'ROVES ITS WORTH
Page 123
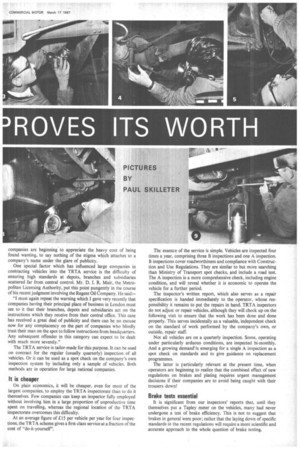
Page 122
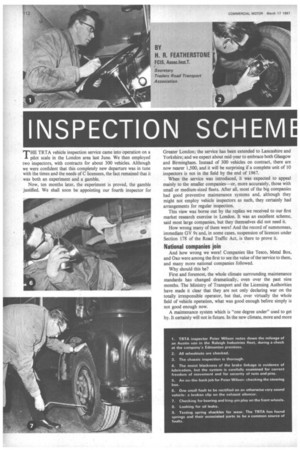
Page 124
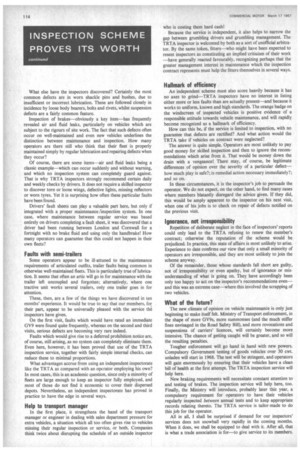
If you've noticed an error in this article please click here to report it so we can fix it.
THE TRTA vehicle inspection service came into operation on a pilot scale in the London area last June. We then employed two inspectors, with contracts for about 300 vehicles. Although we were confident that this completely new departure was in tune with the times and the needs of C licensees, the fact remained that it was both an experiment and a gamble.
Now, ten months later, the experiment is proved, the gamble justified. We shall soon be appointing our fourth inspector for Greater London; the service has been extended to Lancashire and Yorkshire; and we expect about mid-year to embrace both Glasgow and Birmingham. Instead of 300 vehicles on contract, there are now nearer 1,500, and it will be surprising if a complete unit of 10 inspectors is not in the field by the end of 1967.
When the service was introduced, it was expected to appeal mainly to the smaller companies—or, more accurately, those with small or medium-sized fleets. After all, most of the big companies had good preventive maintenance systems and, although they might not employ vehicle inspectors as such, they certainly had arrangements for regular inspection.
This view was borne out by the replies we received to our first market research exercise in London. It was an excellent scheme, said most large companies, but they themselves did not need it.
How wrong many of them were! And the record of summonses, immediate GV 9s and, in some cases, suspension of licences under Section 178 of the Road Traffic Act, is there to prove it.
National companies join
And how wrong we were! Companies like Tesco, Metal Box, and Oxo were among the first to see the value of the service to them, and many more national companies followed.
Why should this be?
First and foremost, the whole climate surrounding maintenance standards has changed dramatically, even over the past nine months. The Ministry of Transport and the Licensing Authorities have made it clear that they are not only declaring war on the totally irresponsible operator, but that, over virtually the whole field of vehicle operation, what was good enough before simply is not good enough now.
A maintenance system which is "one degree under" used to get by. It certainly will not in future. In the new climate, more and more companies are beginning to appreciate the heavy cost of being found wanting, to say nothing of the stigma which attaches to a company's name under the glare of publicity.
One special factor which has influenced large companies in contracting vehicles into the TRTA service is the difficulty of ensuring high standards at depots, branches and subsidiaries scattered far from central control. Mr. D. I. R. Muir, the Metropolitan Licensing Authority, put this point pungently in the course of his recent judgment involving the Regent Oil Company. He said:— "I must again repeat the warning which I gave very recently that companies having their principal place of business in London must see to it that their branches, depots and subsidiaries act on the instructions which they receive from their central office. This case has received a great deal of publicity and there can be no excuse now for any complacency on the part of companies who blindly trust their man on the spot to follow instructions from headquarters. Any subsequent offender in this category can expect to be dealt with much more severely."
