Boilers for Steam Wagons and Tractors.
Page 2
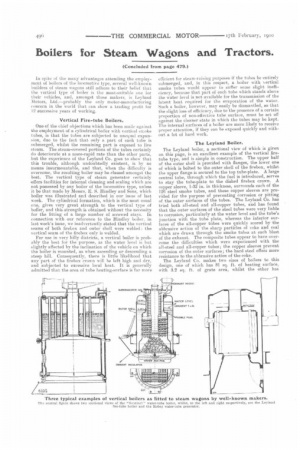
Page 3
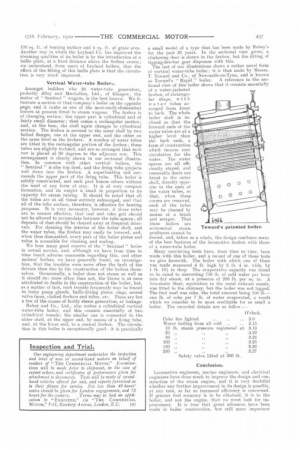
Page 4
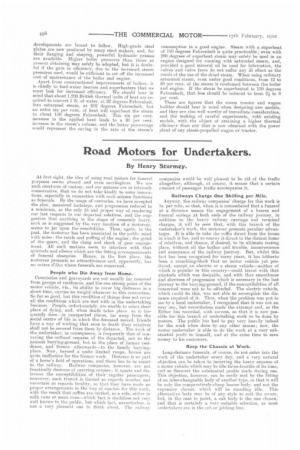
If you've noticed an error in this article please click here to report it so we can fix it.
In spite of the many advantages attending the employment of boilers of the locomotive type, several well-known builders of steam wagons still adhere to their belief that the vertical typo of boiler is the most-suitable one ior their vehicles, and, amoogst those makers, is Leyland Motors, Ltd.—probably the only motor-manufacturing concern in the world that can show a trading profit for 12 successive years of working.
Vertical Fire-tube Boilers.
One of the chief objections which has been made against the employment of a cylindrical boiler with vertical smoke tubes, is that the tubes are subjected to unequal expansion, due to the fact that only a part of each tube is submerged, whilst the remaining part is exposed to live steam. The steam-covered portions of the tubes certainly do deteriorate at a more-rapid rate than the other parts, but the experience of the Leyland Co. goes to show that this trouble, although undoubtedly existent, is by no means insurmountable, and that, when the difficulty is overcome, the resulting boiler may be classed amongst the best. The vertical type of steam generator certainly offers facilities for internal cleaning and scaling which are not possessed by any boiler of the locomotive type, unless it be that made by Messrs. E. S. Hindley and Sons, which boiler was illustrated and described in our issue of last week. The cylindrical formation, which is the most usual one, gives very great strength to the vertical type of boiler, and this strength is obtained without the necessity for the fitting of a large number of screwed stays. In connection with our reference to the Hinclley boiler, in last week's issue, we inadvertently stated that the vertical seams of both firebox and outer shell were welded: the vertical seam of the firebox only is welded.
For use in very hilly districts, a vertical boiler is probably the best for the purpose, as the water level is but slightly affected by the. inclination of the vehicle on which the boiler is mounted, as when ascending or descending a steep hill. Consequently, there is little likelihood that any part of the firebox crown will he left high and dry, and subjected to excessive local heat. It is generally admitted that the area of tube heating-surface is far more efficient for steam-raising rposes if the tubes be entirely
submerged, and, in this respect, a boiler with vertical smoke tubes would appear to suffer some slight inefficiency, because that part of each tube which stands above the water level is not available for the transmission of the latent heat required for the evaporation of the water. Such a boiler, however, may easily be dismantled, so that the slight loss of efficiency, due to the presence of a certain proportion of non-effective tube surface, must be set off against the cleaner state in which the tubes may be kept. The internal surfaces of a boiler are more likely to receive proper attention, if they can be exposed quickly and without a lot of hard work.
