Specialists are best
Page 31
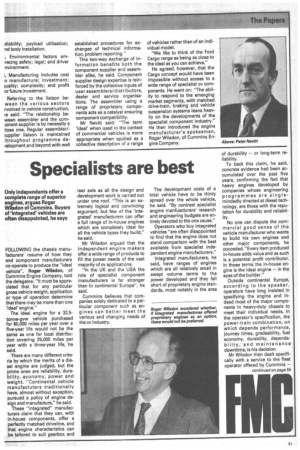
Page 33
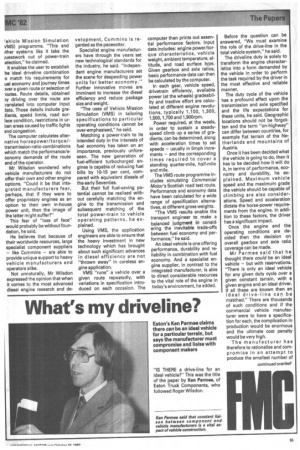
Page 34
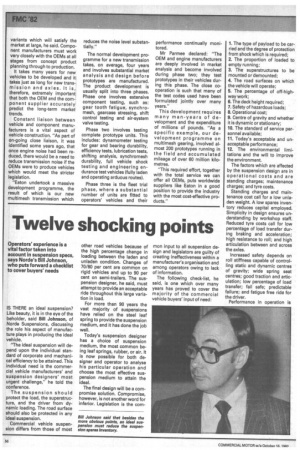
If you've noticed an error in this article please click here to report it so we can fix it.
Only independents offer a complete range of superior engines, argues Roger Wilsdon of Cummins. Buyers of 'integrated' vehicles are often disappointed, he says FOLLOWING the chassis manufacturers' resume of how they and component manufacturers co-operate to produce the "ideal vehicle", Roger Wilsdon, of Cummins Engine Company, told the delegates: "It must be appreciated that for any particular gross vehicle weight, application or type of operation determine that there may be more than one 'ideal' engine."
The ideal engine for a 32.5tonne-gvw vehicle purchased for 80,000 miles per year over a five-year life would not be the same as one for local distribution covering 25,000 miles per. year with a three-year life, he said.
There are many different criteria by which the merits of a diesel engine are judged, but the prime ones are reliability, durability, economy, power and weight. "Continental vehicle manufactuters traditionally have, almost without exception, pursued a policy of engine design and manufacture," he said.
These "integrated" manufacturers claim that they can, with in-house components, offer a perfectly matched driveline, and that engine characteristics can be tailored to suit gearbox and rear axle as all the design and development work is carried out under one roof. "This is an extremely logical and convincing argument, but few of the 'integrated' manufacturers can offer a full range of in-house engines which are completely ideal for all the vehicle types they build," he said.
Mr Wilsdon argued that the independent engine makers offer a wide range of products to fill the power needs of the vast majority of cv applications.
"In the UK and the USA the role of specialist component manufacturers is far stronger than in continental Europe", he said.
Cummins believes that companies solely dedicated to a particular component such as engines can better meet the various and changing needs of the cv industry. The development costs of a total vehicle have to be thinly spread over the whole vehicle, he said. "By contrast specialist engine manfuacturers' research and engineering budgets are entirely devoted to the one cause."
Operators who buy integrated vehicles "are often disappointed to find that the engine does not stand comparison with the best available from specialist independent engine manufacturers."
Integrated manufacturers, he said, have ranges of engines which are all relatively small in swept volume terms to the power developed and they fall short of proprietary engine standards, most notably in the area of durability — or long-term reliability.
To back this claim, he said, concrete evidence had been accumulated over the past five years, confirming the fact that heavy engines developed by companies whose engineering programmes are singlemindedly directed at diesel technology, are those with the reputation for durability and reliability.
No one can dispute the commercial good sense of the vehicle manufacturer who wants to build his own engines and other major components, he conceded. "Every item produced in-house adds value and as such is a potential profit contributor. In those terms the in-house engine is the ideal engine — in the eyes of the builder."
Outside continental Europe, according to the speaker, operators have long insisted in specifying the engine and indeed most of the major components in heavy-duty chassis to meet their individual needs. In the operator's specification, the power-train combination, on which depends performance, journey times, gradeability, fuel economy, durability, dependability, and maintenance downtime, is his decision.
Mr Wilsdon then dealt specifically with a service to the fleet operator offered by Cummins —
'ehicle Mission Simulation VMS) programme. "This and ther systems like it take the puesswork out of power-train election," he claimed.
It enables the user to establish he ideal driveline combination o match his requirements for uel economy and journey times war a given route or selection of .outes. Route details, obtained )y driving over the route are :ranslated into computer input late. Those details include graiients, speed limits, road surface condition, restrictions in urban areas caused by traffic lights and congestion.
The computer calculates alternative horsepower/torque!transmission-ratio combinations which match the performance/economy demands of the route and of the operator.
Mr Wilsdon wondered why vehicle manufacturers do not offer their own and other engine options. "Could it be that integrated manufacturers fear, perhaps, that if they were to offer proprietary engines as an option to their own in-house power unit, then the image of the latter might suffer?"
This fear of "loss of face" would probably be without foundation, he said.
He believes that because of their worldwide resources, large specialist component suppliers — like Cummins — are able to provide unique support to heavy vehicle manufacturers and operators alike.
Not unnaturally, Mr Wilsdon expressed the opinion that when it comes to the most advanced diesel engine research and de velopment, Cummins is regarded as the pacesetter.
