LESS HEAVY MORE GOODS
Page 106
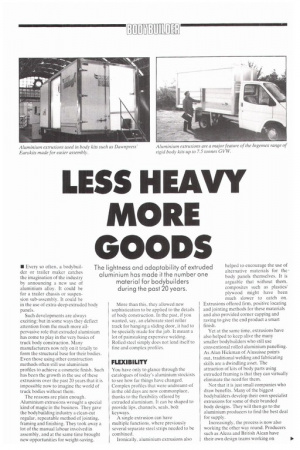
Page 108
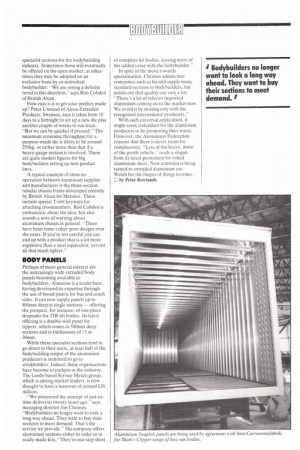
If you've noticed an error in this article please click here to report it so we can fix it.
• Every so often, a bodybuilder or trailer maker catches the imagination of the industry by announcing a new use of aluminium alloy. It could be for a trailer chassis or suspension sub-assembly. It could be in the use of extra-deep extruded body panels.
Such developments are always exciting; but in some ways they deflect attention from the much more allpervasive role that extruded aluminium has come to play in the very basics of truck body construction. Many manufacturers now rely on it totally to form the structural base for their bodies. Even those using other construction methods often still use aluminium profiles to achieve a cosmetic finish. Such has been the growth in the use of these extrusions over the past 20 years that it is impossible now to imagine the world of truck bodies without them.
The reasons are plain enough. Aluminium extrusions wrought a special kind of magic in the business. They gave the bodybuilding industry a clean-cut regular, repeatable method of jointing, framing and finishing. They took away a lot of the manual labour involved in assembly, and at the same time brought new opportunities for weight-saving. More than this, they allowed new sophistication to be applied to the details of body construction. In the past, if you wanted, say, an elaborate steel roller track for hanging a sliding door, it had to be specially made for the job. It meant a lot of painstaking expensive welding. Rolled steel simply does not lend itself to fine and complex profiles.
You have only to glance through the catalogues of today's aluminium stockists to see how far things have changed. Complex profiles that were undreamt-of in the old days are now commonplace, thanks to the flexibility offered by extruded aluminium. It can be shaped to provide lips, channels, seals, bolt keyways.
A single extrusion can have multiple functions, where previously several separate steel strips needed to be combined.
Ironically, aluminium extrusions also helped to encourage the use of alternative materials for the body panels themselves. It is arguable that without them, composites such as plastics/ plywood might have been much slower to catch on. Extrusions offered firm, positive locating and jointing methods for these materials and also provided corner capping and raving to give the end product a smart finish.
Yet at the same time, extrusions have also helped to keep alive the many smaller bodybuilders who still use conventional rolled aluminium panelling. As Alan Hickman of A lusuisse points out, traditional welding and fabricating skills are a dwindling asset. The attraction of kits of body parts using extruded framing is that they can virtually eliminate the need for them.
Not that it is just small companies who draw benefits. Many of the biggest bodybuilders develop their own specialist extrusions for some of their branded body designs. They will then go to the aluminium producers to find the best deal for supply.
Increasingly, the process is now also working the other way round. Producers such as Alcoa and British Alcan have their own design teams working on
specialist sections for the bodybuilding industry. Sometimes these will eventually be offered on the open market; at other times they may be adopted on an exclusive basis by an individual bodybuilder: -We are seeing a definite trend in this direction," says Ron Cobden of British Alcan.
How easy is it to get your profiles made up? Peter Unstead of Alcoa Extruded Products, Swansea, says it takes from 10 days to a fortnight to set up a new die plus another couple of weeks to run trials. "But we can be quicker if pressed." The minimum economic throughput for a purpose-made die is likely to be around 250kg, or rather more than that if a heavy-gauge section is involved. These are quite modest figures for big bodybuilders setting up new product lines.
A typical example of close cooperation between aluminium supplier and manufacturer is the three-section tubular chassis frame developed recently by British Alcan for Metalair. These include special T-slot keyways for attaching crossrnembers. Ron Cobden is enthusiastic about the idea, but also sounds a note of warning about aluminium chassis in general. "There have been some rather poor designs over the years. If you're not careful you can end up with a product that is a lot more expensive than a steel equivalent, yet not all that much lighter."
Perhaps of more general interest are the increasingly wide extruded body panels becoming available to bodybuilders. Alusuisse is a leader here. having developed its expertise through the use of broad panels for bus and coach sides. It can now supply panels up to 800mm deep in single sections offering the prospect, for instance, of one-piece dropsides for TIR tilt bodies. Its latest offering is a double-wall panel for tippers, which comes in 580mm deep sections and in thicknesses of 15 or 30rnm.
While these specialist sections tend to go direct to their users, at least half of the bodybuilding output of the aluminium producers is reckoned to go to stockholders. Indeed, these organisations have become a lynchpin in the industry. The Leeds-based Service Metals group, which is among market leaders, is now thought to have a turnover of around £16 million.
-We pioneered the concept of just-intime deliveries twenty years ago," says managing director Jim Chrimes: "Bodybuilders no longer want to look a long way ahead. They want to buy their sections to meet demand. That's the service we provide." His company offers aluminium sections either to order or in ready-made kits. "They're one step short of complete kit bodies, leaving more of the added value with the bodybuilder.
In spite of the move towards specialisation, Chrimes admits that companies such as his still supply many standard sections to bodybuilders, but points out that quality can vary a lot: "There's a lot of inferior imported aluminium coming on to the market now. We avoid it by dealing only with the recognised international producers."
With such universal application, it might seem redundant for the aluminium producers to be promoting their wares. However, the Aluminium Federation reasons that there is never room for complacency. "Less of the heavy, more of the goods vehicle," reads a slogan from its latest promotion for rolled aluminium sheet. Now attention is being turned to extruded aluminium too. Watch for the shapes of things to come. 0 by Peter Rowlands