The transport warehouse link
Page 50
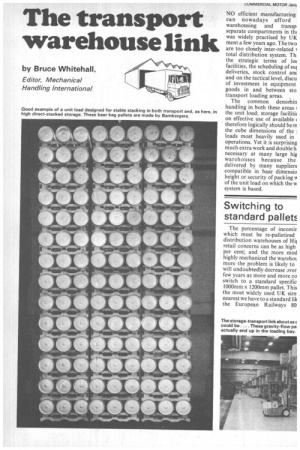
Page 51
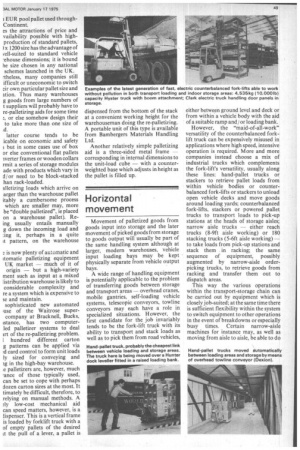
Page 52
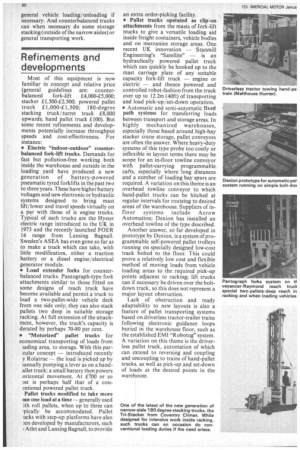
If you've noticed an error in this article please click here to report it so we can fix it.
by Bruce Whitehall, Editor, Mechanical Handling International
NO efficient manufacturing can nowadays afford warehousing and transp. separate compartments in th( was widely practised by UK ment a few years ago. The two are too closely inter-related total distribution system. Th the strategic terms of lo( facilities, the scheduling of sui deliveries, stock control anc and on the tactical level, discu of investment in equipment goods in and between sto transport loading areas.
The common denomin handling in both these areas the unit load; storage facilitit on effective use of available therefore logically should be rn the cube dimensions of the loads most heavily used in operations. Yet it is surprising much extra work and double h. necessary at many large hig warehouses because the delivered by many suppliers compatible in base dimensio height or security of packing NI of the unit load on which thew system is based.
Switching to standard palletf.
The percentage of incomir which must be re-palletized distribution warehouses of Hi) retail concerns can be as high per cent; and the more mod highly mechanized the warehot more the problem is likely to will undoubtedly decrease aver few years as more and more co switch to a standard specific 1000mm x 1200mm pallet. This the most widely used UK size nearest we have to a standard lik the European Railways 80, FUR pool pallet used throughContinent.
es the attractions of price and vailability possible with highproduction of standard pallets, x 1200 size has the advantage of iell-suited to standard vehicle -ehouse dimensions; it is bound he size chosen in any national schemes launched in the UK. -theless, many companies still ifficult or uneconomic to switch ir own particular pallet size and ltion. Thus many warehouses g goods from large numbers of t suppliers will probably have to re-palletizing aids for some time or else somehow design their to take more than one size of .d.
latter course tends to be icable on economic and safety but in some cases use of box or else conventional flat pallets iverter frames or wooden collars rmit a series of storage modules ade with products which vary in d/ or need to be block-stacked han rack-loaded.
alletizing loads which arrive on arger than the warehouse pallet itably a cumbersome process which are smaller may, more be "double palletized", ie placed on a warehouse pallet). Reing usually entails manually g down the incoming load and :ing it, perhaps in a quite it pattern, on the warehouse .t is now plenty of automatic and itomatic palletizing equipment UK market — much of it of origin — but a high-variety ment such as input at a mixed iistribution warehouse is likely to considerable complexity and re a system which is expensive to se and maintain.
sophisticated new automated use of the Waitrose supercompany at Bracknell, Bucks, [stance, has two computerled palletizer systems to deal trt of the re-palletizing problem. I hundred different carton g patterns can be applied via id card control to form unit loads ly sized for conveying and 1g in the high-bay warehouse.
e palletizers are, however, much 'ance of those typically used, can be set to cope with perhaps dozen carton sizes at the most. It timately be difficult, therefore, to relying on manual methods. A ly low-cost mechanical aid can speed matters, however, is a lispenser. This is a vertical frame is loaded by forklift truck with a of empty pallets of the desired It the pull of a lever, a pallet is dispensed from the bottom of the stack at a convenient working height for the warehouseman doing the re-palletizing. A portable unit of this type is available from Bambergers Materials Handling Ltd.
Another relatively simple palletizing aid is a three-sided metal frame — corresponding in internal dimensions to the unit-load cube — with a counterweighted base which adjusts in height as the pallet is filled up.
Horizontal movement
Movement of palletized goods from goods input into storage and the later movement of picked goods from storage to goods output will usually be part of the same handling system although at larger, modern warehouses, vehicle input loading bays may be kept physically separate from vehicle output bays.
A wide range of handling equipment is potentially applicable to the problem of transferring goods between storage and transport areas — overhead cranes, mobile gantries, self-loading vehicle systems, telescopic conveyors, towline conveyors may each have a role in specialized situations. However, the first candidate for the job invariably tends to be the fork-lift truck with its ability to transport and stack loads as well as to pick them from road vehicles, either between ground level and deck or from within a vehicle body with the aid of a suitable ramp and/ or loading bank.
