E PACKAGE
Page 30
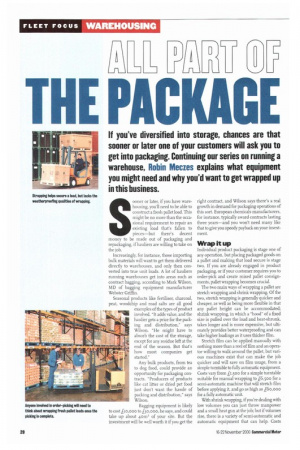
Page 31
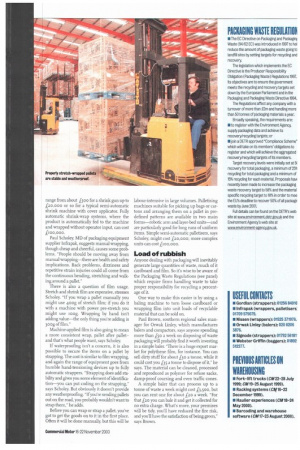
If you've noticed an error in this article please click here to report it so we can fix it.
If you've diversified into storage, chances are that sooner or later one of your customers will ask you to get into packaging. Continuing our series on running a warehouse, Robin Meczes explains what equipment you might need and why you'd want to get wrapped up in this business.
Sooner or later, if you have warehousing, you'll need to be able to construct a fresh pallet load. This might be no more than the occasional requirement to repair an existing load that's fallen to pieces—but there's decent money to be made out of packaging and repackaging, if hauliers are willing to take on the job.
Increasingly, for instance, those importing bulk materials will want to get them delivered directly to warehouses, and only then converted into true unit loads. A lot of hauliers running warehouses get into areas such as contract bagging, according to Mark Wilson, MD of bagging equipment manufacturer Webster Griffin.
Seasonal products like fertiliser, charcoal, peat, woodchip and road salts are all good examples of the types of product involved. "It adds value, and the haulier gets a price for the packing and distribution," says Wilson. "He might have to absorb the cost of the storage, except for any residue left at the end of the season. But that's how most companies get started."
Any bulk products, from tea to dog food, could provide an opportunity for packaging contracts. "Producers of products like cat litter or dried pet food just don't want the hassle of packing and distribution," says Wilson.
Bagging equipment is likely to cost £10,000 to £30,000, he says, and could take up about 4o m2 of your site. But the investment will be well worth it if you get the
right contract, and Wilson says there's a real growth in demand for packaging operations of this sort. European chemicals manufacturers, for instance, typically award contracts lasting three years—and you worst need many like that to give you speedy payback on your investment.
Wrap ft Up
Individual product packaging is stage one of any operation, but placing packaged goods on a pallet and maldng that load secure is stage two. If you are already engaged in product packaging, or if your customer requires you to order-pick and create mixed pallet consignments, pallet wrapping becomes crucial.
The two main ways of wrapping a pallet are stretch wrapping and shrink wrapping. Of the two, stretdi wrapping is generally quicker and cheaper, as well as being more flexible in that any pallet height can be accommodated; shrink wrapping, in which a "hood" of a fixed size is pulled over the load and heat-shrunk, takes longer and is more expensive, but ultimately provides better waterproofing and can take higher loadings as it uses thicker film.
Stretch film can be applied manually with nothing more than a reel of film and an operator willing to walk around the pallet, but various machines exist that can make the job quicker and will save on film usage, from a simple turntable to fully automatic equipment. Costs vary from £1,500 for a simple turntable suitable for manual wrapping to /6,5ao for a semi-automatic machine that will stretch film before applying it, and go as high as £60,000 for a fully automatic unit.
With shrink wrapping, if you're dealing with low volumes you can just throw manpower and a small heat gun at the job; but if volumes rise, there is a variety of semi-automatic and automatic equipment that can help. Costs range from about £300 for a shrink gun up to £20,000 Or so for a typical semi-automatic shrink machine with cover applicator. Fully automatic shrink-wrap systems, where the product is automatically fed to the machine and wrapped without operator input, can cost ficio,000.
Paul Scholey, MD of packaging equipment supplier lnfrapalc, suggests manual wrapping, though cheap and cheerful, causes some problems. "People should be moving away from manual wrapping—there are health and safety implications. Back problems, dizziness and repetitive strain injuries could all come from the continuous bending, stretching and walki rig around a pallet."
There is also a question of film usage. Stretch and shrink film are expensive, stresses Scholey. "If you wrap a pallet manually you might use 400g of stretch film; if you do it with a machine with power pre-stretch you might use toog. Wrapping by hand isn't adding value—the only thing you're adding is 3oog of film."
Machine-applied film is also going to mean a more consistent wrap, pallet after pallet-and that's what people want, says Scholey.
If waterproofing isn't a concern, it is also possible to secure the items on a pallet by strapping. The cost is similar to film wrapping, and again the range of equipment goes from humble hand-tensioning devices up to fully automatic strappers. "Strapping does add stability and gives you some element of identification—you can put coding on the strapping," says Scholey. But obviously it doesn't provide any weatherproofing. "if you're sending pallets out on the road, you probably wouldn't want to strap them," he adds.
Before you can wrap or strap a pallet, you've got to get the goods on to it in the first place. Often it will he done manually, but this will be labour-intensive in large volumes. Palletising machines suitable for picking up bags or cartons and arranging them on a pallet in predefined patterns are available in two main forms—robotic arm and layer-bed units—and are particularly good for long runs of uniform items. Simple semi-automatic palletisers, says Scholey, might cost L2 0,0 oo: more complex units can cost Doo,000.
Load of rubbish
Anyone dealing with packaging will inevitably generate large quantifies of waste, much of it cardboard and film. So it's wise to be aware of the Packaging Waste Regulations (see panel) which require firms handling waste to take proper responsibility for recycling a percentage of it.
One way to make this easier is by using a baling machine to turn loose cardboard or wrapping film into unit loads of recyclable material that can be sold on.
Paul Brown, southern regional sales manager for Orwak Linley, which manufactures balers and compactors, says anyone spending more than £50 a week on disposing of waste packaging will probably find it worth investing in a simple baler, "There is a huge export market for polythene film, for instance. You can sell dirty stuff for about Do a tonne, while it could cost you £33 a tonne to dispose of it," he says. The material can be cleaned, processed and reproduced as polymer for refuse sacks, damp-proof coursing and even traffic cones.
A simple baler that can process up to a tonne of waste a week might cost £3,500, but you can rent one for about Lao a week. "For that fzo you can bale it and get it collected for no extra charge. What's more, your premises will be tidy, you'll have reduced the fire risk, and you'll have the satisfaction of being green," says Brown.