The effects of legislation upon the design of heavy-duty truck engines
Page 68
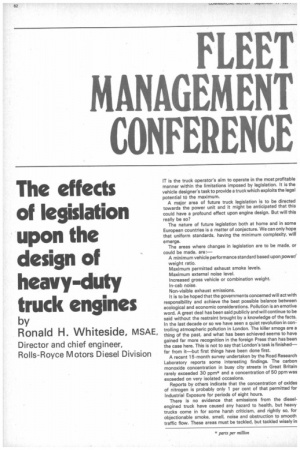
Page 69
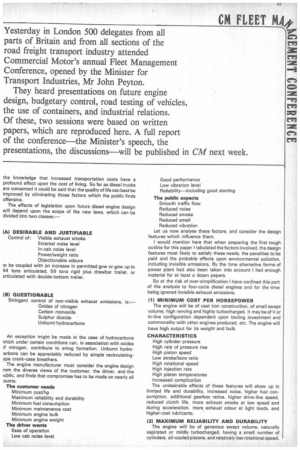
Page 70
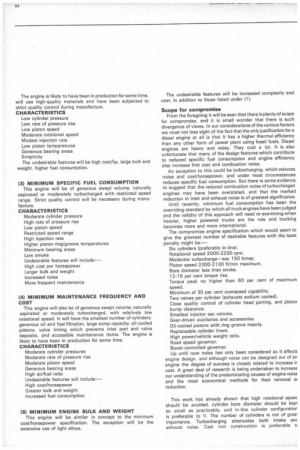
Page 71
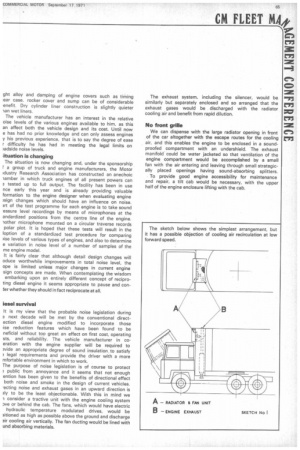
Page 72
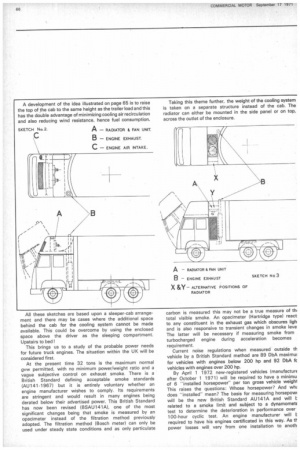
Page 73
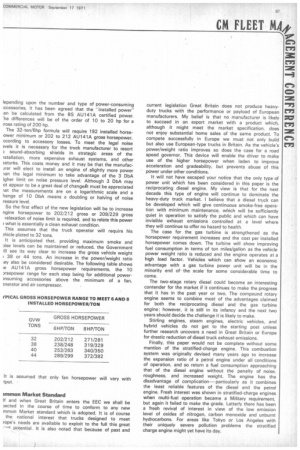
If you've noticed an error in this article please click here to report it so we can fix it.
by
Ronald H. Whiteside, MSAE,
Director and chief engineer, Rolls-Royce Motors Diesel Division
An exception might be made in the case of hydrocarbons vhich under certain conditions can, in association with oxides yf nitrogen, contribute to smog formation. Unburnt hydro :arbons can be appreciably reduced by simple recirculating ype crank-case breathers.
The engine manufacturer must consider the engine design rom the diverse views of the customer, the driver, and the iublic, and finds that compromise has to be made on nearly all ounts.
The customer needs Minimum cost/hp Maximum reliability and durability Minimum fuel consumption Minimum maintenance cost Good performance Low vibration level Reliability—including good starting The public expects Smooth traffic flow Reduced noise Reduced smoke Reduced smell Reduced vibration Let us now analyse these factors, and consider the design features which influence them.
I would mention here that when preparing the first rough outline for this paper I tabulated the factors involved, the design features most likely to satisfy these needs, the penalties to be paid and the probable effects upon environmental pollution, including invisible emissions. By the time alternative forms of power plant had also been taken into account I had enough material for at least a dozen papers.
