Panoramic Windscreens in the Making
Page 63
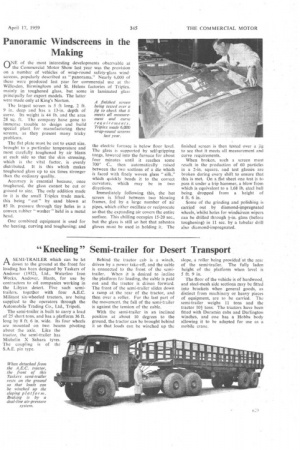
If you've noticed an error in this article please click here to report it so we can fix it.
ONE of the most interesting developments observable at the Commercial Motor Show last year was the provision on a number of vehicles of wrap-round safety-glass wind, screens, popularly described as "panorama." Nearly 6,000 of these were produced last. year for commercial use at the Willesden, Birmingham and St. Helens factories of Triplex. mainly in toughened glass, but some in laminated glass principally for export models. The latter were made only at King's Norton.
The largest screen is 5 ft long, 2 ft. 9 in. deep and has a 13-in, depth of curve. Its weight is 44 lb. and the area 28 sq. ft. The company have gone to immense trouble to design and build special plant for manufacturing these screens, as they present many tricky problems.
The flat plate must be cut to exact size, brought to a particular temperature and most carefully toughened by air blasts at each side so that the skin stressing, which is the vital factor, is evenly distributed. It is this which makes toughened glass up to six times stronger than the ordinary quality.
Accuracy is essential because, once toughened, the glass cannot be cut or ground to size. The only addition made to it is the small Triplex trade mark, this being " cut " by sand blown at 85 lb. pressure through tiny holes in a convex rubber " washer " held in a metal head.
One combined equipment is used for the heating, curving and toughening; and the electric furnace is below floor level. The glass is supported by self-gripping tongs, lowered into the furnace for about four minutes until it reaches some 700* C., then automatically raised between the two sections of a die which is faced with finely woven glass "silk," which quickly bends it to the correct curvature, which may be in two directions.
Immediately following this, the hot screen is lifted between two blowing frames, fed by a large number of air pipes, which either oscillate or reciprocate so that the expanding air covers the entire surface. This chilling occupies 15-20 sec., but the glass is still so hot that asbestos gloves must be used in holding it. The finished screen is then tested over a jig to see that it meets all measurement and curve requirements.
When broken, such a screen must result in the production of 60 particles in a 2-in. square, and test glasses are broken during every shift to ensure that this is met. On kflat sheet one test is to pass it under a trip hammer, a blow from which is equivalent to a 1.68 lb. steel ball being dropped from a height of 4 ft. 6 in.
Some of the grinding and polishing is carried out by diamond-impregnated wheels, whilst holes for windscreen wipers can be drilled through I-in. glass (before toughening) in 11 sec. by a tubular drill also diamond-impregnated.