AEC/TASKERS
Page 56
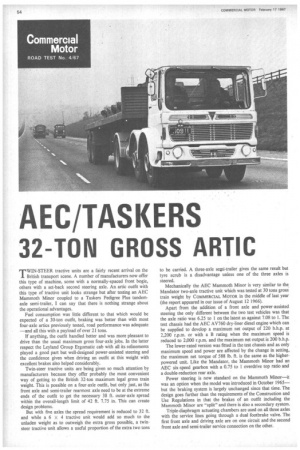
Page 57
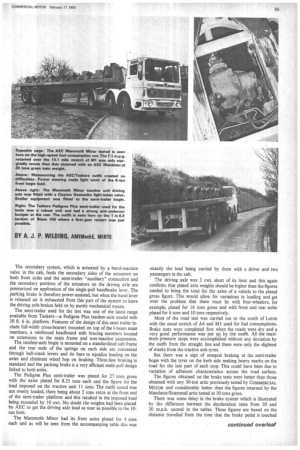
Page 58
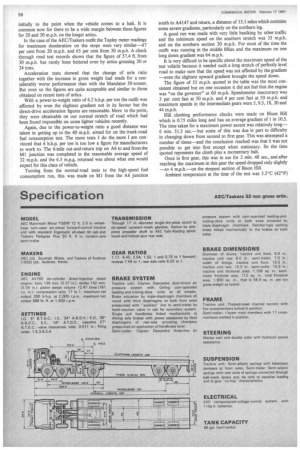
Page 59
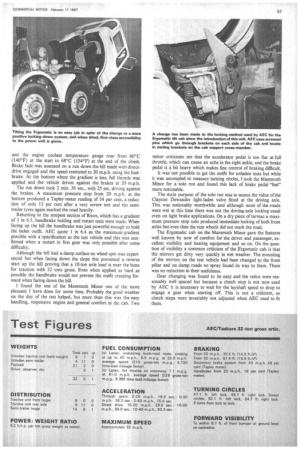
If you've noticed an error in this article please click here to report it so we can fix it.
32-TON GROSS ARTIC
rr WIN-STEER tractive units are a fairly recent arrival on the British transport scene. A number of manufacturers now offer this type of machine, some with a normally-spaced front bogie, others with a set-back second steering axle. An artic outfit with this type of tractive unit looks strange but after testing an AEC Mammoth Minor coupled to a Taskers Pedigree Plus tandemaxle semi-trailer, I can say that there is nothing strange about the operational advantages.
Fuel consumption was little different to that which would be expected of a 30-ton outfit, braking was better than with most four-axle artics previously tested, road performance was adequate —and all this with a payload of over 21 tons.
If anything, the outfit handled better and was more pleasant to drive than the usual maximum gross four-axle jobs. In the latter respect the Leyland Group Ergomatic cab with all its refinements played a good part but well-designed power-assisted steering and the confidence given when driving an outfit at this weight with excellent brakes also helped considerably.
Twin-steer tractive units are being given so much attention by manufacturers because they offer probably the most convenient way of getting to the British 32-ton maximum legal gross train weight. This is possible on a four-axle outfit, but only just, as the front axle and semi-trailer rearmost axle need to be at the extreme ends of the outfit to get the necessary 38 ft. outer-axle spread within the overall-length limit of 42 ft. 7.75 in. This can create design problems.
But with five axles the spread requirement is reduced to 32 and while a 6 x 4 tractive unit would add so much to the unladen weight as to outweigh the extra gross possible, a twinsteer tractive unit allows a useful proportion of the extra two tons to be carried. A three-axle scull-trailer gives the same result but tyre scrub is a disadvantage unless one of the three axles is steered.
Mechanically the AEC Mammoth Minor is very similar to the Mandator two-axle tractive unit which was tested at 30 tons gross train weight by COMMERCIAL MoToR in the middle of last year (the report appeared in our issue of August 12 1966).
Apart from the addition of a front axle and power-assisted steering the only different between the two test vehicles was that the axle ratio was 6.25 to 1 on the latest as against 7.08 to 1. The test chassis had the AEC AV760 dry-liner diesel engine which can be supplied to develop a maximum net output of 220 b.h.p. at 2,200 r.p.m. or with a B rating when the maximum speed is reduced to 2,000 r.p.m. and the maximum net output is 200 b.h.p.
The lower-rated version was fitted in the test chassis and as only maximum speed and power are affected by the change in setting, the maximum net torque of 588 lb. ft. is the same as the higherpowered unit. Like the Mandator, the Mammoth Minor had an AEC six-speed gearbox with a 0.75 to I overdrive top ratio and a double-reduction rear axle.