So at the risk of over-simplification I have confined this part of the analysis to four-cycle diesel engines and for the time being ignored invisible exhaust emissions.
(1) MINIMUM COST PER HORSEPOWER The engine will be of cast iron construction, of small swept volume, high revving and highly turbocharged. It may be of V or in-line configuration dependent upon tooling investment and commonality with other engines produced, etc. The engine will have high output for its weight and bulk.
CHARACTERISTICS High cylinder pressure High rate of pressure rise High piston speed Low stroke/bore ratio High rotational speed High injection rate High piston temperatures Increased complication The undesirable effects of these features will show up in limited life and durability, increased noise, higher fuel con sumption, additional gearbox ratios, higher drive-line speed, reduced clutch life, more exhaust smoke at low speed and during acceleration, more exhaust odour at light loads, and higher-cost lubricants.
(2) MAXIMUM RELIABILITY AND DURABILITY The engine will be of generous swept volume, naturally aspirated or mildly turbocharged, having a small number of cylinders, oil-cooled pistons, and relatively low rotational speed. The undesirable features will be increased complexity and cost, in addition to those listed under
Scope for compromise
From the foregoing it will be seen that there is plenty of scope for compromise, and it is small wonder that there is such divergence of views. In our considerations of the various factors we must not lose sight of the fact that the only justification for a diesel engine at all is that it has a higher thermal efficiency than any other form of power plant using fossil fuels. Diesel engines are heavy and noisy. They cost a lot. It is also unfortunate that many of the design features which contribute to reduced specific fuel consumption and engine efficiency also increase first cost and combustion noise.
An exception to this could be turbocharging, which reduces noise and cost/horsepower, and under most circumstances reduces specific fuel consumption. But there is some evidence to suggest that the reduced combustion noise of turbocharged engines may have been overstated, and that the marked reduction in inlet and exhaust noise is of greatest significance.
Until recently, minimum fuel consumption has been the overriding standard by which all truck engines have been judged and the validity of this approach will need re-examining when heavier, higher powered trucks are the rule and trucking becomes more and more international.
The compromise engine specification which would seem to give the greatest number of desirable features with the least penalty might be:—
Six cylinders (preferably in-line).
Rotational speed 2000-2200 rpm.
Moderate turbocharge—say 150 bmep.
Piston speed 2000-2100 ft/min maximum.
Bore diameter less than stroke.
12-15 per cent torque rise.
Torque peak no higher than 60 per cent of maximum speed.
Minimum of 30 per cent overspeed capability.
Two valves per cylinder (exhausts sodium cooled).
Close quality control of cylinder head porting, and piston bump clearance.
Smallest injector sac volume.
Gear-driven auxiliaries and accessories.
Oil-cooled pistons with ring groove inserts.
Replaceable cylinder liners.
High power/vehicle weight ratio.
Road speed governor.
Boost-controlled governor.
Up until now noise has only been considered as it affectE engine design, and although noise can be designed out of an engine the degree of success is closely related to increase ir cost. A great deal of research is being undertaken to increasE our understanding of the predominating causes of engine noise and the most economical methods for their removal oi reduction.
This work has already shown that high rotational speec should be avoided, cylinder bore diameter should be kepi as small as practicable, and in-line cylinder configuratior is preferable to V. The number of cylinders is not of grea• importance. Turbocharging attenuates both intake anc exhaust noise. Cast iron construction is preferable ti
ght alloy and damping of engine covers such as timing ear case, rocker cover and sump can be of considerable enefit. Dry cylinder liner construction is slightly quieter -ian wet liners.
The vehicle manufacturer has an interest in the relative oise levels of the various engines available to him, as this an affect both the vehicle design and its cost. Until now e has had no prior knowledge and can only assess engines y his previous experience, that is to say the degree of ease r difficulty he has had in meeting the legal limits on iadside noise levels.
ituation is changing
The situation is now changing and, under the sponsorship a group of truck and engine manufacturers, the Motor idustry Research Association has constructed an anechoic lamber in which truck engines of all present powers can a tested up to full output. The facility has been in use nce early this year and is already providing valuable formation to the engine designer when evaluating engine :sign changes which should have an influence on noise. 1rt of the test programme for each engine is to take sound essure level recordings by means of microphones at the andardized positions from the centre line of the engine. iother microphone mounted on a circular traverse records polar plot. It is hoped that these tests will result in the loption of a standardized test procedure for comparing iise levels of various types of engines, and also to determine e variation in noise level of a number of samples of the me engine model.