The TRTA service is tailor-made for this purpose. It can be used on contract for the regular (usually quarterly) inspection of all vehicles. Or it can be used as a spot check on the company's own inspection system by including only a sample of vehicles. Both methods are in operation for large national companies.
It is cheaper
On plain economics, it will be cheaper, even for most of the largest companies, to employ the TRTA inspectorate than to do it themselves. Few companies can keep an inspector fully employed without involving him in a large proportion of unproductive time spent on travelling, whereas the regional location of the TRTA inspectorate overcomes this difficulty.
At an average figure of £15 per vehicle per year for four inspections, the TRTA scheme gives a first-class service at a fraction of the cost of "do-it-yourself'. The essence of the service is simple. Vehicles are inspected four times a year, comprising three B inspections and one A inspection. B inspections cover roadworthiness and compliance with Construction and Use Regulations. They are similar to but more searching than Ministry of Transport spot checks, and include a road test. The A inspection is a more comprehensive check, including engine condition, and will reveal whether it is economic to operate the vehicle for a further period.
The inspector's written report, which also serves as a repair specification is handed immediately to the operator, whose responsibility it remains to put the repairs in hand. TRTA inspectors do not adjust or repair vehicles, although they will check up on the following visit to ensure that the work has been done and done properly. This serves incidentally as a valuable, independent check on the standard of work performed by the company's own, or outside, repair staff.
Not all vehicles are on a quarterly inspection. Some, operating under particularly arduous conditions, are inspected bi-monthly. And a growing demandis emerging for a single A inspection as a spot check on standards and to give guidance on replacement programmes.
The latter is particularly relevant at the present time, when operators are beginning to realize that the combined effect of new regulations on brakes and plating requires urgent management decisions if their companies are to avoid being caught with their trousers down!
Brake tests essential
It is significant from our inspectors' reports that, until they themselves put a Tapley meter on the vehicles, many had never undergone a test of brake efficiency. This is not to suggest that brakes in general were poor; rather that the laying down of specific standards in the recent regulations will require a more scientific and accurate approach to the whole question of brake testing. What else have the inspectors discovered? Certainly the most common defects are in worn shackle pins and bushes, due to insufficient or incorrect lubrication. These are followed closely in incidence by loose body bearers, bolts and rivets, whilst suspension defects are a fairly common feature.
Inspection of brakes--obviously a key item—has frequently revealed air and fluid leaks, particularly on vehicles which are subject to the rigours of site work. The fact that such defects often occur on well-maintained and even new vehicles underlines the distinction between maintenance and inspection. How many operators are there still who think that their fleet is properly maintained simply by regular lubrication and repairing defects when they occur?
Of course, there are some items—air and fluid leaks being a classic example—which can occur suddenly and without warning, and which no inspection system can completely guard against. That is why TRTA inspectors strongly recommend certain daily and weekly checks by drivers. It does not require a skilled inspector to discover torn or loose wings, defective lights, missing reflectors or worn tyres. Yet it is surprising how often these particular faults have been found.
Drivers' fault sheets can play a valuable part here, but only if integrated with a proper maintenance /inspection system. In one case, where maintenance between regular service was based entirely on drivers completing a fault sheet, it was discovered that a driver had been running between London and Cornwall for a fortnight with no brake fluid and using only the handbrake! How many operators can guarantee that this could not happen in their own fleets?
Faults with semi-trailers
Some operators appear to be ill-attuned to the maintenance requirements of articulated outfits, trailer faults being common in otherwise well-maintained fleets. This is particularly true of lubrication. It seems that often an artic will go in for maintenance with the trailer left uncoupled and forgotten; alternatively, where one tractive unit works several trailers, only one trailer goes in for attention.
These, then, are a few of the things we have discovered in ten months' experience. It would be true to say that our members, for their part, appear to be universally pleased with the service t.14 inspectors have given.
On the first visit, faults which would have rated an immediate GV9 were found quite frequently, whereas on the second and third visits, serious defects are becoming very rare indeed.
