Name change puts Victory clearly in sight
Page 75
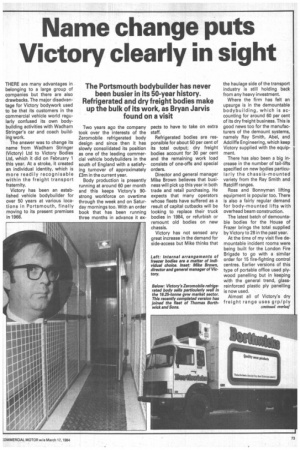
Page 76
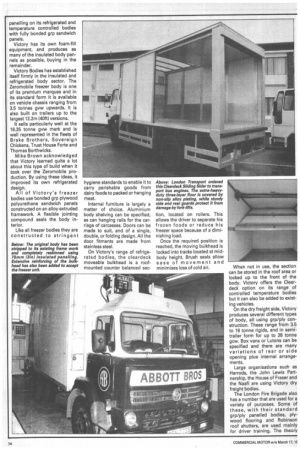
Page 77
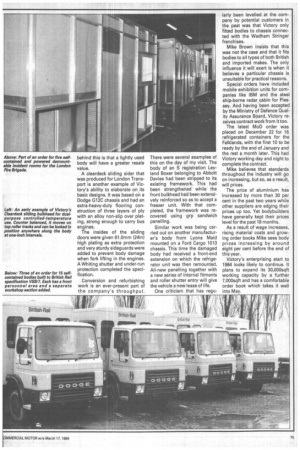
If you've noticed an error in this article please click here to report it so we can fix it.
The Portsmouth bodybuilder has never been busier in its 50-year history. Refrigerated and dry freight bodies make up the bulk of its work, as Bryan Jarvis found on a visit
THERE are many advantages in belonging to a large group of companies but there are also drawbacks. The major disadvantage for Victory bodywork used to be that its customers in the commercial vehicle world regularly confused its own bodybuilding activities with Wadham Stringer's car and coach building work.
The answer was to change its name from Wadham Stringer (Victory) Ltd to Victory Bodies Ltd, which it did on February 1 this year. At a stroke, it created an individual identity, which is more readily recognisable within the freight transport fraternity.
Victory has been an established vehicle bodybuilder for over 50 years at various locations in Portsmouth, finally moving to its present premises in 1966. Two years ago the company took over the interests of the Zeromobile refrigerated body design and since then it has slowly consolidated its position as one of the leading commercial vehicle bodybuilders in the south of England with a satisfying turnover of approximately Om in the current year.
Body production is presently running at around 60 per month and this keeps Victory's 90strong workforce on overtime through the week and on Saturday mornings too. With an order book that has been running three months in advance it ex
pects to have to take on extra staff.
Refrigerated bodies are responsible for about 50 per cent of its total output; dry freight bodies account for 30 per cent and the remaining work load consists of one-offs and special orders.
Director and general manager Mike Brown believes that business will pick up this year in both trade and retail purchasing. He expects that many operators whose fleets have suffered as a result of capital cutbacks will be looking to replace their truck bodies in 1984, or refurbish or remount old bodies on new chassis.
Victory has not sensed any great increase in the demand for side-access but Mike thinks that the haulage side of the transport industry is still holding back from any heavy investment.
Where the firm has felt an upsurge is in the demountable bodybuilding, which is accounting for around 60 per cent of its dry freight business. This is good news too for the manufacturers of the demount systems, namely Ray Smith, Abel, and Adcliffe Engineering, which keep Victory supplied with the equipment.
There has also been a big increase in the number of tail-lifts specified on new bodies particularly the chassis-mounted variety from the Ray Smith and Ratcliff ranges.
Ross and Bonnyman lifting equipment is popular too. There is also a fairly regular demand for body-mounted lifts with overhead beam construction.
The latest batch of demountable bodies for the House of Frazer brings the total supplied by Victory to 28 in the past year.
At the time of my visit five demountable incident rooms were being built for the London Fire Brigade to go with a similar order for 15 fire-fighting control centres. Earlier versions of this type of portable office used plywood panelling but in keeping with the general trend, glassreinforced plastic ply panelling is now used.
Almost all of Victory's dry freight range uses grp/ply panelling on its refrigerated and temperature controlled bodies with fully bonded grp sandwich panels.
Victory has its own foam-fill equipment, and produces as many of the insulated body pannels as possible, buying in the remainder.
Victory Bodies has established itself firmly in the insulated and refrigerated body sector. The Zeromobile freezer body is one of its premium marques and in its standard form it is available on vehicle chassis ranging from 3.5 tonnes gvw upwards. It is also built on trailers up to the largest 12.2m (413ft) versions.
