Producer-gas Lecturers
Page 26
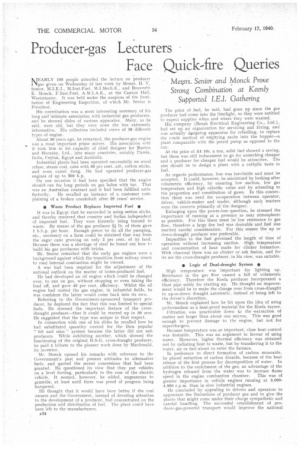
Page 27
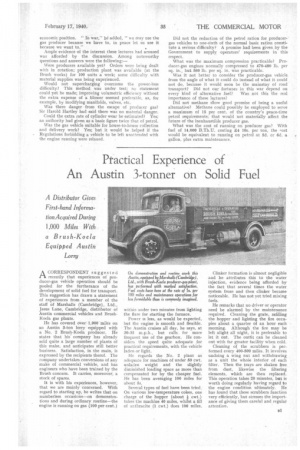
If you've noticed an error in this article please click here to report it so we can fix it.
Face Quick-fire Queries
Messrs. Senior and Monck Prove Strong Combination at Keenly Supported I.E.I. Gathering
NEARLY 100 people attended the lecture on producer gas given on Wednesday of last week by Messrs. H. V. Senior, M.I.E.I., .M.Inst.Fuel, M.I.Mech.E., and Bosworth E. Monck, F.Inst.Fuel, A.M.I.A.E., at the Caxton Hall, Westminster. It was held under the auspices of the Institution of Engineering Inspection, of which Mr. Senior is President.
His contribution was a most interesting summary of his long and intimate association with industrial gas producers, and he showed slides of various apparatus. Many. as he said, were old, but they were none the less extremely informative. His collection included views of 38 different types of engine. .
About 30 years ago, he remarked, the producer-gas engine was a most important prime mover. His association with it took him in his.capacity of chief designer for Ruston and Hornsby, Ltd., into many countries, notably flussia, India, Ceylon, Egypt and Australia.
Industrial plants had been operated successfully on wood refuse, steam coal, coke with 30 per cent. ash, cotton sticks, and even camel dung. He had operated producer-gas engines of up to WI h.p.
On one occasion it had been specified that the engine should' run for long periods on gas laden with tar. That was an Australian contract and it had been fulfilled satis
factorily. He recalled an instance of a customer complaining of a broken crankshaft after 29 years' service.
• Waste Product Replaces Imported Fuel •
It was in Egypt that he succeeded in using cotton sticks, and thereby rendered that country and Sudan independent of imported fuel. They were formerly being burned to waste. By means of the gas producer 2} lb. of them gave 1 b.h.p. per hour. Enough power to do all the pumping, etc., necessary on a farm could be obtained that way from the sugar cane growing on only 2 per cent, of its land. Because there was a shortage of steel he found out how t,) build his gas producers with bricks.
Mr. Senior remarked that the early gas engines were a background against which the transition from railway steam to road internal combustion might be viewed.
A war had been required for the adjustment of the national outlook on the matter of home-produced fuel.
He had developed an oil engine which could be changed over, to run on gas, without stopping or even taking the load off, and gave 40 per cent, efficiency. Whilst the oil engine had ousted the gas engine, in industrial fields, he was confident the latter would come back into its own.
Referring to the Government-sponsored transport producer, he deplored the fact that this was limited to special fuels. He stressed the important feature of the crossdraught producer—that it could he started up in 30 secs. He suggested that the type was unique in that respect.
In connection with one of his slides he recalled how he had substituted quantity control for the then popular " hit and miss " system because the latter did not suit producers. While exhibiting another, which showed the functioning of the original H.S.G. cross-draught producer, he paid a tribute to the pioneer work done by Macdonald, its inventor.
Mr. Monck opened his remarks with reference to the Government's past and present attitudes to alternative fuels, and quoted the recent concessions that had been granted. He questioned its view that they put vehicles on a level footing, particularly in the case of the electric vehicle. It seemed, however, he added, ungenerous to grumble, at least until there was proof of progress being hampered.
He thought that it would have been better if the coal owners and the Government, instead of devoting attention to the development of a producer, had concentrated on the production and distribution of fuel. The plant could have been left to the manufacturers. The price of fuel, he said, had gone up since the gas producer had come into the limelight, so they were entitled to expect supplies when and where they were wanted. His company (Brush Electrical Engineering Co., Ltd.). had set up an organization for servicing and fitting, and was actually designing apparatus for refuelling, to replace the crude method of emptying sacks into the hopper—a plant comparable with the petrol pump as opposed to the can.
