FIT MAINTENANCE TO OPERATION
Page 150
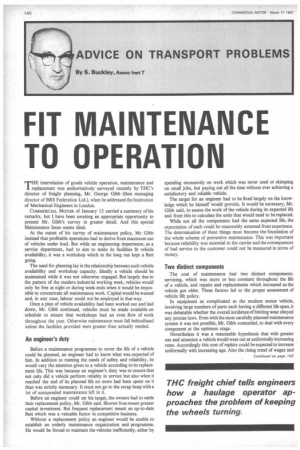
Page 153
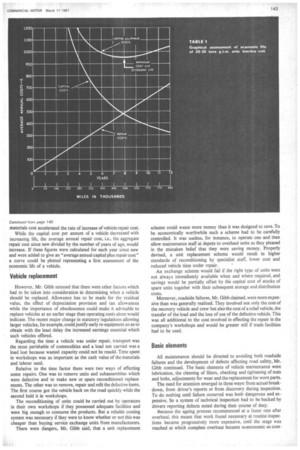
Page 154
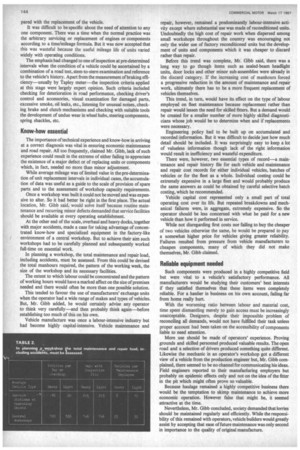
If you've noticed an error in this article please click here to report it so we can fix it.
THE interrelation of goods vehicle operation, maintenance and replacement was authoritatively surveyed recently by THC 's director of freight planning, Mr. George Gibb (then managing director of BRS Federation Ltd.), when he addressed the Institution of Mechanical Engineers in London.
COMMERCIAL MOTOR of January 13 carried a summary of his remarks, but I have been awaiting an appropriate opportunity to present Mr. Gibb's survey in greater detail. And this special Maintenance Issue seems ideal.
At the outset of his survey of maintenance policy, Mr. Gibb insisted that profitable operations had to derive from maximum use of vehicles under load. But while an engineering department, as a service department, had to aim to make its facilities fit vehicle availability, it was a workshop which in the long run kept a fleet going.
The need for planning lay in the relationship between such vehicle availability and workshop capacity. Ideally a vehicle should be maintained while it was not otherwise engaged. But largely due to the pattern of the modern industrial working week, vehicles would only be free at night or during week-ends when it would be impossible to concentrate all maintenance work. Capital would be wasted and, in any case, labour could not be employed in that way.
Once a plan of vehicle availability had been worked out and laid down, Mr. Gibb continued, vehicles must be made available on schedule to ensure that workshops had an even flow of work throughout the year. Otherwise maintenance must fall behindhand unless the facilities provided were greater than actually needed.
An engineer's duty
Before a maintenance programme to cover the life of a vehicle could be planned, an engineer had to know what was expected of him. In addition to meeting the needs of safety and reliability, he would vary the attention given to a vehicle according to its replacement life. This was because an engineer's duty was to ensure that not only did a vehicle perform reliably in service but also when it reached the end of its planned life no more had been spent on it than was strictly necessary. It must not go to the scrap heap with a lot of unexpended maintenance left in it.
Before an engineer could set his target, the owners had to settle their replacement policy, Mr. Gibb said. Shorter lives meant greater capital investment. But frequent replacement meant an up-to-date fleet which was a valuable factor in competitive business.
Without a replacement policy an engineer would be unable to establish an orderly maintenance organization and programme. He would be forced to maintain the vehicles inefficiently, either by spending excessively on work which was never used or skimping on small jobs, but paying out all the time without ever achieving a satisfactory and reliable vehicle.
The target for an engineer had to be fixed largely on the knowledge which he himself would provide. It would be necessary, Mr. Gibb said, to assess the work of the vehicle during its expected life and from this to calculate the units that would need to be replaced.
While not all the components had the same expected life, the expectation of each could be reasonably assumed from experience. The determination of these things must become the foundation of the whole scheme of preventive maintenance. This was important because reliability was essential to the carrier and the consequences of bad service to the customer could not be measured in terms of money.
Two distinct components The cost of maintenance had two distinct components: servicing, which was more or less constant throughout the life of a vehicle, and repairs and replacements which increased as the vehicle got older. These factors led to the proper assessment of vehicle life policy.
