ALUMINIUM
Page 52
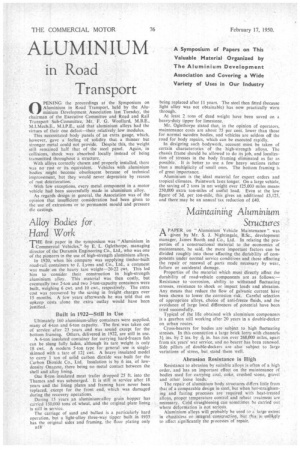
Page 55
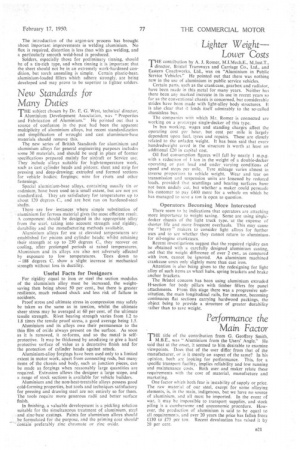
If you've noticed an error in this article please click here to report it so we can fix it.
in Road • Transport
A Symposium of Papers on This Valuable Material Organized by The Aluminium Development Association and Covering a Wide Variety of Uses in Our Industry
0 PENING the proceedings at the Symposium on Aluminium in Road Transport, held by the Muminium Development Association last Tuesday, the chairman of the Executive Committee and Road and Rail Transport Sub-Committee, Mr. E. G. Woollard, Ivf.B.E., M.I.Mech.E., M.I.P.E., said that aluminium alloys had the virtues of their one defect—their, relatively low modulus. This necessitated body panels of an extra gauge, which, • however, gave a feeling of solidity that a thinner but stronger metal could not provide. Despite this, the weight Still remained half that of the steel panel. Again,in collisions, shock was absorbed locally instead of being
transmitted throughout a structure. . . With alloys correctly chosen and properly installed, there was no rust or its equivalent. Vehicles with aluminium bodies might become obsolescent because of technical improvement, but they would never depreciate by reason of rust deterioration.
With few exceptions, every metal component in a motor vehicle had been successfully made in aluminium alloy. As regards design in general, the Association was of the opinion that insufficient consideration had been given to the use of extrusions or to permanent mould and pressure die castings.
Alloy Bodies for Hard Work
T"first paper in the symposium was `.` Aluminium in Commercial Vehicles," by E. L. Oglethorpe, managing director of the Duramin Engineering Co., Ltd., who was one of the pioneers in the use of high-strength aluminium alloys.
In 1920, when his company was supplying timber-built road-rail. containers to J. Lyons and Co., Ltd., a comment was made on the heavy tare weight-20-22 cwt. This led him to consider their construction in high-strength aluminium alloy. This material was then costly, but eventually two 2-ton and two 3-ton-capacity containers were built. weighing 6 cwt. and 10 cwt., respectively. The extra cost was recovered by the saving in freight charges over 15 months. A few years afterwards he was told that on upkeep costs alone the extra outlay would have been justified..
Built in 1922—Still in Use
Ultimately 160 aluminium-alloy containers were supplied, many of 4-ton and 6-ton capacity. The first was taken out of service after 23 years and was sound except for the bottom framing. Others, delivered in 1922, are still in use.
A 6-ton insulated container for carrying hard-frozen fish can be slung fully laden, although its tare weight is only 18 cwt. 6 modern 5-ton type for general use is single
skinned with a tare of 12 cwt. A heavy insulated model to carry 1 ton of solid carbon dioxide was built for the Carbon Dioxide Co., Ltd. Insulation is by 6 ins, of lowdensity Onazote, there being no metal contact between the shell and alloy lining. One 8-ton insulated. meat trailer dropped 25 ft. into the Thames and was submerged. It is still in service after 18 years and the lining plates and framing have never been replaced, except for the front end, which was damaged during the recovery operations. During 15 years an aluminium-alloy grain hopper has carried 150,000 tons of:wheat, and the original plate lining is still in service. The carriage of sand and ballast is a particularly hard operation, but a light-alloy three-way tipper built. in 1933 has the original sides and framing. the floor plating only nI82 being replaced after 11 years. The steel then fitted (because fight alloy was not obtainable) has now practically Worn through.
At least 2 tons of dead weight have been saved on a heavy-duty tipper for limestone.
Mr. Oglethorpe stated that, in the opinion of operators, maintenance costs are about 75 per cent, lower than those for normal wooden bodies, and vehicles are seldom off the road for body repairs, which can be executed rapidly.
