Ceramics smash heat barrier for tomorrow's gas turbines
Page 53
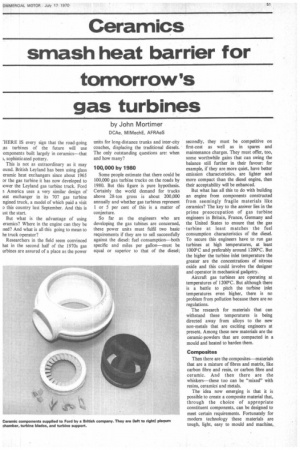
Page 54
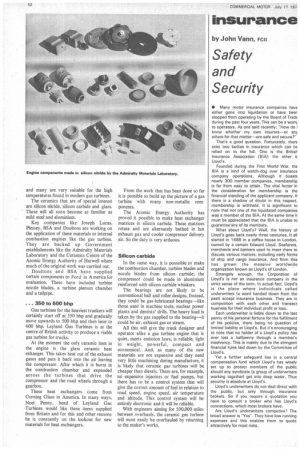
If you've noticed an error in this article please click here to report it so we can fix it.
by John Mortimer
DCAe, MIMechE, AFRAeS
'HERE IS every sign that the road-going as turbines of the future will use omponents built largely in ceramics—that 3, sophisticated pottery.
This is not as extraordinary as it may ound. British Leyland has been using glass eramic heat exchangers since about 1965 or the gas turbine it has now developed to Kower the Leyland gas turbine truck. Ford a America uses a very similar design of eat exchanger in its 707 gas turbine ngined truck, a model of which paid a visit o this country last September. And this is List the start.
But what is the advantage of using eramics? Where in the engine can they be Lsed? And what is all this going to mean to he truck operator?
Researchers in the field seem convinced hat in the second half of the 1970s gas urbines are assured of a place as the power units for long-distance trunks and inter-city coaches, displacing the traditional diesels. The only outstanding questions are: when and how many?
100,000 by 1980 Some people estimate that there could be 100,000 gas turbine trucks on the roads by 1980. But this figure is pure hypothesis. Certainly the world demand for trucks above 28-ton gross is about 200,000 annually and whether gas turbines represent 1 or 5 per cent of this is a matter of conjecture.
So far as the engineers who are developing the gas tubines are concerned, these power units must fulfil two basic requirements if they are to sell successfully against the diesel: fuel consumption—both specific and miles per gallon—must be equal or superior to that of the diesel;
secondly, they must be competitive on first-cost as well as in spares and maintenance charges. They must offer, too, some worthwhile gains that can swing the balance still further in their favour: for example, if they are more quiet, have better emission characteristics, are lighter and more compact than the diesel engine, then their acceptability will be enhanced.
But what has all this to do with building an engine from components constructed from seemingly fragile materials like ceramics? The key to the answer lies in the prime preoccupation of gas turbine engineers in Britain, France, Germany and the United States to ensure that the gas
• turbine at least matches the fuel consumption characteristics of the diesel. To secure this engineers have to run gas turbines at high temperatures, at least 1000PC and preferably around 1200°C. But the higher the turbine inlet temperature the greater are the concentrations of nitrous oxide and this could involve the designer and operator in mechanical gadgetry.
Aircraft gas turbines are operating at temperatures of 1200PC. But although there is a battle to pitch the turbine inlet temperatures even higher, there is no problem from pollution because there are no regulations.
The research for materials that can withstand these temperatures is being directed away from alloys to the new non-metals that are exciting engineers at present. Among these new materials are the ceramic-powders that are compacted in a mould and heated to harden them.
Composites Then there are the composites—materials that are a mixture of fibres and matrix, like carbon fibre and resin, or carbon fibre and ceramic. And then there are the whiskers—these too can be "mixed" with resins, ceramics and Metals.
The idea now emerging is that it is possible to create a composite material that, through the choice of appropriate constituent components, can be designed to meet certain requirements. Fortunately for modern technology these materials are tough, light, easy to mould and machine, and many are very suitable for the high temperatures found in modern gas turbines.
The ceramics that are of special interest are silicon nitride, silicon carbide and glass. These will all soon become as familiar as mild steel and aluminium.
Key companies like Joseph Lucas, Plessey, BSA and Doultons are working on the application of these materials to internal combustion engines like the gas turbine. They are backed up Government establishments like the Admiralty Materials Laboratory and the Ceramics Centre of the Atomic Energy Authority of Harwell where much of the original work was carriied out.
Doultons and BSA have supplied certain components to Ford in America for evaluation. These have included turbine nozzle blades, a turbine plenum chamber and a tailpipe.
... 350 to 600 bhp Gas turbines for the heaviest trunkers will certainly start off at 350 bhp and gradually move upwards to 500 bhp and then later to 600 bhp. Leyland Gas Turbines is at the centre of British activity to produce a viable gas turbine for trucks.
At the moment the only ceramic item in the engine is the glass ceramic heat exhanger. This takes heat out of the exhaust gases and puts it back into the air leaving the compressor. After which it is burnt in the combustion chamber and expanded across the turbines that drive the compressor and the road wheels through a gearbox.
These heat exchangers come from Corning Glass in America. In many ways, Noel Penny, head of Leyland Gas Turbines would like these items supplied from Britain and for this and other reasons he is constantly on the lookout for new materials for heat exchangers. From the work that has been done so far it is possible to build up the picture of a gas turbine with many non-metallic components.
The Atomic Energy Authority has proved it possible to make heat exchanger matrices in silicon carbide. These matrices rotate and are alternately bathed in hot exhaust gas and cooler compressor delivery air. So the duty is very arduous.
Silicon carbide In the same way, it is posssible to make the combustion chamber, turbine blades and nozzle blades from silicon carbide; the compressor could be made in aluminium reinforced with silicon carbide whiskers.
The bearings are not likely to be conventional ball and roller designs. Instead, they could be gas-lubricated bearings—like those used in machine tools, nuclear power plants and dentists' drills. The heavy load is taken by the gas supplied to the bearing—it could be air, exhaust gas or steam.
All this will give the truck designer and operator alike a gas turbine engine that is quiet, meets emission laws, is reliable, light in weight, powerful, compact and economical. And, as many of the new materials are not expensive and they need very little machining during manufacture, it is likely that ceramic gas turbines will be cheaper than diesels. There are, for example, no expensive injectors or fuel pumps, but there has to be a control system that will give the correct amount of fuel in relation to road speed, engine speed, air temperature and altitude. This control system will be entirely electronic and it will be reliable.
With engineers aiming for 500,000 miles between overhauls, the ceramic gas turbine will most easily be overhauled by returning to the maker's works.