road and workshop
Page 51
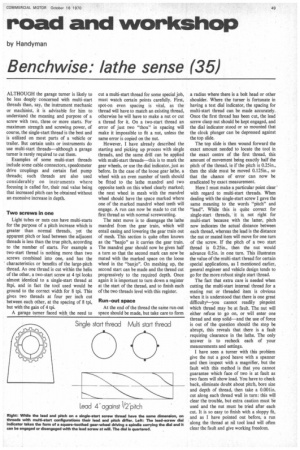
If you've noticed an error in this article please click here to report it so we can fix it.
by Handyman
Benchwise: lathe sense (35)
ALTHOUGH the garage turner is likely to be less deeply concerned with multi-start threads than, say, the instrument mechanic or machinist, it is advisable for him to understand the meaning and purpose of a screw with two, three or more starts. For maximum strength and screwing power, of course, the single-start thread is the best and is utilized on most parts of a vehicle or trailer. But certain units or instruments do use multi-start threads—although a garage turner is rarely required to cut them.
Examples of some multi-start threads include some cable connectors, speedometer drive couplings and certain fuel pump threads; such threads are also used considerably on instruments where focusing is called for, their real value being that increased pitch can be obtained without an excessive increase in depth.
Two screws in one Light tubes or nuts can have multi-starts for the purpose of a pitch increase which is greater than normal threads, yet the apparent pitch or lead between the adjacent threads is less than the true pitch, according to the number of starts. For example a two-start thread is nothing more than two screws combined into one, and has the ' characteristics or benefits of the large-pitch thread. As one thread is cut within the helix of the other, a two-start screw at 4 tpi looks almost identical to a single-start thread at 8tpi, and in fact the tool used would be ground to the correct width for 8 tpi. This gives two threads at four per inch cut between each other, at the spacing of 8 tpi, but with the gain of 4 tpi.
A garage turner faced with the need to
cut a multi-start thread for some special job, must watch certain points carefully. First, spot-on even spacing is vital, as the thread will have to match an existing thread, otherwise he will have to make a nut or cut a thread for it. On a two-start thread an error of just two "thou" in spacing will make it impossible to fit a nut, unless the same error is copied on the nut.
However, I have already described the starting and picking up process with single threads, and the same drill can be applied with multi-start threads—this is to mark the gear wheels, or use the dial indicator, just as before. In the case of the loose gear lathe, a wheel with an even number of teeth should be fitted to the lathe mandrel and two opposite teeth on this wheel clearly marked; the next wheel in mesh with the mandrel wheel should have the space marked where one of the marked mandrel wheel teeth will engage. A run can now be made to cut the first thread as with normal screwcutting.
The next move is to disengage the lathe mandrel from the gear train, which will entail easing and lowering the gear train out of mesh. This section is quite often known as the "banjo" as it carries the gear train. The mandrel gear should now be given half a turn so that the second mark can now be mated with the marked space on the loose wheel in the "banjo". On meshing up, the second start can be made and the thread cut progressively to the required depth. Once again it is important to turn down a register at the start of the thread, and to finish each of the two threads level with this register.
Run-out space
At the end of the thread the same run-out space should be made, but take care to form a radius where there is a bolt head or other shoulder. Where the turner is fortunate in having a test dial indicator, the spacing for multi-start thread can be made accurately. Once the first thread has been cut, the lead screw clasp nut should be kept engaged, and the dial indicator stood or so mounted that the clock plunger can be depressed against the top slide.
The top slide is then wound forward the exact amount needed to locate the tool in the exact centre of the first thread, this amount of movement being exactly half the pitch of the thread, ie if the pitch is 0.25 in., then the slide must be moved 0.125in., so that the chance of error can now be eradicated by exact measurement.
Here I must make a particular point clear' with regard to multi-start threads. When dealing with the single-start screw I gave the same meaning to the words "pitch" and "lead". While this is quite correct for single-start threads, it is not right for multi-start because with the latter, pitch now indicates the actual distance between each thread, whereas the lead is the distance the nut or mated item will move for one turn of the screw. If the pitch of a two start thread is 0.25in., then the nut would advance 0.5in. in one turn. This illustrates the value of the multi-start thread for certain special applications, as I mentioned earlier, general engineer and vehicle design tends to go for the more robust single start thread.
The fact that extra care is needed when cutting the multi-start internal thread for a mating nut or threaded item is obvious when it is understood that there is one great difficulty—you cannot readily pinpoint which thread may be at fault. The nut will either refuse to go on, or will enter one thread and stop solid—and the use of force is out of the question should the stop be abrupt, this reveals that .there is a fault requiring clearance in the lathe. The only answer is to recheck each of your measurements and settings.
I have seen a turner with this problem give the nut a good heave with a spanner and then inspect with a magnifier, but the fault with this method is that you cannot guarantee which face of two is at fault as two faces will show load. You have to check back, eliminate doubt about pitch, bore size and depth of thread, then take a 0.001in. cut along each thread wall in turn: this will clear the trouble, but extra caution must be used and the nut must be tried after each cut. It is so easy to finish with a sloppy fit, and as I have pointed out before, a run along the thread at nil tool load will often clear the fault and give working freedom.