In equipment as complicated as the modem motor vehicle, involving large numbers of parts each having a different life span, it was debatable whether the overall incidence of limiting wear obeyed any precise laws. Even with the most carefully planned maintenance system it was not possible, Mr. Gibb contended, to deal with every component at the optimum stage.
Nevertheless it was a reasonable hypothesis that with greater use and attention a vehicle would wear out at uniformally increasing rates. Accordingly this cost of repairs could be expected to increase uniformally with increasing age. Also the rising trend of wages and materials cost accelerated the rate of increase of vehicle repair cost.
While the capital cost per annum of a vehicle decreased with increasing life, the average annual repair cost, i.e., the aggregate repair cost since new divided by the number of years of age, would increase. If these figures were calculated for each year since new and were added to give an "average annual capital plus repair cost" a curve could be plotted representing a first assessment of the economic life of a vehicle.
Vehicle replacement However, Mr. Gibb stressed that there were other factors which had to be taken into consideration -in determining when a vehicle should be replaced. Allowance has to be made for the residual value, the effect of• depreciation provision and tax allowances while the importance of obsolescence could make it advisable to replace vehicles at an earlier stage than operating costs alone would indicate. The recent major change in statutory regulations allowing larger vehicles, for example, could justify early re-equipment so as to obtain with the least delay the increased earnings essential which such vehicles offered.
Regarding the time a vehicle was under repair, transport was the most perishable of commodities and a load not carried was a load lost because wasted capacity could not be resold. Time spent in workshops was as important as the cash value of the materials and labour used.
Relative to the time factor there were two ways of effecting some repairs. One was to remove units and subassemblies which were defective and to make new or spare reconditioned replacements. The other was to remove, repair and refit the defective items. The first course got the vehicle back on the road quickly while the second held it in workshops.
The reconditioning of units could be carried out by operators in their own workshops if they possessed adequate facilities and were big enough to consume the products. But a reliable costing system was necessary if they were to know whether or not this was cheaper than buying service exchange units from manufacturers.
There were dangers, Mr. Gibb said, that a unit replacement scheme could waste more money than it was designed to save. To be economically worthwhile such a scheme had to be carefully controlled. It was useless, for instance, to operate one and then allow maintenance staff at depots to overhaul units as they pleased in the mistaken belief that they were saving money. Properly devised, a unit replacement scheme would result in higher standards of reconditioning by specialist staff, lower cost and reduced vehicle time under repair.
An exchange scheme would fail if the right type of units were not always immediately available when and where required, and savings would be partially offset by the capital cost of stocks of spare units together with their subsequent storage and distribution costs.
Moreover, roadside failures, Mr. Gibb claimed, were more expensive than was generally realized. They involved not only the cost of the recovery vehicle and crew but also the cost of a relief vehicle, the transfer of the load and the loss of use of the defective vehicle. This was all additional to the cost involved in effecting the repair in the company's workshops and would be greater still if trade facilities had to be used.
Basic elements All maintenance should be directed to avoiding both roadside failures and the development of defects affecting road safety, Mr. Gibb continued. The basic elements of vehicle maintenance were lubrication, the cleaning of filters, checking and tightening of nuts and bolts, adjustments for wear and the replacement for worn parts.
The need for attention emerged in three ways: from actual breakdown, from driver's reports or from discovery during inspection. To do nothing until failure occurred was both dangerous and expensive. So a system of technical inspection had to be backed by drivers reporting defects noted during their course of duty.
Because the ageing process recommenced at a faster rate after overhaul, this meant that work found necessary at routine inspections became progressively more expensive, until the stage was reached at which complete overhaul became uneconomic as corn pared with the replacement of the vehicle.
It was difficult to be specific about the need of attention to any one component. There was a time when the normal practice was the arbitrary servicing or replacement of engines or components according to a time/mileage formula. But it was now accepted that this was wasteful because the useful mileage life of units varied widely with operating conditions.
The emphasis had changed to one of inspection at pre-determined intervals when the condition of a vehicle could be ascertained by a combination of a road test, stem-to-stern examination and reference to the vehicle's history. Apart from the measurement of braking efficiency—usually by Tapley meter—the inspection criteria applied at this stage were largely expert opinion. Such criteria included checking for deterioration in road performance, checking driver's control and accessories, visual examination for damaged parts, excessive smoke, oil leaks, etc., listening for unusual noises, checking brake and clutch mechanisms and checking with suitable tools the development of undue wear in wheel hubs, steering components, spring shackles, etc.
Know-how essential The importance of technical experience and know-how in arriving at a correct diagnosis was vital in ensuring economic maintenance and road repair. All too frequently, claimed Mr. Gibb, lack of such experience could result in the extreme of either failing to appreciate the existence of a major defect or of replacing units or components which, in fact, needed no more than minor adjustment.