It is fairly clear that although detail design changes will oduce worthwhile improvements in total noise level, the ope is limited unless major changes in current engine sign concepts are made. When contemplating the wisdom embarking upon an entirely different concept of reciproting diesel engine it seems appropriate to pause and conler whether they should in fact reciprocate at all.
iesel survival
It is my view that the probable noise legislation during a next decade will be met by the conventional directection diesel engine modified to incorporate those ise reduction features which have been found to be neficial without too great an effect on first cost, operating sts, and reliability. The vehicle manufacturer in coeration with the engine supplier will be required to wide an appropriate degree of sound insulation to satisfy legal requirements and provide the driver with a more mfortable environment in which to work.
The purpose of noise legislation is of course to protect .1 public from annoyance and it seems that not enough ention has been given to the benefits of directional effect both noise and smoke in the design of current vehicles. -ecting noise and exhaust gases in an upward direction is ?.ly to be the least objectionable. With this in mind we -I consider a tractive unit with the engine cooling system Dve or behind the cab. The fans, which would have electric
hydraulic temperature modulated drives, would be sitioned as high as possible above the ground and discharge air cooling air vertically. The fan ducting would be lined with und absorbing materials. The exhaust system, including the silencer, would be similarly but separately enclosed and so arranged that the exhaust gases would be discharged with the radiator cooling air and benefit from rapid dilution.
No front grille
We can dispense with the large radiator opening in front of the car altogether with the escape routes for the cooling air, and this enables the engine to be enclosed in a soundproofed compartment with an undershield. The exhaust manifold' could be water jacketed so that ventilation of the engine compartment would be accomplished by a small fan with the air entering and leaving through small strategically placed openings having sound-absorbing splitters.
To provide good engine accessibility for maintenance and repair, a tilt cab would be necessary, with the upper half of the engine enclosure lifting with the cab. A development of the idea illustrated on page 65 is to raise the top of the cab to the same height as the trailer load and this has the double advantage of minimizing cooling air recirculation and also reducing wind resistance, hence fuel consumption.
All these sketches are based upon a sleeper-cab arrangement and there may be cases where the additional space behind the cab for the cooling system cannot be made available. This could be overcome by using the enclosed space above the driver as the sleeping compartment. Upstairs to bed !
This brings us to a study of the probable power needs for future truck engines. The situation within the UK will be considered first.
At the present time 32 tons is the maximum normal gvw permitted, with no minimum power/weight ratio and a vague subjective control on exhaust smoke. There is a British Standard defining acceptable smoke standards (AU141-1967) but it is entirely voluntary whether an engine manufacturer wishes to comply. Its requirements are stringent and would result in many engines being derated below their advertised power. This British Standard has now been revised (BSAU141A), one of the most significant changes being that smoke is measured by an opacimeter instead of the filtration method previously adopted. The filtration method (Bosch meter) can only be used under steady state conditions and as only particulate Taking this theme further, the weight of the cooling system is taken on a separate structure instead of the cab. The radiator can either be mounted in the side panel or on top, across the outlet of the enclosure.
carbon is measured this may not be a true measure of till total visible smoke. An opacimeter (Hartridge type) react to any constituent in the exhaust gas which obscures ligh and is also responsive to transient changes in smoke leve The latter will be necessary if measuring smoke from turbocharged engine during acceleration becomes requirement.
Current noise regulations when measured outside th vehicle by a British Standard method are 89 DbA maximur for vehicles with engines below 200 hp and 92 DbA fc vehicles with engines over 200 hp.
