TAKING THE• HEADACHE OUT OF LOSS-OF-USE
Page 89
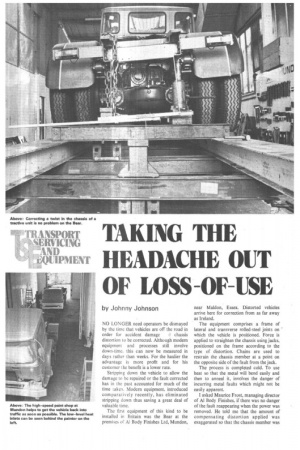
Page 90
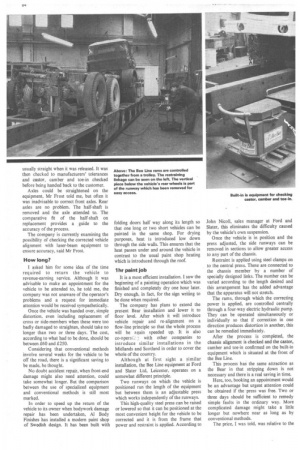
Page 91
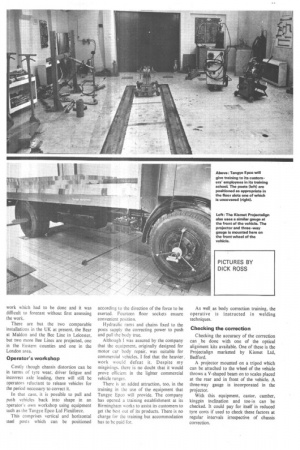
If you've noticed an error in this article please click here to report it so we can fix it.
by Johnny Johnson
NO LONGER need operators be dismayed by the time that vehicles are off the road in
order for accident damage • 1 chassis distortion to be corrected. Although modern equipment and processes still involve down-time, this can now be measured in days rather than weeks. For the haulier the advantage is more profit and for his customer the benefit is a lower rate.
Stripping down the vehicle to allow the damage to be repaired or the fault corrected has in the past accounted for much of the time taken. Modern equipment, introduced comparatively recently, has eliminated stripping down thus saving a great deal of valuable time.
The first equipment of this kind to be installed in Britain was the Bear at the premises of Al Body Finishes Ltd, Mundon, near Maldon, Essex. Distorted vehicles arrive here for correction from as far away as Ireland.
The equipment comprises a frame of lateral and transverse rolled-steel joists on which the vehicle is positioned. Force is applied to straighten the chassis using jacks, positioned on the frame according to the type of distortion-. Chains are used to restrain the chassis member at a point on the opposite side of the fault from the jack.
The process is completed cold. To use heat so that the metal will bend easily and then to anneal it, involves the danger of incurring metal faults which might not be easily apparent.
I asked Maurice Frost, managing director of Al Body Finishes, if there was no danger of the fault reappearing when the power was removed. He told me that the amount of compensating distortion applied was exaggerated so that the chassis member was usually straight when it was released. It was then checked to manufacturers' tolerances and castor, camber and toe-in checked before being handed back to the customer.
Axles could be straightened on the equipment, Mr Frost told me, but often it was inadvisable to correct front axles. Rear axles are no problem. The half-shaft is removed and the axle attended to. The comparative fit of the half-shaft on replacement provides a guide to the accuracy of the process.
The company is currently examining the possibility of checking the corrected vehicle alignment with laser-beam equipment to ensure accuracy, said Mr Frost.
How long?
I asked him for some idea of the time required to return the vehicle to revenue-earning service. Although it was advisable to make an appointment for the vehicle to be attended to, he told me, the company was not unaware of the operator's problems and a request for immediate attention would be received sympathetically.
Once the vehicle was handed over, simple distortion, even including replacement of cross or side-members when these were too badly damaged to straighten, should take no longer than two or three days. The cost, according to what had to be done, should be between £60 and £250.
Considering that conventional methods involve several weeks for the vehicle to be off the road, there is a significant saving to be made, he thought.
No doubt accident repair, when front-end damage might also need attention, could take somewhat longer. But the comparison between the use of specialized equipment and conventional methods is still most marked.