Faults which would give rise to a deferred prohibition notice are, of course, still arising, as no system can completely eliminate them. Even here, however, it has been proved that use of the TRTA inspection service, together with fairly simple internal checks, can reduce these to minimal proportions.
What advantages accrue from using an independent inspectorate like the TRTA as compared with an opk rator employing his own? In most cases, this is an academic question, since only a minority of fleets are large enough to keep an inspector fully employed, and most of those do not find it economic to cover their dispersed depots. Nevertheless, an independent inspectorate has proved in practice to have the edge in several ways.
Help to transport manager
In the first place, it strengthens the hand of the transport manager or engineer in dealing with sales department pressure for extra vehicles, a situation which all too often gives rise to vehicles missing their regular inspection or service, or both. Companies think twice about disrupting the schedule of an outside inspector who is costing them hard cash!
Because the service is independent, it also helps to narrow the gap between grumbling drivers and grumbling management. The TRTA inspector is welcomed by both as a sort of unofficial arbitrator. By the same token, fitters—who might have been expected to resent inspectors as constituting an implied criticism of their work —have generally reacted favourably, recognizing perhaps that the greater management interest in maintenance which the inspection contract represents must help the fitters themselves in several ways.
Hallmark of efficiency
An independent scheme must also score heavily because it has no axes to grind—TRTA inspectors have no interest in listing either more or less faults than are actually present—and because it works to uniform, known and high standards. The orange badge on the windscreen of inspected vehicles is positive evidence of a responsible attitude towards vehicle maintenance, and will rapidly become recognized as a hallmark of efficiency.
How can this be, if the service is limited to inspection, with no guarantee that defects are rectified? And what action would the TRTA take if vehicles on contract were neglected?
The answer is quite simple. Operators are most unlikely to pay good money for skilled inspection and then to ignore the recommendations which arise from it. That would be money down the drain with a vengeance! There may, of course, be legitimate differences of opinion over the severity of a particular defect— how much play is safe?; is remedial action necessary immediately?; and so on.
In these circumstances, it is the inspector's job to persuade the operator. We do not expect, on the other hand, to find many cases where members blatantly disregard the advice given. If they did, this would be amply apparent to the inspector on his next visit, when one of his jobs is to check on repair of defects notified on the previous visit.
Ignorance, not irresponsibility
Repetition of deliberate neglect in the face of inspectors' reports could only lead to the TRTA refusing to renew the member's contract; otherwise the reputation of the scheme would be prejudiced. In practice, this state of affairs is most unlikely to arise. Experience to date confirms our view that only a small minority of operators are irresponsible, and they are most unlikely to join the scheme anyway.
Of the remainder, those whose standards fall short are guilty, not of irresponsibility or even apathy, but of ignorance or misunderstanding of what is going on. They have accordingly been only too happy to act on the inspector's recommendations even— and this was an extreme case—where this involved the scrapping of two vehicles.
What of the future?
The new climate of opinion on vehicle maintenance is only just beginning to make itself felt. Ministry of Transport enforcement, in the shape of more GV9s, more summonses (and the much stiffer fines envisaged in the Road Safety Bill), and more revocations and suspensions of carriers' licences, will certainly become more intensive. The chance of getting caught will be greater, and so will the resulting penalties.
Tougher enforcement will go hand in hand with new powers. Compulsory Government testing of goods vehicles over 30 cwt. unladen will start in 1968. The test will be stringent, and operators will gain enormously by ensuring that their vehicles have a clean bill of health at the first attempt. The TRTA inspection service will help here.
New braking requirements will necessitate constant attention to and testing of brakes. The inspection service will help here, too. Finally, the Ministry will introduce, probably later this year, a compulsory requirement for operators to have their vehicles regularly inspected between annual tests and to keep appropriate records relating thereto. The TRTA service is tailor-made to do this job for the operator.
All in all, I shall be surprised if demand for our inspectors' services does not snowball very rapidly in the coming months. When it does, we shall be equipped to deal with it. After all, that is what a trade association is for—to give service to its members.