The Leyland Boiler.
The Leyland boiler, a sectional view of which is given on this page, is an excellent example of the vertical firetube type, and is simple in construction. The upper half of the outer shell is provided with flanges, the lower one of which is bolted to the outer shell of the firebox, whilst the upper flange is secured to the top tube-plate. A large central tube, through which the fuel is introduced, serves to stay the tube-plate to the dished firebox crown. A copper sleeve, 1-32 in. in thickness, surrounds each of the 126 steel smoke tubes, and these copper sleeves are provided for the purpose of preventing corrosion or pitting of the outer surfaces of the tubes. The Leyland Co. has tried both all-steel and all-copper tubes, and has found that the outer surfaces of the steel tubes were very liable to corrosion, particularly at the water level and the tube's junction with the tube plate, whereas the interior surfaces of the all-copper tubes were quickly scored by the abbrasive action of the sharp particles of coke and coal which are drawn through the smoke tubes at each blast of the exhaust. The composite tubes appear to have overcome the difficulties which were experienced with the all-steel and all-copper tubes; the copper sleeves prevent corrosion of the outer surfaces; the hard steel offers more resistance to the abbrasive action of the coke.
The Leyland Co. makes two sizes of boilers to this design, one of which has 81 sq. ft. of heating surface, with 3.2 sq. ft. of grate area, whilst the other has
100 sq. ft. of heating surface and 4 sq. ft. of grate area. Another way in which the Leyland Co. has improved the steaming qualities of its boiler is by the introduction of a baffle plate, at a fixed distance above the firebox crown ; we understand, from users of Leyland boilers, that the effect of the fitting of this baffle plate is that the circulation is very touch improved.
Vertical Water-tube Boiler..
Amongst builders who lit water-tube generators, probably Alley and MacLellan, Ltd., of Glasgow, the maker of " Sentinel " wagons, is the best known. We illustrate a section of that company's boiler on the opposite page, and it ranks as one of the most-easily-dismantled boilers at present fitted to steam wagons. the firebox is of changing section: the upper part is cylindrical and of fairly small diameter; then comes a rectangular section; and, at the base, the shell again changes to cylindrical section. The firebox is secured to the outer shell by two bolted flanges, one at the upper end, and the other on the same level as the firebars. A number of water tubes are fitted in the rectangular portion of the firebox; these tubes are slightly inclined, and are so arranged that each row is placed at 90 degrees to the adjacent row. This arrangement is clearly shown in our sectional illustration. In common with other vertical boilers, the " Sentinel " is also top fired, and the firing tube projects well down into the firebox. A superheating coil surrounds the upper part of the firing tube. This boiler is solidly constructed, and each part braces others without the need of any form of stay. It is of very compact formation, and its weight is small in proportion to its capacity for steam raising. It should be noted that all the tubes are at all timee entirely submerged, and that all of the tube surface, therefore, is effective for heating purposes. It is very necessary, however, if these tubes are to remain effective, that coal and coke grit should not be allowed to accumulate between the tube spaces; all deposits of dust should be cleared away at frequent intervals. For cleaning the interior of the boiler shell, and the water tubes, the firebox may easily be lowered, and, when thus dismantled, every part of the boiler plates and tubes is accessible for cleaning and scaling.
We hear many good reports of the " Sentinel " boiler in actual service, and, although we have from time to time heard adverse comments regarding this, and other makers' boilers, we have generally found, on investigation, that the troubles were more often the fault of the drivers than due to the construction of the boilers themselves. Occasionally, a boiler does not steam so well as it should do: more often than not, the blame is at once attributed to faults in the construction of the boiler, but, as a matter of fact, such trouble frequently may be traced to leaky pump glands, badly-fitting piston rings, scored valve faces, choked firebars and tubes, etc. These are but a few of the causes of faulty steam generation, or leakage.