Power steering is now standard on the Mammoth Minor—it was an option when the model was introduced in October 1965— but the braking system is largely unchanged since that time. The design goes further than the requirements of the Construction and Use Regulations in that the brakes of an outfit including the Mammoth Minor are "split" and there is also a secondary system.
Triple-diaphragm actuating chambers are used on all three axles with the service lines going through a dual footbrake valve. The first front axle and driving axle are on one circuit and the second front axle and semi-trailer service connection on the other.
The secondary system, which is actuated by a hand-reaction valve in the cab, feeds the secondary sides of the actuators on both front axles and the semi-trailer "auxiliary" connection and the secondary portions of the actuators on the driving axle are pressurized on application of the single-pull handbrake lever. The parking brake is therefore power-assisted, but when the hand lever is released air is exhausted from this part of the system to leave the driving axle brakes held on by purely mechanical means.
The semi-trailer used for the test was one of the latest range available from Taskers—a. Pedigree Plus tandem-axle model with 30 ft. 6 in. platform. Features of the design of this semi trailer include full-width cross-bearers mounted on top of the 1-beam main members, a reinforced headboard with bracing members located on extensions to the main frame and non-reactive suspension.
The tandem-axle bogie is mounted on a standardized sub frame and the rear ends of the springs on each side are connected through bell-crank levers and tie bars to equalize loading on the axles and eliminate wheel hop on braking. Three-line braking is standard and the parking brake is a very efficient multi-pull design linked to both axles.
The Pedigree Plus semi-trailer was plated for 27 tons gross with the axles plated for 8.25 tons each and the figure for the load imposed on the tractive unit 11 tons. The outfit tested was not evenly loaded, there being about 2 tons extra at the front end of the semi-trailer platform and this resulted in the imposed-load being exceeded by 10 cwt. No doubt the weights had been placed by AEC to get the driving axle load as near as possible to the 10ton limit.
The Mammoth Minor had its front axles plated for 4 tons each and as will be seen from the accompanying table this was
exactly the load being carried by them with a driver and two passengers in the cab.
The driving axle was 3 cwt. short of its limit and this again confirms that plated axle weights should be higher than the figures needed to bring the total for the axles of a vehicle to the plated gross figure. This would allow for variations in loading and get over the problem that there must be with four-wheelers, for example, plated for 16 tons gross and with front and rear axles plated for 6 tons and 10 tons respectively.
Most of the road test was carried out to the south of Luton with the usual stretch of A6 and M1 used for fuel consumptions. Brake tests were completed first when the roads were dry and a very good performance was put up by the outfit. All the maximum-pressure stops were accomplished without any deviation by the outfit from the straight line and there were only the slightest of marks from the tractive unit tyres.
But there was a sign of unequal braking at the semi-trailer bogie with the tyres on the kerb side making heavy marks on the road for the last part of each stop. This could have been due to variation of adhesion characteristics across the road surface.
The figures obtained on the brake tests were better than those obtained with any 30-ton artic previously tested by COMMERCIAL MOTOR and considerably better than the figures returned by the Mandator/Scammell artic tested at 30 tons gross.
There was some delay in the brake system which is illustrated by the difference between the deceleration rates from 20 and 30 m.p.h. quoted in the tables. These figures are based on the distance travelled from the time that the brake pedal is touched initially to the point when the vehicle comes to a halt. It is common now for there to be a wide margin between these figures for 20 and 30 m.p.h. on the longer artics.
In the case of the AEC/Taskers outfit the Tapley meter readings for maximum deceleration on the stops were very similar-67 per cent from 20 m.p.h. and 65 per cent from 30 m.p.h. A check through road test records shows that the figure of 57.4 ft. from 30 m.p.h. has rarely been bettered even by artics grossing 20 or 24 tons.
Acceleration tests showed that the change of axle ratio together with the increase in gross weight had made for a considerably worse performance than with the Mandator 30-tonner. But even so the figures are quite acceptable and similar to those obtained on recent tests of artics.
With a power-to-weight ratio of 6.2 b.h.p. per ton the outfit was affected by even the slightest gradient not in its favour but the direct-drive acceleration figures are reasonable. More to the point, they were obtainable on our normal stretch of road which had been found impossible on some lighter vehicles recently.
Again, due to the power-to-weight ratio a good distance was taken in getting up to the 40 m.p.h. aimed for on the trunk-road fuel consumption test. The more tests I do the more I am convinced that 6 b.h.p. per ton is too low a figure for manufacturers to work to. The 6-mile out-and-return trip on A6 to and from the M1 junction was completed in the reasonable average speed of 32 m.p.h. and the 6.5 m.p.g. returned was about what one would expect for this class of vehicle.