In designing such bodywork, account mast be taken of certain characteristics of the high-strength alloys. The chassis frame should be allOwed to do its job, and localization of stresses in the body framing eliminated as far as possible: it s better to use a few heavy sections rather than a multiplicity of 'small ones. The bottom framing is
of great importance. . .
Aluminium is' the, ideal material for export orders and tropical climates. Paintwork lasts longer.' On a large vehicle, the saving of 2 tons in net weight over 125,000 miles means 250,000 extra ton-miles of useful load. Even at the low figure of 3d. per ton-mile, this gives an additional £3,125,and there maybe an annual tax reduction of £40.
.
Maintammg Aluminium
Structures
APARER on "Aluminium Vehicle Maintenance". was by Mr.S. J. Nightingale, B.Sc., .development manager, James Booth and Co., Ltd. In relating the properties of a constructional Material to the economies of maintenance, he said, the more important factors can be divided roughly into those affecting the dufability of components under normal service conditions and those affecting the repair or renewal of parts made necessary by wear, failure or accidental damage.
Properties of the material which must directly affect the durability of road-vehicle components are . as follows:— Resistance to 'corrosion, ability to withstand fluctuating stresses, resistance to shock or impact loads and abrasion. Any means that reduce the flow of galvanic current have been shown to lower the corrosion risk. Careful selection of appropriate alloys, .choice of anti-freeze fluids, 'and the avoidance of large local differences of potential have been tried successfully.
Typical of the life .obtained with aluminium components is a gearbox still working after 20 years in a double-decker on urban routes.• .
.. Cross-bearers for bodies are subject to high fluctuating stresses. In this connection a large brick lorry with channels 31 ins. by 2 ins. by -& in. has run over 268,000 miles, apart from six years' war service, and no bearer has been renewed. Side pillars of double-deckers are also subject to large variations of stress, but stand them well.
Abrasion Resistance is High
Resistance to abrasion by suitable alloys is often of a high order, and has an important effect on the maintenance of bodies used for carrying coal, coke, crushed stone, gravel and 'other loose loads.
The repair of aluminium body. structures differs little from that'of a comparable design in steel, but when hot-straightening and fairing processes are required with heat-treated 1 alloys, proper temperature control and reheat treatment are .. necessary. Cold straightening can sometimes be carried Out where deformation is not serious.
Aluminium alloys will probably be used to large extent in chasSisless or integral construction but this. is tni4ely to affect significantly the processes of repair. The introduction of the argon-arc process has brought about important improvements in welding aluminium. No flux is required, distortion is less than with gas welding, and a particularly smooth weld-bead is produced.
Solders, especially those for preliminary tinning, should be of a tin-rich type, and when tinning it is important that the sheet should not be in an extremely work-hardened condition, but torch annealing is simple. Certain plastic-base, aluminium-loaded fillers which adhere strongly, are being developed and may prove to be superior to lighter solders.
New Standards for
Many Duties THE subject chosen by Dr. E. G. West, technical director,
Aluminium Development Association, was "Properties and Fabrication of Aluminium." He pointed out that a source of confusion in the past had been the apparent multiplicity of aluminium alloys, but recent standardization and simplification of wrought and cast aluminium-base materials should remove this.
The new series of British Standards for aluminium and aluminium alloys for general engineering purposes includes some 30 materials, and should be WO in place of former specifications prepared mainly for aithraft or Service use. They include alloys suitable for high-temperature work, such as cast cylinder heads and pistons; sheet and strip for pressing and deep-drawing; extruded and formed sections for vehicle bodies; forgings; wire for rivets and other fastenings.
Special aluminium-base alloys, containing usually tin or cadmium, have been used to a small extent, but are not yet standardized. They are satisfactory for temperatures up to about 120 degrees C., and are best run on hardened-steel shafts.
There are few instances where simple substitution of aluminium for ferrous material gives the most efficient result. A component should be designed in the appropriate alloy from the star, taking into account strength and rigidity, durability and the manufacturing methods available, Aluminium alloys for use at elevated temperatures are established for pistons and cylinder heads; whilst retaining their strength at up to 250 degrees C., they recover on cooling, after prolonged periods at raised temperatures. Aluminium and its alloys are also not adversely affected by exposure to low temperatures. Tests down to —188 degrees C. show a slight increase irf mechanical strength without loss in ductility.
Useful Facts for Designers
For rigidity equal to iron or steel the section modulus of the aluminium alloy must be increased, the weightsaving then being about 50 per cent., but there is greater resilience, much reduced shock and less risk of failure in accidents.
