Stop transport killing
Page 63
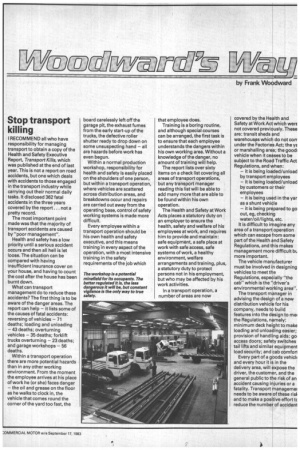
If you've noticed an error in this article please click here to report it so we can fix it.
I RECOMMEND all who have responsibility for managing transport to obtain a copy of the Health and Safety Executive Report, Transport Kills, which was published at the end of last year. This is not a report on road accidents, but one which deals with accidents to those engaged in the transport industry while carrying out their normal daily tasks. It disclosed 362 fatal accidents in the three years covered by the report ... not a pretty record.
The most important point made was that the majority of transport accidents are caused by "poor management".
Health and safety has a low priority until a serious accident occurs and then all hell is let loose. The situation can be compared with having insufficient insurance cover on your house, and having to count the cost after the house has been burnt down.
What can transport management do to reduce these accidents? The first thing is to be aware of the danger areas. The report can help — it lists some of the causes of fatal accidents: reversing of vehicles — 71 deaths; loading and unloading — 43 deaths; overturning vehicles — 35 deaths; forklift trucks overturning — 23 deaths; and garage workshops — 56 deaths.
Within a transport operation there are more potential hazards than in any other working environment. From the moment the employee arrives at his place of work he (or she) faces danger — the oil and grease on the floor as he walks to clock in, the vehicle that comes round the corner of the yard too fast, the board carelessly left off the garage pit, the exhaust fumes from the early start-up of the trucks, the defective roller shutter ready to drop down on some unsuspecting hand — all are hazards before work has even begun.
Within a normal production workshop, responsibility for health and safety is easily placed on the shoulders of one person, but within a transport operation, where vehicles are scattered across distribution areas, and breakdowns occur and repairs are carried out away from the operating base, control of safety working systems is made more difficult.
Every employee within a transport operation should be his own health and safety executive, and this means training in every aspect of the operation, with a most intensive training in the safety requirements of the job which that employee does.
Training is a boring routine, and although special courses can be arranged, the first task is to ensure that each employee understands the dangers within his own working area. Without a knowledge of the danger, no amount of training will help.
The report lists over sixty items on a check list covering all areas of transport operations, but any transport manager reading this list will be able to add many more that are able to be found within his own operation.
The Health and Safety at Work Acts places a statutory duty on an employer to ensure the health, safety and welfare of his employees at work, and requires him to provide and maintain: safe equipment, a safe place at work with safe access, safe systems of work, a healthy environment, welfare arrangements and training, plus, a statutory duty to protect persons not in his employment, but who may be affected by his work activities.
In a transport operation, a number of areas are now
covered by the Health and Safety at Work Act which werE not covered previously. These are: transit sheds and warehouses which do not conunder the Factories Act; the yz or marshalling area; the good vehicle when it ceases to be subject to the Road Traffic Act Regulations, and when:
— it is being loaded/unload by transport employees — it is being loaded/unload by customers or their employees — it is being used in the yar as a shunt vehicle — it is being prepared to go out, eg, checking water/oil/lights, etc.
It is difficult to imagine any area of a transport operation which can escape from some part of the Health and Safety Regulations, and this makes management more difficult more important.
The vehicle manufacturer must be involved in designing vehicles to meet the Regulations, especially "the cab" which is the "driver's environmental working area".
The transport manager in advising the design of a new distribution vehicle for his company, needs to build features into the design to mei the Regulations, namely: minimum deck height to make loading and unloading easier; provision of handling aids; go access doors; safety switches tail lifts and similar equipment load security; and cab comforl Every part of a goods vehicli and every hour it is in the delivery area, will expose the driver, the customer, and the general public to the risk of an accident causing injuries or a fatality. Transport managemer needs to be aware of these risk and to make a positive effort tc reduce the number of accident