Turning from the normal-road tests to the high-speed fuel consumption run, this was made on Ml from the A6 junction south to A4147 and return, a distance of 15.1 miles which contains some severe gradients, particularly on the northern leg.
A good run was made with very little baulking by other traffic and the minimum speed on the southern stretch was 35 m.p.h. and on the northern section 30 m.p.h. For most of the time the outfit was running in the middle fifties and the maximum on one long down gradient was 64 m.p.h.
It is very difficult to be specific about the maximum speed of the test vehicle because it needed such a long stretch of perfectly level road to make sure that the speed was not affected by the gradient —even the slightest upward gradient brought the speed down.
The figure of 55 m.p.h. quoted in the table was the most consistent obtained but on one occasion it did not feel that the engine was "on the governor" at 60 m.p.h. Speedometer inaccuracy was 3 per cent fast at 30 m.p.h. and 4 per cent fast at 50 m.p.h. and maximum speeds in the intermediate gears were 5, 9.5, 18, 30 and 44 m.p.h. Hill climbing performance checks were made on Bison Hill which is 0.75 miles long and has an average gradient of 1 in 10.5. The time taken for a maximum power ascent was relatively long6 min. 51.5 sec.—but some of this was due in part to difficulty in changing down from second to first gear. This was attempted a number of times—and the conclusion reached was that it was not possible to get into first except when stationary. So the time quoted represents the climb plus a momentary halt.
Once in first gear, this was in use for 2 min. 48 sec., and after reaching the maximum in this gear the speed dropped only slightly —to 4 m.p.h.—on the steepest section of Bison Hill.
Ambient temperature at the time of the test was 5.5°C (42°F) and the engine coolant temperature gauge rose from 60°C (140°F) at the start to 68°C (154°F) at the end of the climb. Brake fade was assessed on a run down the hill made with directdrive engaged and the speed restricted to 20 m.p.h. using the footbrake. At the bottom where the gradient is less, full throttle was applied and the vehicle driven against the brakes at 20 m.p.h.
The run down took 2 min. 36 sec., with 25 sec. driving against the brakes. A maximum pressure stop from 20 m.p.h. at the bottom produced a Tapley-meter reading of 54 per cent, a reduction of only 13 per cent after a very severe test and the semitrailer tyres again marked the road heavily.
Returning to the steepest section of Bison, which has a gradient of 1 in 6.5, handbrake holding and restart tests were made. When facing up the hill the handbrake was just powerful enough to hold the laden outfit. AEC quote 1 in 6.4 as the maximum gradient possible with a specification as the test vehicle and this was confirmed when a restart in first gear was only possible after some difficulty.
Although the hill had a damp surface no wheel spin was experienced but when facing down the slope this prevented a reverse start up the hill proving that a 10-ton axle load is near the bone for traction with 32 tons gross. Even when applied as hard as possible the handbrake would not prevent the outfit creeping forward when facing down the hill.
I found the test of the Mammoth Minor one of the more pleasant I have done for some time. Probably the good weather on the day of the test helped, but more than this was the easy handling, responsive engine and general comfort in the cab. Two minor criticisms are that the accelerator pedal is too flat at full throttle, which can cause an ache in the right ankle, and the brake pedal is a bit heavy which makes fine control of braking difficult.
It was not possible to get the outfit for unladen tests but while it was uncoupled to measure turning circles, I took the Mammoth Minor for a solo run and found this lack of brake pedal "feel" more noticeable.
The main purpose of the solo run was to assess the value of the Clayton Dewandre light-laden valve fitted at the driving axle. This was noticeably worthwhile and although most of the roads were wet at this time there was not the driving-axle locking usual even on light• brake applications. On a dry piece of tarmac a maximum pressure stop solo produced immediate locking of both front axles but even then the rear wheels did not mark the road.
The Ergomatic cab on the Mammoth Minor gave the features well known by now of comfort for the driver and passenger, excellent visibility and heating equipment and so on. On the question of visibility a common criticism of the Ergomatic cab is that the mirrors get dirty very quickly in wet weather. The mounting of the mirrors on the test vehicle had been changed to the front pillar and on damp roads no spray found its way to them. There was no reduction in their usefulness.
Gear changing was found to be easy and the ratios were reasonably well spaced but because a clutch stop is not now used by AEC it is necessary to wait for the layshaft speed to drop to engage a gear when starting off. This is not a criticism, as clutch stops were invariably not adjusted when AEC used to fit them.