Plastics Save 7 cwt.
Page 37
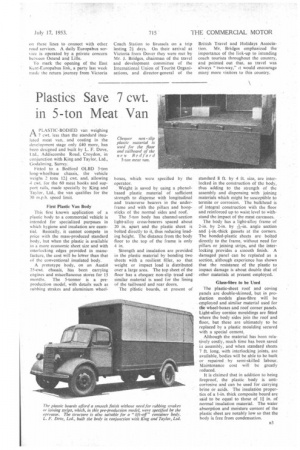
If you've noticed an error in this article please click here to report it so we can fix it.
in 5-ton Meat Van
APLAST1C-BODIED van weighing 7 cwt. less than the standard insulated meat van, and costing in the development stage only £40 more, has been designed and built by L. F. Dove, Ltd., Addiscombe Road, Croydon, in conjunction with King and Taylor, Ltd., G ()dal ming, Surrey.
Fitted to a Bedford OLBD 5-ton long-wheelbase chassis, the vehicle weighs 2 tons 121 cwt. and, allowing 4 cwt. for the 60 meat hooks and support rails, made specially by King and Taylor, Ltd., the van qualifies for the 30 m.p.h. speed limit.
First Plastic Van Body This first known application of a plastic body to a commercial vehicle is intended for specialized purposes in which hygiene and insulation are essential. Basically, it cannot compete in price with the mass-produced standard body, but when the plastic is available in a more economic sheet size and with interlocking edges provided in manufacture, the cost will be lower than that ()I the conventional insulated body.
A prototype body, on an Austin 25-cwt. chassii, has been carrying engines and miscellaneous stores for 15 months. The 5-tonner is a preproduction model, with details such as rubbing strakes and aluminium wheel boxes, which were specified by the operator.
Weight is saved by using a phenolbased plastic material of sufficient strength to dispense with longitudinal and transverse bearers in the underframe and with the pillars and hoopsticks of the normal sides and roof.
The 5-ton body has channel-section light-alloy cross-bearers spaced about 20 in. apart and the plastic sheet is bolted directly to it, thus reducing loading height. The distance from the body floor to the top of the frame is only 4 in.
Strength and insulation are provided in the plastic material by bonding two sheets with a resilient filler, so that weight or impact load is distributed over a large area. The top sheet of the floor has a chequer non-slip tread and similar material is used for the lining of the tailboard and rear doors.
The plastic boards, at present of
standard 8 ft. by 4 ft. size, are interlocked in the construction of the body, thus adding to the strength of the assembly and dispensing with joining materials which might be susceptible to termite or corrosion. The bulkhead is of integral construction with the floor and reinforced up to waist level to withstand the impact of the meat carcasses.
The body has a light-alloy frame of 2-in. by 2-in, by h-in. angle section and -in.-thick gussets at the corners. The bonded-plastic sheets are bolted directly to the frame, without need for pillars or joining strips, and the interlocking provides a smooth finish. A damaged panel can be rcpladed as a section, although experience has shown that the resistance of the plastic to impact damage is about double that of other materials at present employed.
Glass-fibre to be Used
The plastic-sheet roof and eoving panels are double-skinned, but in production models glass-fibre will be employed and similar material used for the wheel-boxes and roof corner panels. Light-alloy cornice mouldings are fitted where the body sides join the roof and floor, but these are ultimately to be replaced by a plastic moulding secured with a special cement.
Although the material has been relatively costly, much time has been saved in assembly, and when standard sheets 7 ft. long, with interlocking joints, are available, bodies will be able to be built or repaired by semi-skilled labour. Maintenance cost will be greatly reduced.
It is claimed that in addition to being fireproof, the plastic body is anticorrosive and can he used for carrying brine or acids. The insulatiOn properties of a 1-in, thick composite board are said to be equal to those of 14 in, of normal insulation material. The water absorption and moisture content of the plastic sheet are notably low so that the body is free from condensation.