At the price of £4 10s. a ton, solid fuel showed a saving, but there was still inducement to go for something cheaper and a producer for cheaper fuel would be attractive. The aim should be to design a plant with a cathplic taste in fuel.
As regards performance, loss was inevitable and must be accepted. It could, however, be minimized by looking after volumetric efficiency, by ensuring low suction, low gas temperature and high calorific value and by attending to the proportion and constitution of gases. In this connection there was need for co-operation between operator, driver, vehicle-maker and trader, although such matters were the concern primarily of. the designer. Enlarging upon the power-loss question, he stressed the importance of running at a pressure as near atmospheric as possible. For this there must be.low resistance to gas flow, therefore a large fire bed was desirable and fuel size merited careful consideration. For this reason the up or down-draught producer was preferable.
Impurities in the fuel governed the length of time of operation without increasing suction. High temperature and concentration of heat made for clinker formation. With charcoal there was no clinker or ash fusion, and for its use the cross-draught producer, in his view, was suitable.
• Logic of Dual-draught System • High temperature was important for lighting up. Resistance in the gas flow caused a fall of volumetric efficiency. Therefore the Kocla producer incorporated a blast pipe solely for starting up. He thought an improvement would be to make the change over from cross-draught to up-or-down draught automatic, instead of being left to the driver's discretion.
Mr. Monck explained how he hit upon the idea of using carborundum as a heat-proof material for the Koela tuyere.
Filtration was practicable down to the -extraction of matter not larger than about one micron. This was good enough to prevent damage to the engine, hut not for superchargers.
Because temperature was so important, close heat control was desirable, This was an argument in favour of using water. Moreover, higher thermal efficiency was obtained not by radiating heat to waste, hut by transferring it to the water, air or fuel about to enter the furnace.
In preference to direct formation of carbon monoxide, he placed reduction of carbon dioxide, because of the heat release of the first process for decomposition of water. In addition to the enrichment of the gas, an advantage of the hydrogen released from the water was to increase flame speed in the engine combustion chamber. This was of greater importance in vehicle engines running at 3,0004.000 r.p.m. than in slow industrial engines.
He concluded by appealing to drivers and operators to appreciate the limitations of producer gas and to give the plants that might come under their charge sympathetic and careful handling. The successful establishment of producer-gas-powered transport would improve the national
economic position. " In war," he added, " we may use the gas producer because we have to, in peace let us use it because we want to."
Ample evidence of the interest these lectures had aroused was afforded by the discussion. Among noteworthy questions and answers were the following:— Were producers available yet? Orders were being dealt with in rotation; production plant was available (at the Brush works) for 100 units a week; some difficulty with material supplies was .being experienced,
Would not supercharging overcome the power-loss difficulty? This method was under test; no statement could yet be made; improving volumetric efficiency without the extra expense of a blower seemed preferable, as, for example, by modifying manifolds, valves, etc.
Was there danger from the escape of producer gas? Sir Harold Hartley had said there was no material danger. Could the extra rate of cylinder wear be estimated? Yes; an authority had given as a basic figure twice that of petrol.
Was the gas vehicle suitable for house-to-house collection and delivery work? Yes; but it would be helped if the Regulations forbidding a vehicle to be left unattended with the engine running were relaxed. Did not the reduction of the petrol ration for producergas vehicles to one-sixth of the normal basic ration constitute a serious difficulty? A promise had been given, by the Government to supply operators' requirements in this respect.
What was the maximum compression practicable? Producer-gas engines normally compressed to 470-480 lb. per sq. in„ but 560 lb, per sq. in, was practicable.
Was it not better to consider the producer-gas vehicle from the angle of what it could do instead of what it could not do, because it would soon be the mainstay of road transport? Did not our fortunes in this war depend on every kind of alternative fuel? Was not this the real importance of these lestures?
Did not methane show good promise of being a useful alternative? Methane could possibly be employed to serve a maximum of 15 per cent, of the country's peace-time petrol requirements; that would not materially affect the future of the inexhaustible producer gas.
What was the cost of running on producer gas? With fuel of 14,000 B.Th.U. costing 44 10s. per ton, the ost would be equivalent to running on petrol at 5d. or 6d. a gallon, plus extra maintenance.