ELECTRONICS TAKE CONTROL
Page 24
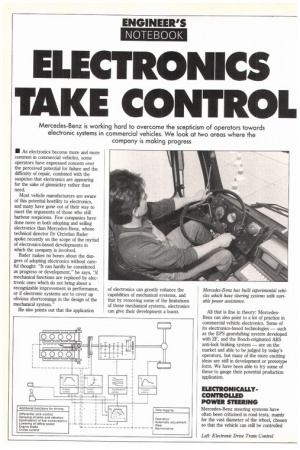
Page 25
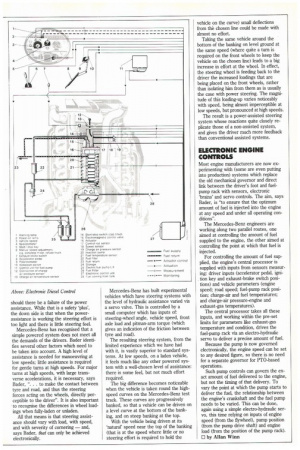
If you've noticed an error in this article please click here to report it so we can fix it.
Mercedes-Benz is working hard to overcome the scepticism of operators towards electronic systems in commercial vehicles. We look at Iwo areas where the company is making progress
• As electronics become more and more common in commercial vehicles, some operators have expressed concern over the perceived potential for failure and the difficulty of repair, combined with the suspicion that electronics are appearing for the sake of gimmickry rather than need.
Most vehicle manufacturers are aware of this potential hostility to electronics, and many have gone out of their way to meet the arguments of those who still harbour suspicions. Few companies have done more in both adopting and selling electronics than Mercedes-Benz, whose technical director Dr Christian Bader spoke recently on the scope of the myriad of electronics-based developments in which the company is involved.
Bader makes no bones about the dangers of adopting electronics without careful thought: "It can hardly be considered as progress or development," he says, "if mechanical functions are replaced by electronic ones which do not bring about a recognizable improvement in performance, or if electronic systems are to cover up obvious shortcomings in the design of the mechanical system."
He also points out that the application of electronics can greatly enhance the capabilities of mechanical systems, and that by removing some of the limitations of those mechanical systems, electronics can give their development a boost. All that is fine in theory: MercedesBenz can also point to a lot of practice in commercial vehicle electronics. Some of its electronics-based technologies — such as the EPS gearshifting system developed with ZF, and the Bosch-originated ABS anti-lock braking system — are on the market and able to be judged by today's operators, but many of the more exciting ideas are still in development or prototype form. We have been able to try some of these to gauge their potential production application.
ELECTRONICALLYCONTROLLED POWER STEERING
Mercedes-Benz steering systems have often been criticised in road tests, mainly for the vast diameter of the wheel, chosen so that the vehicle can still be controlled should there be a failure of the power assistance. While that is a safety 'plus', the down side is that when the powerassistance is working the steering effort is too light and there is little steering feel.
Mercedes-Benz has recognised that a simple powered system does not meet all the demands of the drivers. Bader identifies several other factors which need to be taken into account. A high level of assistance is needed for manoeuvring at low speeds; little assistance is required for gentle turns at high speeds. For major turns at high speeds, with large transverse accelerations, it is necessary, says Bader, ". . . to make the contact between tyre and road, and thus the steering forces acting on the wheels, directly perceptible to the driver". It is also important to recognise the differences in wheel loadings when fully-laden or unladen.
All that means is that steering assistance should vary with load, with speed, and with severity of cornering — and, says Bader, that can only be achieved electronically. Mercedes-Benz has built experimental vehicles which have steering systems with the level of hydraulic assistance varied via a servo valve. This is controlled by a small computer which has inputs of: steering-wheel angle, vehicle speed, front axle load and pitman-arm torque (which gives an indication of the friction between tyre and road).
The resulting steering system, from the limited experience which we have had with it, is vastly superior to standard systems. At low speeds, on a laden vehicle, it feels much like any other powered system with a well-chosen level of assistance: there is some feel, but not much effort required.
The big difference becomes noticeable when the vehicle is taken round the highspeed curves on the Mercedes-Benz test track. These curves are progressively banked, so that a vehicle can be driven on a level curve at the bottom of the banking, and on steep banking at the top.
With the vehicle being driven at its 'natural' speed near the top of the banking (that is at the speed where little or no steering effort is required to hold the vehicle on the curve) small deflections from the chosen line could be made with almost no effort.
Taking the same vehicle around the bottom of the banking on level ground at the same speed (where quite a turn is required on the front wheels to keep the vehicle on the chosen line) leads to a big increase in effort at the wheel. In effect, the steering wheel is feeding back to the driver the increased loadings that are being placed on the front wheels, rather than isolating him from them as is usually the case with power steering. The magnitude of this loading-up varies noticeably with speed, being almost imperceptible at low speeds, but pronounced at high speeds.
The result is a power-assisted steering system whose reactions quite closely replicate those of a non-assisted system, and gives the driver much more feedback than conventional assisted systems.
ELECTRONIC ENGINE CONTROLS
Most engine manufacturers are now experimenting with (some are even putting into production) systems which replace the old mechanical governor and direct link between the driver's foot and fuelpump rack with sensors, electronic 'brains' and servo controls. The aim, says Bader, is "to ensure that the optimum amount of fuel is injected into the engine at any speed and under all operating conditions".
The Mercedes-Benz engineers are working along two parallel routes, one aimed at controlling the amount of fuel supplied to the engine, the other aimed at controlling the point at which that fuel is injected.
For controlling the amount of fuel supplied, the engine's central processor is supplied with inputs from sensors measuring: driver inputs (accelerator pedal, ignition key and exhaust-brake switch positions) and vehicle parameters (engine speed; road speed; fuel-pump rack position; charge-air and fuel temperatures; and charge-air pressure-engine and exhaust-gas temperatures).
The central processor takes all these inputs, and working within the pre-set limits for parameters like exhaust-gas temperature and condition, drives the fuel-pump rack via an electro-hydraulic servo to deliver a precise amount of fuel.
Because the pump is now governed electronically, the engine speed can be set to any desired figure, so there is no need for a separate governor for PTO-based operations.
Such pump controls can govern the exact amount of fuel delivered to the engine, but not the timing of that delivery. To vary the point at which the pump starts to deliver the fuel, the relationship between the engine's crankshaft and the fuel pump needs to be varied. This can be done, again using a simple electro-hydraulic servo, this time relying on inputs of engine speed (from the flywheel), pump position (from the pump drive shaft) and engine load (from the position of the pump rack). 0 by Allan Winn