The Industry's Largest Baling Press
Page 40
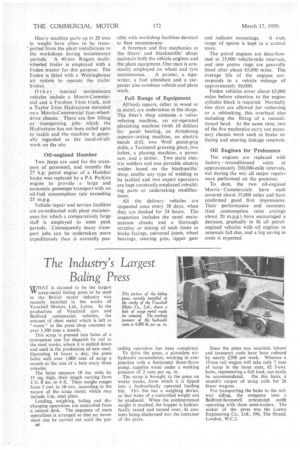
If you've noticed an error in this article please click here to report it so we can fix it.
WHAT is claimed to be the largest " scrap-metal baling press to be used in the British motor industry was recently installed in the works of Vauxhall Motors, Ltd., Luton. In the production of Vauxhall cars and Bedford commercial vehicles, the amount of sheet metal which is left as "
waste" in the press shop amounts to over 1,300 tons a month.
This scrap is pressed into bales of a convenient size for dispatch by rail to the steel works, where it is melted down and used in the production of new steel. Operating 16 hours a day, the press bales well over 1,000 tons of scrap a month at the rate Of a bale every three minutes.
The bales measure 18 ins, wide by 15 ins. high, their length varying from 2 ft. 8 ins. to 4 ft. Their weight ranges from 5 cwt. to 10 cwt., "according to the nature of the scrap metal, which may include i-in, steel plate.
Loading, weighing, baling and discharging operations are controlled from a central disk. The sequence of main operations is arranged so that no movement can be carried out until the pre
136 ceding operation has been completed.
To drive the press, a pistonless airhydraulic accumulator, working in conjunction with a horizontal three-throw pump, supplies water under a working pressure of 2 tons per sq. in.
The scrap is brought to the press on works trucks, from which it is tipped into a hydraulically operated loading bin. This bin has a weighing device, so that bales of a controlled weight can be produced. When the predetermined weight is reached, the hopper is hydraulically raised and turned over, its contents being discharged into the container of the press. Since the press was installed, labour and transport costs have been reduced by nearly £200 per week, Whereas a I3-ton rail wagon will take only 7 tons of scrap in the loose state, 62 5-cwt. bales, representing a full load, can easily be accommodated. On this basis, a month's output of scrap calls for 26 fewer wagons.
For transporting the bales to the railway siding, the company uses a Bedford-Scamrnell articulated outfit operating with three semi-trailers. The maker of the press was the Loewy Engineering Co., Ltd., 396, The Strand, London, W.C.2.