While average mileage was of limited value in the pre-determination of unit replacement intervals in individual cases, the accumulation of data was useful as a guide to the scale of provision of spare parts and to the assessment of workshop capacity requirements.
Once a workshop was built it could not be moved and was expensive to alter. So it had better be right in the first place. The actual location, Mr. Gibb said, would solve itself because routine maintenance and recurring minor defects demanded that service facilities should be available at every operating establishment.
At the other end of the scale, overhaul and heavy docks, together with major accidents, made a case for taking advantage of concentrated know-how and specialized equipment in the factory-like environment of a central workshop. But to achieve their aim such workshops had to be carefully planned and subsequently worked full-time on essential work.
In planning a workshop, the total maintenance and repair load, including accidents, must be assessed. From this could be devised the total manhours required, the pattern of the working week, the size of the workshop and its necessary facilities.
The extent to which labour could be concentrated and the pattern of working hours would have a marked affect on the size of premises needed and there would often be more than one possible solution.
This tended to favour the use of manufacturers' exchange units when the operator had a wide range of makes and types of vehicles. But, Mr. Gibb added, he would certainly advise any operator to think very carefully—and then probably think again—before establishing too much of this on his own.
Vehicle manufacture was once a labour-intensive industry but had become highly capital-intensive. Vehicle maintenance and repair, however, remained a predominantly labour-intensive activity except where substantial use was made of reconditioned units. Undoubtedly the high cost of repair work when dispersed among small workshops throughout the country was encouraging not only the wider use of factory reconditioned units but the development of units and components which it was cheaper to discard rather than repair.
Before this trend was complete, Mr. Gibb said, there was a long way to go though items such as sealed-beam headlight units, door locks and other minor sub-assemblies were already in the discard category. If the increasing cost of manhours forced a progressive reduction in the amount of maintenance and repair work, ultimately there has to be a more frequent replacement of vehicles themselves.
This trend, in turn, would have its effect on the type of labour employed on fleet maintenance because replacement rather than repair would lessen the need for skilled fitters. But a demand would be created for a smaller number of more highly skilled diagnosticians whose job would be to determine when and if replacements were necessary.
Engineering policy had to be built up on accumulated and recorded information. But it was difficult to decide just how much detail should be included. It was surprisingly easy to keep a lot of valueless information though lack of the right information would result in inefficiency and wasteful expenditure.
There were, however, two essential types of record—a maintenance and repair history file for each vehicle and maintenance and repair cost records for either individual vehicles, batches of vehicles or for the fleet as a whole. Individual costing could be extremely expensive in a large fleet and would probably produce the same answers as could be obtained by careful selective batch costing, which he recommended.
Vehicle capital cost represented only a small part of total operating cost over its life. But repeated breakdowns and mechanical failures were, in aggregate, extremely expensive. So the operator should be less concerned with what he paid for a new vehicle than how it performed in service.
While not disregarding first costs nor failing to buy the cheaper of two vehicles otherwise the same, he would be prepared to pay a somewhat higher price for vehicles giving greater reliability. Failures resulted from pressure from vehicle manufacturers to cheapen components, many of which they did not make themselves, Mr. Gibb claimed.
Reliable equipment needed Such components were produced in a highly competitive field but were vital to a vehicle's satisfactory performance. All manufacturers would be studying their customers' best interests if they satisfied themselves that these items were completely reliable. For a haulier in business on his own account, failing far from home really hurt.
With the worsening ratio between labour and material cost, time spent dismantling merely to gain access must be increasingly unacceptable. Designers, despite their impossible problem of reconciling all demands, would not have fulfilled their task unless proper account had been taken on the accessibility of components liable to need attention.
More use should be made of operators' experience. Proving grounds and skilled personnel produced valuable results. The open road and a selection of drivers produced something quite different. Likewise the mechanic in an operator's workshop got a different view of a vehicle from the production engineer but, Mr. Gibb complained, there seemed to be no channel for communicating his ideas. Field engineers reported to their manufacturing employers but probably on epidemic effects only and not on the idea of the fitter in the pit which might often prove so valuable.
Because haulage remained a highly competitive business there would be the temptation to skimp maintenance to achieve more economic operation. However false that might be, it seemed attractive at the time.
Nevertheless, Mr. Gibb concluded, society demanded that lorries should be maintained regularly and efficiently. While the responsibility of this remained with operators, vehicle builders would greatly assist by accepting that ease of future maintenance was only second in importance to the quality of original manufacture.