In order to speed up the return of the vehicle to its owner when bodywork damage repair has been undertaken, Al Body Finishes has installed a modern paint shop of Swedish design. It has been built with folding doors half way along its length so that one long or two short vehicles can be painted in the same shop. For drying purposes, heat is introduced low down through the side walls. This ensures that the heat passes under and around the vehicle in contrast to the usual paint shop heating which is introduced through the roof.
hr paint job It is a most efficient installation. I saw the beginning of a painting operationwhich was finished and completely dry one hour later. Dry enough, in fact, for the sign writing to be done when required.
The company has plans to extend the present Bear installation and lower it to floor level. After which it will introduce vehicle repair and re-alignment on a flow-line principle so that the whole process will be again speeded up. It is also co-operatl: T. with other companies to introduce similar installations in the Midlands and Scotland in order to cover the whole of the country.
Although at first sight a similar installation, the Bee Line equipment at Ford and Slater Ltd, Leicester, operates on a somewhat different principle.
Two runways on which the vehicle is positioned run the length of the equipment but between them is an adjustable press which works independently of the runways.
This high-quality steel press can be raised or lowered so that it can be positioned at the most convenient height for the vehicle to be corrected and it is from the frame that power and restraint is applied. According to John Nicoll, sales manager at Ford and Slater, this eliminates the difficulty caused by the vehicle's own suspension.
Once the vehicle is in position and the press adjusted, the side runways can be removed in sections to. allow greater access to any part of the chassis.
Restraint is applied using steel clamps on to the central press. These are connected to the chassis member by a number of specially designed links. The number can be varied according to the length desired and this arrangement has the added advantage that the apparatus will not stretch.
The rams, through which the correcting power is applied, are controlled centrally through a four-way electric hydraulic pump. They can be operated simultaneously or individually so that if correction in one direction produces distortion in another, this can be remedied immediately.
After the process is completed, the chassis alignment is checked and the castor, camber and toe-in confirmed on the built-in equipment which is situated at the front of the Bee Line.
This process has the same attraction as the Bear in that stripping down is not necessary and there is a real saving in time.
Here, too, booking an appointment would be an advantage but urgent attention could be obtained if the press was free. Two or three days should be sufficient to remedy simple faults in the ordinary way. More complicated damage might take a little longer but nowhere near as long as by conventional methods.
The price, I was told, was relative to the work which had to be done and it was difficult to forecast without first assessing the work.
There are but the two comparable installations in the UK at present, the Bear at Maldon and the Bee Line in Leicester, but two more Bee Lines are projected, one in the Eastern counties and one in the London area.
Operator's workshop Costly though chassis distortion can be in terms of tyre wear, driver fatigue and incorrect axle loading, there will still be operators reluctant to release vehicles for the period necessary to correct it.
In that case, it is possible to pull and push vehicles back into shape in an aperator's own workshop using equipment such as the Tangye Epco Ltd Flexiforce.
This comprises vertical and horizontal steel posts which can be positioned according to the direction of the force to be exerted. Fourteen floor sockets ensure convenient position.
Hydraulic rams and chains fixed to the posts supply the correcting power to push and pull the body true.
Although I was assured by the company that the equipment, originally designed for motor car body repair, was suitable for commercial vehicles. I feel that the heavier work would defeat it. Despite my misgivings, there is no doubt that it would prove efficient in the lighter commercial vehicle ranges.
There is an added attraction, too, in the training in the use of the equipment that Tangye Epco will provide. The company has opened a training establishment at its Birmingham works to assist its customers to get the best out of its products. There is no charge for the training but accommodation has to be paid for. As well as body correction training, the operative is instructed in welding techniques.
Checking the correction Checking the accuracy of the correction can , be done with one of the optical alignment kits available. One of these is the Projectalign marketed by Kismet Ltd, Bedford.
A projector mounted on a tripod which can be attached to the wheel of the vehicle throws a V-shaped beam on to scales placed at the rear and in front of the vehicle. A three-way gauge is incorporated in the projector.
With this equipment, castor, camber, kingpin inclination and toe-in can be checked. It could pay for itself in reduced tyre costs if used to check these factors at regular intervals irrespective of chassis correction.