HINTS ON MAINTENANCE.
Page 30
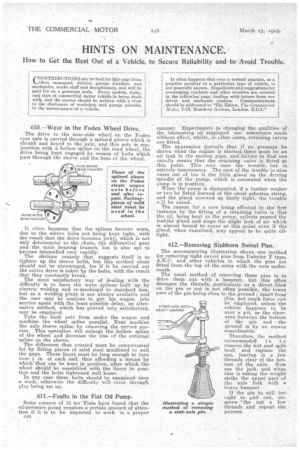
If you've noticed an error in this article please click here to report it so we can fix it.
How to Get the Best Out of a Vehicle, to Secure Reliability and to Avoid Trouble.
610.—Wear in the Foden Wheel Drive.
The drive to the near-side wheel on the Foden Tear axle is carried through a splined sleeve-which is shrunk and keyed to the 'axle, and this acts in conjunction with a hollow spline on the road wheel, the drive being kept engaged by means of bolts which pass through the sleeve and the boss of the wheel.
It often happens that the splines become worn, due to the sleeve bolts not being kept tight, with the result that the drive becomes jerky, which is not only detrimental to the chain, the differential gear and the main bearing brasses, but is also apt to become intensified very rapidly. The obvious remedy that suggests itself is to tighten up the sleeve bolts, but this method alone should not be encouraged, for if it be carried out the entire drive is taken by the bolts, with the result that they constantly break.
The most satisfactory way of dealing with the difficulty is to have the worn splines built up by electric welding and re-machined to standard size, but as a welding plant is not always available and the user may be anxious to get his wagon into service again with the least possible delay, an alternative method, which has proved very satisfactory, may be employed.
Take the back axle from under the wagon and machine the wheel spline parallel. Next machine the axle sleeve spline by removing the curved portion. This operation will enlarge the hollow spline of the wheel and decrease the size of the external spline on the sleeve.
The difference thus created must be compensated for by fitting pieces of mild steel machined to suit the gaps. These liners must be long enough to turn over 1 in. at each end, thus affording a means by which'they can be kept in position, after which the wheel should be assembled with the liners in position and the bolts tightened well home. In any case these bolts should be examined once a week, otherwise the difficulty will recur through play being set up.
611.—Faults in the Fiat Oil Pump.
Some owners of 15 ter-Fiats have found that the oil-pressure pump requires a certain amount of attention if it is to be expected to work in a proper
e46 manner. Experiments in changing the qualities of the lubricating oil employed are sometimes made without effect, whilst, in ether cases, retaining valves are fitted.
The impression prevails that if no pressure be shown when the engine is started,there must be an air leak in the suction pipe, and failure to find one usually means that the retaining -valve is fitted at this point. This may cure the trouble, but is entirely unnecessary. The root of the trouble in nine cases out of ten is the little gland on the driving 'spindle of the pump, which is concealed when the pump is in position.
When the pump is dismantled, if a leather washer or two be fitted instead of the usual asbestos string, and the gland screwed up fairly tight, the trouble 14:11 be cured.
The reason for a cure being effected in the first instance by the fitting of a retaining valve is that the oA being kept in the pump, collects around the leaking gland and stops the slight leak of air which is almost bound to occur at this point even if the gland, when examined, may appear to be quite oiltight.
612.—Removing Stubborn Swivel Pins.
The accompanying illustration shows one method for removing tight swivel pins from Daimler Y type, A.E.G. and other vehicles in which the pins are fitted from the top of the axles with the nuts underneath.
The usual method of removing these pins is to drive them out with a hammer, but this often damages the threads, particularly as a direct blow on the pin or nut is not often possible, the lower part of the pin being close to the ground ; apart from this, not much force can be employed, unless the vehicle happens to be over a pit, as the clearance between the bottom of the pin and the ground is by no means considerable.
STIZIKE WERE WIT1-1 NEAVY WAMMER
Therefore, the method recommended i s t o remove the nut and split bush and replace the nut, leaving it a few threads clear of the bottom of the axle. Now use the jack, and when this is taking the weight strike the upper part of the axle fork with a heavy hammer.
If the pin be still too tight to 011 out, unscrew "the nut a few threads and repeat the process.