Ford tandem
Page 44
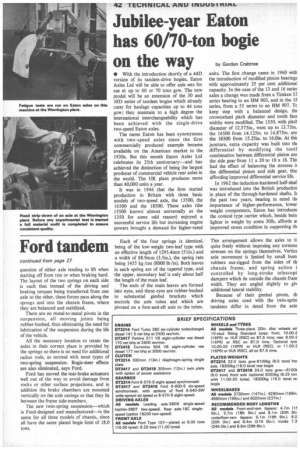
Page 45
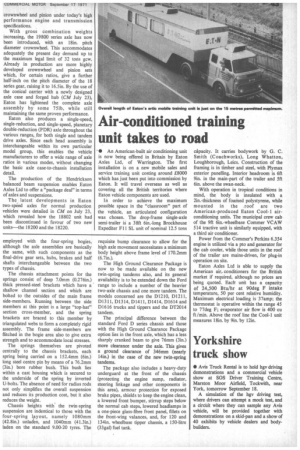
If you've noticed an error in this article please click here to report it so we can fix it.
continued from page 27
question of either axle tending to lift when starting off from rest or when braking hard. The layout of the two springs on each side is such that instead of the driving and braking torques being transferred from one axle to the other, these forces pass along the springs and into the chassis frame, where they are balanced and stabilized.
There are no metal-to-metal pivots in the suspension, all moving joints being rubber-bushed, thus eliminating the need for lubrication of the suspension during the life of the vehicle.
All the necessary location to retain the axles in their correct place is provided by the springs so there is no need for additional radius rods, as normal with most types of two-spring suspension. Bogie-steer effects are also eliminated, says Ford.
Ford has moved the rear-brake actuators well out of the way to avoid damage from rocks or other surface projections, and in addition the brake chambers are mounted vertically on the axle casings so that they lie between the frame side-members.
The new twin-spring suspension-which is Ford-designed and manufactured-is the same for all three models of chassis, since all have the same plated bogie limit of 18.0 tons. Each of the four springs is identical, being of the low-weight two leaf type with an effective length of 1295.4mm (51in.) and a width of 88.9mm (3.5in.), the spring rate being 1455 kg /cm (8000 lb/in). Both leaves in each spring are of the tapered type, and the upper, secondary leaf is only about half the length of the main leaf.
The ends of the main leaves are formed into eyes, and these eyes are rubber-bushed to substantial gimbal brackets which encircle the axle tubes and which are pivoted on a fore-and-aft axis to the tubes. This arrangement allows the axles to ti: quite freely without imposing any torsionc stresses on the springs themselves. Vertict axle movement is limited by small bum rubbers out-rigged from the sides of th chassis frame, and spring action i controlled by long-stroke telescopi dampers which lie outside the chassis fram width. They are angled slightly to giv additional lateral stability.
Because of their gimbal pivots, th driving axles used with the twin-sprin tandems differ in detail from the axle employed with the four-spring bogies, although the axle assemblies are basically the same, with such components as the final-drive gear sets, hubs, brakes and half shafts interchangeable between the two types of chassis.
The chassis attachment points for the springs consist of deep 7.0mm (0.276in.) thick pressed-steel brackets which have a shallow channel section and which are bolted to the outsides of the main frame side-members. Running between the side members at this point is a large "top-hat" section cross-member, and the spring brackets are braced to this member by triangulated webs to form a completely rigid assembly. The frame side-members are (Etched in the bogie area also to give extra strength and to accommodate local stresses.
The springs themselves are pivoted centrally to the chassis brackets, each spring being carried on a I52.4mm (6in.) long steel centre pin by means of a 76.2mm (3in.) bore rubber bush. This bush lies within a cast housing which is secured to the underside of the spring by inverted U-bolts. The absence of need for radius rods not only simplifies the overall suspension and reduces its production cost, but it also reduces the weight.
Chassis heights with the twin-spring suspension are indentical to those with the four-spring layout, namely 1080mm (42.8in.) unladen, and 1040mm (41.3in.) laden on the standard 9.00-20 tyres. The requisite bump clearance to allow for the high axle movement necessitates a minimum body height above frame level of 170.2mm (6.7in.).
The High Ground Clearance Package is now to be made available on the new twin-spring tandems also, and its general availability is to be extended down the Ford range to include a number of the heavier two-axle chassis and one more tandem. The models concerned are the D1210, D1211. D1311, D1314, D1411, D1414, D1614 and D1616 trucks and tippers and the DT2014 tandem.
The principal difference between the standard Ford D series chassis and those with the High Ground Clearance Package option lies in the front axle, which has a less sharply cranked beam to give 76mm (3in.) more clearance under the axle. This gives a ground clearance of 346mm (nearly 14in.) in the case of the new twin-spring tandems.
The package also includes a heavy-duty underguard at the front of the chassis (protecting the engine sump. radiator, steering linkage and other components in this area), armour protection for exposed brake pipes, shields to keep the engine clean, a lowered front bumper, stirrup steps below the normal cab steps, lowered headlamps in a one-piece glass-fibre front panel, fillets on the front-wing valances, and, for 120 and 134in. wheelbase tipper chassis, a 150-litre (33ga1) fuel tank.