By April 1 1972 new-registered vehicles (manufacture after October 1 1971) will be required to have a minimu of 6 "installed horsepower" per ton gross vehicle weigh1 This raises the questions: Whose horsepower? And whi does "installed" mean? The basis for measuring horsepowr will be the new British Standard AU141A and will t related to a smoke limit and subject to a dynamometE test to determine the deterioration in performance over 100-hour cyclic test. An engine manufacturer will t required to have his engines certificated in this way. As tt power losses will vary from one installation to anoth lepending upon the number and type of power-consuming iccessories, it has been agreed that the "installed power' an be calculated from the BS AU141A certified power. he differences will be of the order of 10 to 20 hp for a iross rating of 200 hp.
The 32-ton/6hp formula will require 192 installed horseower minimum or 202 to 212 AU141A gross horsepower. ccording to accessory losses, To meet the legal noise 3vels it is necessary for the truck manufacturer to resort ) sound-absorbing shields in strategic areas of the istallation, more expensive exhaust systems, and other aatures. This costs money and it may be that the manufacJrer will elect to install an engine of slightly more power -Ian the legal minimum to take advantage of the 3 DbA igher limit on noise pressure level. Although 3 DhA may ot appear to be a great deal of changetit must be appreciated -tat the measurements are on a logarithmic scale and a hange of 10 DbA means a doubling or halving of noise ressure level.
So the first effect of the new legislation will be to increase ngine horsepower to 202/212 gross or 209/229 gross relaxation of noise limit is required. and to relate this power ) what is essentially a clean exhaust condition.
This assumes that the truck operator will require his ?.hicle plated to 32 tons.
It is anticipated that, providing maximum smoke and Dise levels can be maintained or reduced, the Government ill see its way clear to increase the gross vehicle weight 38 or 44 tons. An increase in the power/weight ratio lay also be considered desirable. The following table shows le AU141A gross horsepower requirements, the 10 )rsepower range for each step being for additional power)nsuming accessories above the minimum of a fan, anerator and air compressor. current legislation Great Britain does not produce heavyduty trucks with the performance or payload of European manufacturers. My belief is that no manufacturer is likely to succeed in an export market with a product which, although it might meet the market specification, does not enjoy substantial home sales of the same product. To compete successfully in Europe we must not only build but also use European-type trucks in Britain. As the vehicle's power/weight ratio improves so does the case for a road speed governor. This device will enable the driver to make use of the higher horsepower when laden to improve acceleration and gradeability, but prevents abuse of this power under other conditions.
It will not have escaped your notice that the only type of power unit which has been considered in this paper is the reciprocating diesel engine. My view is that for the next decade this type of engine will continue to dominate the heavy-duty truck market. I believe that a diesel truck can be developed which will give continuous smoke-free operation with minimum maintenance, which will be sufficiently quiet in operation to satisfy the public and which can have invisible exhaust emissions controlled at a level where they will continue to offer no hazard to health.
The case for the gas turbine is strengthened as the horsepower requirement increases and the cost per installed horsepower comes down. The turbine will show improving fuel consumption in terms of ton miles/gallon as the vehicle power weight ratio is reduced and the engine operates at a high load factor. Vehicles which can show an economic advantage with a gas turbine power unit will be in the minority end of the scale for some considerable time to come.
The two-stage rotary diesel could become an interesting contender for the market if it continues to make the progress that it has in the past year or two. The compound rotary engine seems to combine most of the advantages claimed for both the reciprocating diesel and the gas turbine engine; however, it is still in its infancy and the next two years should decide the challenge it is likely to make.
Stirling engines, steam engines, electric vehicles, and hybrid vehicles do not get to the starting post unless further research uncovers a need in Great Britain or Europe for drastic reduction of diesel truck exhaust emissions.
Finally, this paper would not be complete without some mention of the stratified-charge engine. This combustion system was originally devised many years ago to increase the expansion ratio of a petrol engine under all conditions of operation, and so return a fuel consumption approaching that of the diesel engine without the penalty of noise, roughness, and increased weight. The engine has the disadvantage of complication particularly as it combines the least reliable features of the diesel and the petrol engine. Fresh interest was shown in stratified-charge engines when multi-fuel operation became a Military requirement, but again it failed to make the grade. Latterly there has been a fresh revival of interest in view of the low emission level of oxides of nitrogen, carbon monoxide and unburnt hydrocarbons. For areas like Tokyo or Los Angeles with their uniquely severe pollution problems the stratified charge engine might yet have its day.