Specialist engine manufacturers have through the years set new technological standards for the industry, he said. "Independent engine manufacturers set the scene for despeeding power units for better economy." Further innovative moves are imminent to increase the diesel efficiency and reduce package size and weight.
"The uses of Vehicle Mission Simulation (VMS) in tailoring specifications to particular operating conditions cannot be over-emphasised," he said.
Matching a power-train to its intended duty in the interests of fuel economy has taken on an importance, previously unforeseen. The new generation of fuel-efficient turbocharged engines is capable of reducing fuel bills by 10-15 per cent, compared with equivalent diesels of the early Seventies.
But their full fuel-saving potential cannot be realised without carefully matching the engine to the transmission and subsequent matching of the total power-train to vehicle operating patterns, he explained.
Using VMS, the application engineers are able to ensure that the heavy investment in new technology which has brought about such significant advances in diesel efficiency are not "thrown away" in careless engine application.
VMS "runs" a vehicle over a given route repeatedly, with variations in specification introduced on each occasion. The computer then prints out essential performance factors. Input data includes: engine power/torque characteristics, vehicle weight, ambient temperature, altitude, and road surface type. Given gearbox and axle ratios, basic performance data can then be calculated by the computer.
In each gear, vehicle speed, drivetrain efficiency, available power (at the wheels) gradeability and tractive effort are calculated at different engine revolutions, typically 1,100, 1,300, 1,500,1,700 and 1,900rpm.
Power required, at the weels, in order to sustain a steadyspeed climb up a series of gradients, can be determined, along with acceleration times to set speeds — usually in 5mph increments — and the corresponding times required to cover a standing quarter-mile, half-mile and mile.
The VMS route programme includes simulating Commercial Motor's Scottish road test route. Performance and economy data have been calculated for a wide range of specification alternatives, at different gross weights.
"The VMS results enable the transport engineer to make a balanced iudgment in considering the inevitable trade-offs between fuel economy and performance," he said.
An ideal vehicle is one offering performance, durability and reliability in combination with fuel economy. And a specialist engine supplier, in contrast to the integrated manufacturer, is able to direct considerable resources to the vital role of the engine in today's environment, he added. Before the question can be answered, "We must examine the role of the drive-line in the total vehicle system," he said.
The driveline duty is solely to transform the engine characteristics into a form demanded by the vehicle in order to perform the task required by the driver in the most effective and reliable manner.
The duty cycle of the vehicle has a profound effect upon the transmission and axle specified and the life expectations for these units, he said. Geographic locations should not be forgotten and the term "on-highway" can differ between countries, for example flat terrain of the Netherlands and mountains of Austria.
Once it has been decided what the vehicle is going to do, then it has to be decided how it will do it, in terms of performance, economy and durability, he explained. Maximum vehicle speed and the maximum grade the vehicle should be capable of climbing are also considerations. Speed and acceleration dictate the horse-power requirements from the engine. In addition to these factors, the driver has a significant impact.
Once the engine and the operating conditions are decided then the decision on overall gearbox and axle ratio coverage can be made.
Mr Parmee said that he thought there could be an ideal vehicle — but with reservations. "There is only an ideal vehicle for any given duty cycle over a given constant terrain, with a given engine and an ideal driver. If all these are known then an ideal drive-line can be matched." There are thousands of such conditions and if the commercial vehicle manufacturer were to have a specification for each, the complication in production would be enormous and the ultimate cost penalty would be very high.
The manufacturer has therefore to rationalise and compromise in an attempt to produce the smallest number of variants which will satisfy the market at large, he said. Component manufacturers must work very closely with the OEMs at all stages from concept product planning through to production.
It takes many years for new vehicles to be developed and it takes just as long for new transmission and axles. It is,. therefore, extremely important that both the OEM and the component supplier accurately predict the long-term market trends.
Constant liaison between vehicle and component manufacturers is a vital aspect of vehicle construction. "As part of on-going close liaison, it was identified some years ago, that once engine noise had been reduced, there would be a need to reduce transmission noise if the OEMs were to produce vehicles which would meet the stricter legislation.
"Eaton undertook a massive development programme, the result of which is our new multimesh transmission which reduces the noise level substantially."
The normal development programme for a new transmission takes, on average, four years and involves substantial market analysis and design before prototypes are manufactured. The product development is usually split into three phases. Phase one involves extensive component testing, such as: gear tooth fatigue, synchromesh, gearcase stressing, shift control testing and air-system valve testing.
Phase two involves testing complete prototype units. This includes: dynamometer testing for gear and bearing durability, efficiency tests, lubrication tests, shifting analysis, synchromesh durability, full vehicle shock testing and engineering endurance test vehicles (fully laden and operating arduous routes).
Phase three is the fleet trial phase, where a substantial number of units are fitted to operators' vehicles and their performance continually monitored.
Mr Parmee declared: "The OEM and engine manufacturers are deeply involved in market analysis and become involved during phase two; they test prototypes in their vehicles during this phase. The close cooperation is such that many of the test codes used have been formulated jointly over many years."
This development requires many man-years of development and the expenditure of millions of pounds. "As a specific example, our development programme on multimesh gearing, involved almost 200 prototypes running in the field and accumulated mileage of over 60 million kilometres.
"This required effort, together with the total service we can offer all OEMs, puts worldwide suppliers like Eaton in a good position to provide the industry with the most cost-effective products."