HOT TIPS ON SMALL TIPPERS
Page 49
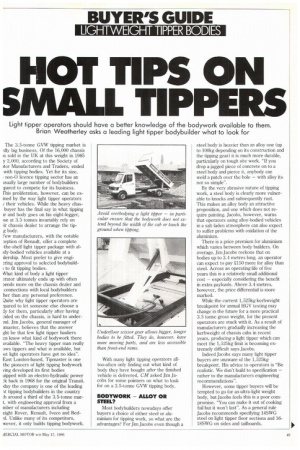
Page 50
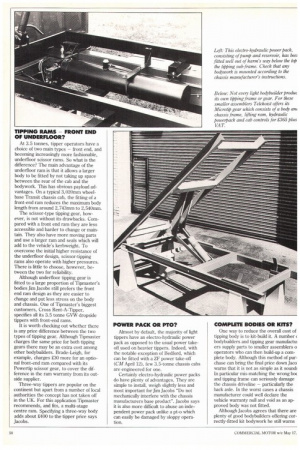
Page 51
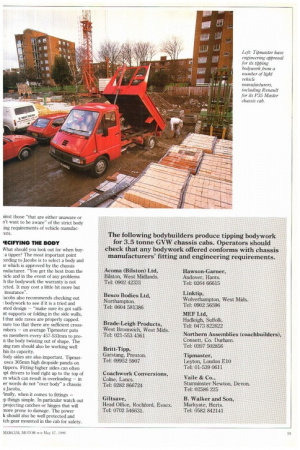
If you've noticed an error in this article please click here to report it so we can fix it.
Light tipper operators should have a better knowledge of the bodywork available to them. Brian Weatherley asks a leading light tipper bodybuilder what to look for
The 3.5-tonne GVW tipping market is .dly big business. Of the 16,000 chassis is sold in the UK at this weight in 1985 y 2,000, according to the Society of itor Manufacturers and Traders, ended with tipping bodies. Yet for its size, : non-0 licence tipping sector has an isually large number of bodybuilders Tared to compete for its business. Fhis proliferation, however, can be exined by the way light tipper operators ,r their vehicles. While the heavy chasbuyer has the final say in what tipping ir and body goes on his eight-legger, pse at 3.5 tonnes invariably rely on ir chassis dealer to arrange the tipg body.
Few manufacturers, with the notable :eption of Renault, offer a complete -the-shelf light tipper package with alidy-bodied vehicles available at a dership. Most prefer to give engiHing approval to selected bodybuild; to fit tipping bodies, What kind of body a light tipper .rator ultimately ends up with often aends more on the chassis dealer and connections with local bodybuilders her than any personal preference. Quite why light tipper operators are pared to let someone else choose a dy for them, particularly after having zided on the chassis, is hard to under'id. Jim Jacobs, general manager of =aster, believes that the answer ght be that few light tipper hauliers en know what kind of bodywork there available. "The heavy tipper man really ows tippers and what is available, but )st light operators have got no idea". East London-based, Tipmaster is one the pioneers of light tipping bodywork ving developed its first bodies uipped with an electro-hydraulic power :k back in 1968 for the original Transit. day the company is one of the leading it tipping bodybuilders in the country :h around a third of the 3.5-tonne mart, with engineering approval from a mber of manufacturers including eight Rover, Renault, Iveco and Bed d. many of its competitors, wever, it only builds tipping bodywork. With many light tipping operators alltoo-often only finding out what kind of body they have bought after the finished vehicle is delivered, CM asked Jim Jacobs for some pointers on what to look for on a 3.5-tonne GVW tipping body.
BODYWORK — ALLOY OR STEEL?
Most bodybuilders nowadays offer buyers a choice of either steel or aluminium for tipping work, so what are the advantages? For Jim Jacobs even though a steel body is heavier than an alloy one (up to 100kg depending on its construction and the tipping gear) it is much more durable, particularly on tough site work. "If you drop a jagged piece of concrete on to a steel body and pierce it, anybody can weld a patch over the hole — with alloy its not so simple".
By the very abrasive nature of tipping work, a steel body is clearly more vulnerable to knocks and subsequently rust. This makes an alloy body an attractive proposition, and one which does not require painting. Jacobs, however, warns that operators using alloy-bodied vehicles in a salt-laden atmosphere can also expect to suffer problems with oxidation of the aluminium.
There is a price premium for aluminium which varies between body builders. On average, Jim Jacobs reckons that on bodies up to 3.4 metres long, an operator can expect to pay .050 more for alloy than steel. Across an operating life of five years this is a relatively small additional cost — especially considering the benefit in extra payloads. Above 3.4 metres, however, the price differential is more marked.
