to 80,000 miles.
Reclamation, as applied to chassis parts in the Burtonon-Trent workshops, includes metal spraying the king pins and welding such parts as the steering-box spherical ,bearings, gearbox striker forks, brake cams and so on. There is no hard-and-fast policy with regard to reclamation, the job being undertaken according to the condition of the part and the requirements of the moment. The reconditioning of king pins represents a saving of only 10 per cent., and the practice is continued more to save materials than from the economy aspect.
A. Check on Maintenance The parts built-up by welding in the Walsall workshops include clutch withdrawal levers, engine-suspension brackets and hand-brake-lever shafts. Brake anchor pins are recovered by brazing and machining. This gives a brass-to-brass bearing surface, but is highly satisfactory, the life being increased by about 30,000 miles. The many parts reclaimed by welding by Coventry Corporation include shackle plates and brackets. In the Coventry and Wolverhampton workshops, all steering parts, axles, hubs and so on are crack tested.
At Coventry, checks on outstanding servicing and overhaul work are facilitated by a " maintenance progress board" on which the components due for checking are indicated by a red disc, and the completed components by a green disc. The number of items covered is 11 and the period is a fortnight.
The higher top gear of the five-speed boxes fitted to four of the Cooper buses gives improved fuel consumption, but this is offset by the greater tyre and brake costs.
A great improvement in the clutch wear of the Walsall buses has been achieved by strict attention to the B2 maker's instructions, the mileage between refacing having been increased from 80,000 to 130,000 miles.
The ease with which fluid couplings and Wilson gearboxes can be serviced and overhauled represents one of the main savings in the time spent on maintenance in the Coventry workshops. Not only is the work simplified, but the life of the transmission components is materially increased. The gain in terms of maintenance more than offsets the slightly higher fuel consumption. Modifications to the fluid coupling include the fitting of twin oil seals and an oil thrower to obviate gland leaks.
Coventry bodywork fittings of interest include Ferodo matting in the gangways, between each seat and at the top of the stairs; the matting gives a smooth floor and reduces cleaning time. Stainless-steel handrails are used and ivorine plates are fitted round the bell pushes.
All bodywork repairs, including the rebuilding of wartime bodies, are carried out in the workshops. The rebuilt bodies are repanelled with aluminium in place of steel sheet, and are fitted with shallow sliding lights and generally modernized to the Coventry standard.
Bodywork features which would be particularly appreciated by Burton-on-Trent Corporation include adequate ventilating arrangements, all-steel grab handles, used-ticket boxes which can be easily emptied, and long-wearing stair treads.
All body repairs and complete overhauls are carried out in the Walsall bodyshop. The war-time utility bodies are progressively being replaced by 1936-1937 pitch-pine-framed bodies, formerly fitted to the Dennis buses in the fleet. It is considered that these will remain sound for five years.
Leather for Cleanliness Walsall being a mining district, leather upholstery, is fitted to all the Corporation bus seats to reduce cleaning costs to a minimum. Wolverhampton Corporation also fits leather seats and squabs as an aid to cleanliness. The rear corner panels of the Walsall buses are of rubber, to reduce repair costs arising from minor accidents.
Running-cost figures for 1950-1951 have been provided by Wolverhampton, Walsall and Burton-on-Trent. In the first two instances, a comparison can be made between motorbus and trolleybus costs. The 116 double-deckers and 10 single-deckers in the Wolverhampton motorbus fleet covered a total distance of 4,139,496 miles and carried 33,232,295 passengers, and the overall working expenses were 19.506d. per mile. This compares with 20.244d. per mile for the 172 trolleybuses, which covered 5,925,298 miles and carried 79,430,015 passengers. The cost of oil fuel for the motorbuses was 3.203d. per mile, compared with a trolleybus current cost of 2.294d. per mile. Overall repair-and-maintenance costs were 3.215d. per mile for motorbuses and 4.115d. per mile for trolleybuses, the latter figure including 0.770d. per mile for the maintenance of overhead electrical equipment.
The 173 double-deckers and 32 single-deckers in the Walsall motorbus fleet covered 6,574,611 miles and carried 67,155,916 passengers, and the 39 trolleybuses covered 869,078 miles and carried 13,607,854 passengers. The overall running cost of the motorbuses in the fleet was 21.14d. per mile and of the trolleybuses 23.78d. per mile. Motorbus fuel cost 3.25d. per mile and the trolleybus current was 2.435d. per mile.
The 32 double-deckers and 20 single-deckers in the Burton-on-Trent fleet covered 14m. miles and carried 131m. passengers. The fuel cost was 2.82d. per mile and the total-cost figure for repairs and maintenance, excluding tyres, was 1.42d. per mile.