OILING THE WHEELS
Page 36
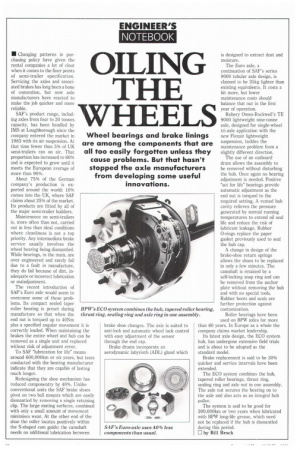
If you've noticed an error in this article please click here to report it so we can fix it.
• Changing patterns in purchasing policy have given the rental companies a lot of clout when it comes to the finer points of semi-trailer specification. Servicing the axles and associated brakes has long been a bone of contention, but now axle manufacturers have reacted to make the job quicker and more reliable.
SAF's product range, including axles from four to 20 tonnes capacity, has been handled by IMS at Loughborough since the company entered the market in 1983 with its air suspension. At that time fewer than 5% of UK semi-trailers ran on air. That proportion has increased to 60% and is expected to grow until it meets the European average of more than 90%.
About 75% of the German company's production is exported around the world: 10% comes into the UK, where SAF claims about 25% of the market. Its products are fitted by all of the major semi-trailer builders.
Maintenance on semi-trailers is, more often than not, carried out in less than ideal conditions where cleanliness is not a top priority. Any intermediate brake service usually involves the wheel bearing being dismantled. While bearings, in the main, are over engineered and rarely fail due to a fault in manufacture, they do fail because of dirt, inadequate or incorrect lubrication or maladjustment.
The recent introduction of SAF's Euro axle would seem to overcome some of these problems. Its compact sealed taper roller bearing is preset during BPW's ECU system combines the hub, tapered roller bearing, manufacture so that when the thrust ring, sealing ring and axle ring in one assembly.
end nut is torqued up to 40Nm plus a specified angular movement it is correctly loaded. When maintaining the brakes the entire wheel and hub can be removed as a single unit and replaced without risk of adjustment error.
To SAF "lubrication for life" means around 600,000km or six years, but tests conducted with the bearing manufacturer indicate that they are capable of lasting much longer.
Redesigning the shoe mechanism has reduced componentry by 40%. Unlike conventional units the SAF brake shoes pivot on two ball mounts which are easily dismantled by removing a single retaining clip. The large mating surfaces, combined with only a small amount of movement minimises wear, At the other end of the shoe the roller locates positively within the S-shaped cam guide: the camshaft needs no additional lubrication between brake shoe changes. The axle is suited to anti-lock and automatic wheel lock control with easy adjustment of the sensor through the end cap.
Brake drums incorporate an aerodynamic labyrinth (ADL) gland which is designed to extract dust and moisture.
The Euro axle, a continuation of SAF's series 9000 tubular axle design, is claimed to be 35kg lighter than existing equivalents. It costs a bit more, but lower maintenance costs should balance that out in the first year of operation.
Rubery Owen-Rockwell's TE 9000 lightweight nine-tonne axle, designed for single-wheel tri-axle application with the new Flexair lightweight suspension, tackles the maintenance problem from a slightly different direction.
The use of an outboard drum allows the assembly to be removed without disturbing the hub. Once again no bearing adjustment is needed. Positive "set for life" bearings provide automatic adjustment as the end nut is torqued to the required setting. A vented hub cavity relieves the pressure generated by normal running temperatures to extend oil seal life and reduce the risk of lubricant leakage. Rubber 0-rings replace the paper gasket previously used to seal the hub cap.
A change in design of the brake-shoe return springs allows the shoes to be replaced in only a few minutes. The camshaft is retained by a self-locking snap ring and can be removed from the anchor plate without removing the hub and with no special tools. Rubber boots and seals are further protection against contamination.
Roller bearings have been used on BPW axles for more than 60 years. In Europe as a whole the company claims market leadership.
Its latest axle design, the ECO system hub, has undergone extensive field trials and is about to be adopted as the standard model.
Brake replacement is said to be 30% quicker and service intervals have been extended.
The ECO system combines the hub. tapered roller bearings, thrust ring, sealing ring and axle nut in one assembly. The axle nut secures the bearing on to the axle and also acts as an integral hub puller.
The system is said to be good for 300,000knn or two years when lubricated with BPW long-life grease, which need not be replaced if the hub is dismantled during this period.
El by Bill Brock