While the current 1,525kg kerbweight breakpoint for annual HGV testing may change in the future for a more practical 3.5 tonne gross weight, for the present operators are stuck with it. As a result of manufacturers gradually increasing the kerbweight of chassis cabs in recent years, producing a light tipper which can meet the 1,525kg limit is becoming extremely difficult says Jacobs.
Indeed Jacobs says many light tipper buyers are unaware of the 1,525kg breakpoint. His advice to operators is "Be realistic. We don't build to specification — rather to the manufacturers engineering recommendations".
However, some tipper buyers will be tempted to go for an ultra-light weight body, but Jacobs feels this is a poor compromise. "You can make it out of cooking foil but it won't last". As a general rule Jacobs recommends specifying 14SWG steel on light tipper floor sections and 1618SWG on sides and tailboards. TIPPING RAMS — FRONT END OF UNDERFLOOR?
At 3.5 tonnes, tipper operators have a choice of two main types — front end, and becoming increasingly more fashionable, underfloor scissor rams. So what is the difference? The main advantage of the underfloor ram is that it allows a larger body to be fitted by not taking up space between the rear of the cab and the bodywork. This has obvious payload advantages. On a typical 3,020mm wheelbase Transit chassis cab, the fitting of a front-end ram reduces the maximum body length from around 2,743mm to 2,540mm.
The scissor-type tipping gear, however, is not without its drawbacks. Compared with a front end ram they are less accessible and harder to change or maintain. They also have more moving parts and use a larger ram and seals which will add to the vehicle's kerbweight. To overcome the initial higher resistance of the underfloor design, scissor-tipping rams also operate with higher pressures. There is little to choose, however, between the two for reliability.
Although underfloor tipping gear is fitted to a large proportion of Tipmaster's bodies Jim Jacobs still prefers the front end ram design as they are easier to change and put less stress on the body and chassis. One of Tipmaster's biggest customers, Cross Rent-A-Tipper, specifies all its 3.5 tonne GVW dropside tippers with front-end rams.
It is worth checking out whether there is any price difference between the two types of tipping gear. Although Tipmaster charges the same price for both tipping gears there may be an extra cost among other bodybuilders. Brade-Leigh, for example, charges .U0 more for an optional front-end ram compared with its Powertip scissor gear, to cover the difference in the ram warranty from its outside supplier.
Three-way tippers are popular on the continent but apart from a number of local authorities the concept has not taken off in the UK. For this application Tipmaster recommends, and fits, a multi-stage centre ram. Specifying a three-way body adds about 2400 to the tipper price says Jacobs. POWER PACK OR PTO?
Almost by default, the majority of light tippers have an electro-hydraulic power pack as opposed to the usual power takeoff used on heavier tippers. Indeed, with the notable exception of Bedford, which can be fitted with a Zr power take-off (CM April 12), few 3.5-tonne chassis cabs are engineered for one.
Certainly electro-hydraulic power packs do have plenty of advantages. They are simple to install, weigh slightly less and most important for Jim Jacobs "Do not mechanically interfere with the chassis manufacturers base product". Jacobs says it is also more difficult to abuse an independent power pack unlike a pt-o which can easily be damaged by sloppy operation. COMPLETE BODIES OR KITS?
One way to reduce the overall cost of tipping body is to kit-build it. A number bodybuilders and tipping gear manufactui ers supply parts to smaller assemblers o operators who can then build-up a complete body. Although this method of purchase can bring the final price down Jaco warns that it is not as simple as it sound: In particular mis-matching the wrong bat and tipping frame can seriously damage the chassis driveline — particularly the back axle. In the worst cases a chassis manufacturer could well declare the vehicle warranty null and void as an approved body was not fitted.
Although Jacobs agrees that there are plenty of good bodybuilders offering correctly-fitted kit bodywork he still warns
linst those "that are either unaware or ft want to be aware" of the strict body ing requirements of vehicle manufac-ers.
%ammo THE BODY
What should you look out for when buy, a tipper? The most important point :ording to Jacobs is to select a body and lr which is approved by the chassis nufacturer. "You get the best from the icle and in the event of any problems the bodywork the warranty is not 2..cted. It may cost a little bit more but insurance".
racobs also recommends checking out bodywork to see if it is a tried and sted design — "make sure its got suffint supports or folding in the side walls, that side raves are properly capped. sure too that there are sufficient crossmbers — on average Tipmaster puts rss members every 457-533mm to preit the body twisting out of shape. The )ing ram should also be working well bin its capacity.
3ody sides are also important. Tipmasuses 305mm high dropside panels on tippers. Fitting higher sides can often -ipt drivers to load right up to the top of m which can result in overloading — in er words do not "over body" a chassis s Jacobs.
inally, when it comes to fittings things simple. In particular watch out projecting catches or hinges that will more prone to damage. The power k should also be well protected and tch gear mounted in the cab for safety.