However, the "maid-of-all-work" versatility of the counterbalanced forklift truck can be expensively misused in applications where high speed, intensive operation is required. More and more companies instead choose a mix of industrial trucks which complements the fork-lift's versatility, usually along these lines: hand-pallet trucks or stackers to retrieve pallet loads from within vehicle bodies or counterbalanced fork-lifts or stackers to unload open vehicle decks and move goods around loading yards; counterbalanced fork-lifts, stackers or powered pallet trucks to transport loads to pick-up stations at the heads of storage aisles; narrow aisle trucks — either reach trucks (8-9ft aisle working) or 180 stacking trucks (5-6ft aisle working) — to take loads from pick-up stations and stack them in racking; the same sequence of equipment, possibly augmented by narrow-aisle orderpicking trucks, to retrieve goods from racking and transfer them out to dispatch areas.
This way the various operations within the transport-storage chain can be carried out by equipment which is closely job-suited; at the same time there is sufficient flexibility within the system to switch equipment to other operations in the event of breakdowns or especially busy times. Certain narrow-aisle machines for instance may, as well as moving from aisle to aisle, be able to do general vehicle loading/unloading if necessary. And counterbalanced trucks can when necessary do some storage stacking (outside of the narrow aisles) or general transporting work.
Refinements and developments
Most of this ,equipment is now familiar in concept and relative price (general guidelines are: counterbalanced fork-lift £4,000-£5,000; stacker £1,50042,500; powered pallet truck £1,00041,500; 180-degree stacking truck/turret truck £8,000 upwards; hand pallet truck £100). But some recent refinements and developments potentially increase throughput speeds and cost-effectiveness. For instance: • Electric "indoor-outdoor" counterbalanced fork-lift trucks. Demands for fast but pollution-free working both inside the warehouse and outside in the loading yard have produced a new generation of battery-powered pneumatic tyred forklifts in the past two to three years. These have higher battery voltages and new electronic or hydraulic systems designed to bring mast lift/lower and travel speeds virtually on a par with those of ic engine trucks. Typical of such trucks are the Hyster electric range introduced to the UK in 1973 and the recently launched FOER 14 range from Lansing Bagnall. Sweden's ASEA has even gone so far as to make a truck which can take, with little modification, either a traction battery or a diesel engine/electrical generator module.
• Load extender forks for counterbalanced trucks. Pantograph-type fork attachments similar to those fitted on some designs of reach truck have become available and permit a truck to load a two-pallet-wide vehicle deck from one side only; they can also stack pallets two deep in suitable storage racking. At full extension of the attachment, however, the truck's capacity is derated by perhaps 70-80 per cent.
• "Motorized" pallet trucks for economical transporting of loads from 3ading area, to storage. With this parcular concept — introduced recently y Rolatruc — the load is picked up by • fanually pumping a lever as on a handallet truck; a small battery then powers orizontal movement. At £700 or so 3St is perhaps half that of a con:.ntional powered pallet truck.
Pallet trucks modified to take more 'an one load at a time — generally used ith roll pallets, when up to three can 'pically be accommodated. Pallet ucks with step-up platforms have also :en developed by manufacturers, such ; A tlet and Lansing Bagnall, to provide an extra order-picking facility.
• Pallet trucks operated as clip-on attachments from the masts of fork-lift trucks to give a versatile loading aid inside freight containers, vehicle bodies and on mezzanine storage areas. One recent UK innovation — Stanmill Engineering's "Satellite" — is an hydraulically powered pallet truck which can quickly be hooked up to the mast carriage plate of any suitable capacity fork-lift truck — engine or electric — and thence powered and controlled robot-fashion from the truck over up to 12.2m (40ft) of transporting and load pick-up/set-down operation.
• Automatic and semi-automatic fixed path systems for transferring loads between transport and storage areas. In highly mechanized warehouses, especially those based around high-bay stacker crane storage, pallet conveyors are often the answer. Where heavy-duty systems of this type probe too costly or inflexible in layout terms there may be scope for an in-floor towline conveyor with pallet-carrying programmable carts, especially where long distances and a number of loading bay spurs are required. A variation on this theme is an overhead towline conveyor to which hand-pallet trucks can be hitched at regular intervals for routeing to desired areas of the warehouse. Suppliers of infloor systems include Acrow Automation; Dexion has installed an overhead towline of the type described.
Another answer, so far developed in prototype by Dexion, is a system of programmable self-powered pallet trolleys running on specially designed low-cost track bolted to the floor. This could prove a relatively low cost and flexible method of moving loads from vehicle loading areas to the required pick-up points adjacent to racking; lift trucks can if necessary be driven over the boltdown track, so this does not represent a major layout obstruction.
Lack of obstruction and ready adaptability to new layouts is also a feature of pallet transporting systems based on driverless tractor-trailer trains following electronic guidance loops buried in the warehouse floor, such as the established EMI "Robotug" system. A variation on this theme is the driverless pallet truck, automation of which can extend to reversing and coupling and uncoupling to trains of hand-pallet trucks, as well as pick-up and set-down of loads at the desired points in the warehouse.