Case study: Clipper Logistics
Page 23
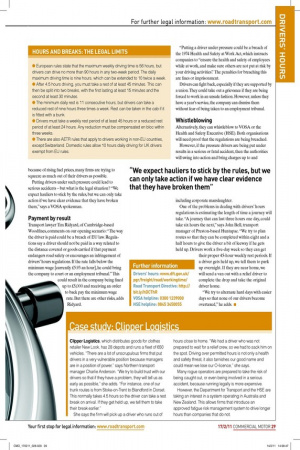
If you've noticed an error in this article please click here to report it so we can fix it.
Clipper Logistics, which distributes goods for clothes retailer New Look, has 28 depots and runs a fleet of 650 vehicles. “There are a lot of unscrupulous firms that put drivers in a very vulnerable position because managers are in a position of power,” says Northern transport manager Charlie Anderson. “We try to build trust with our drivers so that if they have a problem, they will tell us as early as possible,” she adds. “For instance, one of our trunk routes is from Stoke-on-Trent to Blandford in Dorset. This normally takes 4.5 hours so the driver can take a rest break on arrival. If they get held up, we tell them to take their break earlier.”
She says the firm will pick up a driver who runs out of hours close to home. “We had a driver who was not prepared to wait for a relief crew, so we had to sack him on the spot. Driving over permitted hours is not only a health and safety threat, it also tarnishes our good name and could mean we lose our O-licence,” she says.
Many rogue operators are prepared to take the risk of being caught out, or even being involved in a serious accident, because running legally is more expensive.
However, the Department for Transport and the HSE are taking an interest in a system operating in Australia and New Zealand. This allows firms that introduce an approved fatigue risk management system to drive longer hours than companies that do not.