Robey and Co., Ltd., also makes a cylindrical vertical water-tribe boiler, and this consists essentially of two cylindrical vessels; the smaller one is connected to the outer shell, at the upper end, by means of a firing tube, and, at the lower end, to a conical firebox. The circulation in this boiler is exceptionally goodit is practically
a small model of a type that has been made by Robey's for the past 20 years. In the sectional view given, a clinkerint; door is .shown in the firebox, but the fitting of tipping-fire-bar gear dispenses with this.
The last of our illustrations shows a rather novel form of vertical water-tube boiler; it is that made by Messrs.
T. Toward and Co., of Newcastle-on-Tyne, and is known as Toward's " Rapid " boiler. A reference to the sectional view of this boiler shows that it consists essentially of a water-jacketed firebox, of rectangular shape, with w a ter tubes arranged from front to back. The whole boiler shell is inclined so that the forward ends of the water tubes are at a higher level than the back ends, a form of construction which insures easy circulation for the water. The water spaces are all efficiently stayed, and removable doors are fitted to the outer shell, directly opposite to the ends of the water tubes, so that, when these covers are removed, each of the tubes may be cleaned by means of a brush and scraper. That these boilers are economical steam producers cannot be denied, and, taken as a whole, the design combines many of the best features of the locomotive firebox with those of a water-tube boiler.
Many convincing tests have, from time to time, been made with this boiler, and a record of one of these tests we give herewith. The boiler with which one of these was made measured 4 ft. high by 2 ft. 4 in. wide, by I ft. 10.,1,in deep. The evaporative capacity was found to be equal to converting 758 lb. of cold water per hour into dry steam, at a. pressure of 200 lb. per sq. in. A live-steam blast, equivalent to the usual exhaust nozzle, was fitted in the chimney, but the boiler was not lagged. The fuel used was coke, the total amount being 108 lb.-one lb. of coke per 7 lb. of water evaporated, a result which we consider to be most creditable for so small a boiler. The recorded details are as follow :—
OA; Towards patented boiler.
Locomotive engineers, marine engineers, and electrical engineers have done much to improve the design and construction of the steam engine, and it is very doubtful whether any further improvement in its design is passible, at any rate, so far as increased efficiency is concerned. If greater fuel economy is to be obtained, it is to the boiler, and not the engine, that we must look for improvement. It is true that great advances have been made in boiler construction, but still more important developments are bound to follow. High-grade steel plates are now produced by many steel makers, and, for their flanging and shaping, powerful hydraulic presses are available. Higher boiler pressures than those at present obtaining may safely be adopted, but it is doubtful if the gain in efficiency, duo to the increased steam pressures used, would be sufficient to set off the increased cost of maintenance of the boiler and engine.
Apart from constructinnal improvements of boilers, it is chiefly to feed-water heaters and superheaters that we must look for increased efficiency. We should bear in mind that about 1,200 British thermal units of heat are required to convert 1 lb. of water, at 32 degrees Fahrenheit, into saturated steam, at 212 degrees Fahrenheit, but an extra six per cent, of heat will superheat the steam to about 150 degrees Fahrenheit. This six per cent. increase in the applied heat leads to a 30 per cent. increase in the steam's volume, and the latter percentage would represent the saving in the rate of the steam's consumption in a good engine. Steam with a superheat of 150 degrees Fahrenheit is quite practicable; even with 200 degrees of superheat steam may safely be used in an engine designed for running with saturated steam, and, provided a good mineral oil be used for lubrication, the valves and valve faces do not suffer any ill effect as the result of the use of the dried steam. When using ordinary saturated steam, even under good conditions, from 12 to 30 per cent. of the steam is condensed between the boiler and engine. If the steam be superheated to 150 degrees Fahrenheit, that loss should be reduced to from 2A to 6 per cent.
These are figures that the steam tractor and wagon builder should bear in mind when designing new models, and they are also well worthy of immediate consideration, and the making of careful experiments, with existing models, with the object of attaining a higher thermal efficiency than any that is now obtained with the power plant of any steam-propelled wagon or tractor.