Proof stress and ultimate stress in compression may safely be taken as the same as in tension, whilst the ultimate sheer stress may be averaged at 60 per cent, of the ultimate tensile strength. Rivet bearing strength varies from 1.2 to 1.8 times the tensile proof stress, a good average being 1.5.
Aluminium and its alloys owe their permanence to the thin film of oxide always present on the surface. As soon as it is removed, it re-forms, and so the metal -is selfprotective. It may be thickened by anodizing to give a hard protective surface of value as a decorative finish and for the protection of cytincler heads against attack. Aluminium-alloy forgings have been used only to a limited extent in motor work, apart from connecting rods, but many items of the chassis and body, such as junction pieces, can be made as forgings when reasonably large quantities are required. Extrusion allows the designer a large scope, and a range of stock sections is available for vehicle builders.
Aluminium and the non-heat-treatable alloys possess good cold-forming properties, but tools and techniques satisfactory for pressing and drawing steel are not entirely so for them. The tools require more generous radii and better surface finish.
In finishing, a valuable development is a pickling solution suitable for the simultaneous treatment of aluminium, steel and zinc-base castings. Paints for aluminium alloys should be formulated for the purpose, and the priming coat should' contain preferably zinc chromate or zinc oxide.
Lighter Weight— Lower Costs THE contribution by A. J. Romer, M.I.Mech.E., M.Inst.T., director, Bristol Tramways and Carriage Co., Ltd., and Eastern Coachworks. Ltd., was on "Aluminium in Public Service Vehicles." He pointed out that there was nothing new in the use of aluminium in public service vehicles.
Certain parts, such as the crankcase, gearbox and radiator, have been made in this metal for many years. Neither has there been any marked increase in its use in recent years so far as the conventional chassis is concerned, but considerable strides have been made with light-alloy body structures. It is also clear that it lends itself admirably to the so-called chassisless bus.
The companies with which Mr. Romer is connected are working on a prototype single-decker of this type. In bus working, wages and standing charges affect the operating cost per hour. but cost per mile is largely dependent upon fuel, tyres and repairs, These are closely related to the unladen weight. It has been said that every hundredweight saved in the structure is worth at least an additional £20 in capital cost.
Oil fuel consumption figures will fall by nearly 1 m.p.g. with a reduction of I ton in the weight of a double-decker operating or part load and under varying conditions of speed and stops per mile. Tyre mileage varies almost in inverse proportion to vehicle weight. Wear and tear on transmission and suspension units are lessened by reduced loads. provided that scantlings and bearing surfaces have not been unduly cut, but whether a maker could persuade his customer to pay £400 more for a vehicle on which he has managed to save a ton is open to question.
Operators Becoming More Interested
There seem to be indications that operators are attaching more importance to weight saying. Some are using singledecker chassis of the light truck type, at the expense of shorter life and more frequent overhauls. This may cause the " heavy " makers to consider light alloys for further uses and to see whether they cannot return to aluminium. for oil-engine crankcases.
Recent investigations suggest that the required rigidity can be obtained with a carefully designed aluminium casting. and that the weight difference of over 2 cwt., as compared with iron, cannot be ignored, An aluminium machined crankcase costs only slightly more than cast iron.
Attention is also being given to the redesigning for light alloy of such items as wheel hubs, spring brackets and brake anchor brackets.
The Bristol concern has been using aluminium extruded H-section for body pillars with timber fillers for panel attachments. From this stage there was a progressive substitution, the main longitudinal rails, for instance, becoming continuous flat sections carrying hardwood packings, the object being to provide a structure of greater durability rather than to save weight.
Performance the Main Factor
THE title of the contribution from G. Geoffrey Smith, M.B.E., was "Aluminium from the Users' Angle." He said that at the onset, it seemed to him desirable to examine viewpoints. Does that of the user differ from that of the manufacturer, or is it merely an aspect of the same? In his opinion, both are looking for performance. This, for a specific transport facility, implies reliability and low running and maintenance costs. Both user. and maker relate these requirements with the cost of material, manufacture and marketing.
One factor which both fear is instability of supply or price. The raw material of our steel, except for some alloying elements, is, in the main, indigenous, but we have no source of aluminium, and all most be imported. In the event of war, it may be impossible to transport supplies, and stock piling is a cumbersome and uneconomic procedure. However, the production of aluminium is said to be equal to all requirements. and over 20 years the price has fallen from £130 td £75 per ton. Recent devaluation has raised it by 20 per cent.