It sells particularly well at the 16.25 tonne gvw mark and is well represented in the fleets of Brake Brothers, Sovereign Chickens, Trust House Forte and Thomas Borthwicks.
Mike Brown acknowledged that Victory learned quite a lot about this type of build when it took over the Zeromobile production. By using these ideas, it improved its own refrigerated design.
All of Victory's freezer bodies use bonded grp plywood polyurethane sandwich panels constructed on an alloy extruded framework. A flexible jointing compound seals the body interior.
Like all freezer bodies they are constructed to stringent hygiene standards to enable it to carry perishable goods from dairy foods to packed or hanging meat.
Internal furniture is largely a matter of choice. Aluminium body shelving can be specified, as can hanging rails for the carriage of carcasses. Doors can be made to suit, and of a single, double, or folding design. All the door fitments are made from stainless steel.
On Victory's range of refrigerated bodies, the cleardeck moveable bulkhead is a roofmounted counter balanced sec
Above: London Transport ordered this Cleardeck Sliding Sider to transport bus engines. The extra-heavyduty three-layer floor is covered by non-slip alloy plating, while sturdy side and rear guards protect it from damage by fork-lifts.
tion, located on rollers. This allows the driver to separate his frozen foods or reduce his freezer space because of a diminishing load.
Once the required position is reached, the moving bulkhead is locked into tracks located at midbody height. Brush seals allow ease of movement and minimises loss of cold air. When not in use, the section can be stored in the roof area or locked up to the front of the body. Victory offers the Cleardeck option on its range of controlled temperature bodies but it can also be added to existing vehicles.
On the dry freight side, Victory produces several different types of body, all using grp/ply construction. These range from 3.5 to 16 tonne rigids, and in semitrailer form for up to 38 tonne gcw. Box vans or Lutons can be specified and there are many variations of rear or side opening plus internal arrangements.
Large organisations such as Harrods, the John Lewis Partnership, the House of Fraser and the Naafi are using Victory dry freight bodies.
The London Fire Brigade also has a number that are used for a variety of purposes. Some of these, with their standard grp/ply panelled bodies, plywood flooring and Robinson roof shutters, are used mainly for driver training. The theory behind this is that a lightly used body will have a greater resale value.
A cleardeck sliding sider that was produced for London Transport is another example of Victory's ability to elaborate on its basic designs. It was based on a Dodge G12C chassis and had an extra-heavy-duty flooring construction of three layers of ply with an alloy non-slip over plating, strong enough to carry bus engines.
The insides of the sliding doors were given 61.0mm (24in) high plating as extra protection and very sturdy sideguards were added to prevent body damage when fork lifting in the engines. A Whiting shutter and under-run protection completed the specification.
Conversion and refurbishing work is an ever-present part of the company's throughput. There were several examples of this on the day of my visit. The body of an S registration Leyland Boxer belonging to Abbott Davies had been stripped to its existing framework. This had been strengthened while the front bulkhead had been extensively reinforced so as to accept a freezer unit. With that completed, the framework was recovered using grp sandwich panelling.
Similar work was being carried out on another manufacturer's body from Lyons Maid mounted on a Ford Cargo 1013 chassis. This time the damaged body had received a front-end extension on which the refrigerator unit was then remounted. All-new panelling together with a new series of internal fitments and roller shutter entry will give the vehicle a new lease of life.
One criticism that has regu
larly been levelled at the company by potential customers in the past was that Victory only fitted bodies to chassis connected with the Wadham Stringer franchises.
Mike Brown insists that this was not the case and that it fits bodies to all types of both British and imported makes. The only influence it will exert is when it believes a particular chassis is unsuitable for practical reasons.
Special orders have included mobile exhibition units for companies like IBM and the steel ship-borne radar, cabin for Plessey. And having been accepted by the Ministry of Defence Quality Assurance Board, Victory receives contract work from it too.
The latest MoD order was placed on December 22 for 16 refrigerated containers for the Falklands, with the first 10 to be ready by the end of January and the rest a month later. This had Victory working day and night to complete the contract.
Mike believes that standards throughout the industry will go on increasing, but so, as a result, will prices.
The price of aluminium has increased by more than 30 per cent in the past two years while other suppliers are edging their prices up too. Yet bodybuilders have generally kept their prices level for the past 18 months.
As a result of wage increases, rising material costs and growing order books Mike sees body prices increasing by around eight per cent before the end of this year.
Victory's enterprising start to 1984 looks likely to continue. It plans to expand its 30,000sqft working capacity by a further 7,000sqft and has a comfortable order book which takes it well into May.