DETACHABLE FLATS SPEED DELIVERIES
Page 118
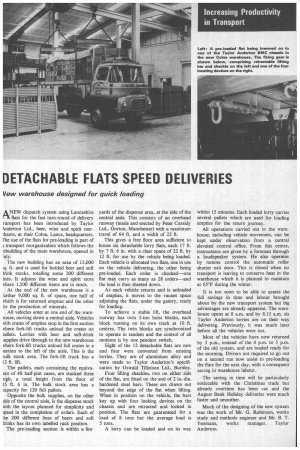
If you've noticed an error in this article please click here to report it so we can fix it.
Vew warehouse designed for quick loading A NEW dispatch system using Lancashire rX flats for the fast turn round of delivery
ransport has been introduced by Taylor knderton Ltd., beer, wine and spirit merthants, at their Colne, Lanes, headquarters.
[he use of the flats for pre-loading is part of transport reorganization which follows the 'ebuilding of the main warehouse, opened in ruly.
The new building has an area of 13,000 Q.. ft. and is used for bottled beer and soft
Irink stocks, totalling some 200 different ines. It adjoins the wine and spirit store vhere 1,500 different items are in stock.
At the end of the new warehouse is a 'urther 9,000 sq. ft. of space, one half of vhich is for returned empties and the other or the production of minerals.
All vehicles enter at one end of the warelouse, moving down a central aisle. Vehicles vith crates of empties stop in the first section sphere fork-lift trucks unload the crates on )allets. Lorries with beer and soft-drink ;upplies drive through to the new warehouse there fork-lift trucks unload full crates in a iection to the left of the aisle. This is the )ulk stock area. The fork-lift truck has a 12 ft. lift.
The pallets, each containing the equivaent of 48 half-pint cases, are stacked three ligh, a total height from the floor of 15 ft. 6 in. The bulk stock area has a ;opacity for 120 full pallets.
Opposite the bulk supplies, on the other ;ide of the central aisle, is the dispense stock vith the layout planned for simplicity and ;peed in the completion of orders. Each of :he 200 different lines of beers and soft kinks has its own labelled rack position.
The pre-loading section is within a few yards of the dispense area, at the side of the central aisle. This consists of an overhead runway (made and erected by Peter Cassidy Ltd., Gorton, Manchester) with a maximum travel of 64 ft. and a width of 22 ft.
This gives a free floor area sufficient to house six detachable lorry flats, each 17 ft. by 7 ft. 6 in. with a clear space of 22 ft. by 12 ft. for use by the vehicle being loaded. Each vehicle is allocated two flats, one in use on the vehicle delivering, the other being pre-loaded. Each order is checked—one flat may carry as many as 28 orders—and the load is then sheeted down.
As each vehicle returns and is unloaded of empties, it moves to the vacant space adjoining the flats, under the gantry, ready for loading.
To achieve a stable lift, the overhead runway has twin 5-ton hoist blocks, each block running on its own track at 10 ft. centres. The twin blocks are synchronized to operate in tandem and the control of all motions is by one pendant switch.
Eight of the 12 detachable flats are new and four were converted from existing lorries. They are of aluminium alloy and were made to Taylor Anderton's specification by Oswald Tillotson Ltd., Burnley.
Four lifting shackles, two on either side of the flat, are fitted on the end of 2 in.-dia. hardened steel bars. These are drawn out beyond the edge of the flat when lifting. When in position on the vehicle, the bars key up with four locking devices on the chassis and are retracted and locked in position. The flats are guaranteed for a load of 8 tons but the average load is 5 tons.
A lorry can be loaded and on its way within 15 minutes. Each loaded lorry carries several pallets which are used for loading empties for the return journey.
All operations carried out in the warehouse, including vehicle movement, can be kept under observation from a central elevated control office. From this centre, instructions are giveri by a foreman through a loudspeaker system. He also operates by remote control the automatic roller shutter exit door. This is closed when no transport is leaving to conserve heat in the warehouse which it is planned to maintain at 65°F during the winter.
It is too soon to be able to assess the full savings in time and labour brought about by the new transport system but big advantages are already apparent. The warehouse opens at 8 a.m. and by 8.15 a.m. six Taylor Anderton lorries are on their way delivering. Previously, it was much later before all the vehicles were out.
Most of the vehicles have now returned by 3 p.m., instead of the 4 p.m. to 5 p.m. of the old system, and are loaded ready for the morning. Drivers not required to go out on a second run now assist in pre-loading the flats for the next day, with a consequent saving in warehouse labour.
The saving in time will be particularly noticeable with the Christmas trade but already overtime has been cut and the August Bank Holiday deliveries were much faster and smoother.
Much of the designing of the new system was the work of Mr. G. Robinson, works study and methods engineer and Mr. B. T. Yeomans, works manager, Taylor Anderton.