Lorry trends: the shape of things to come
Page 62
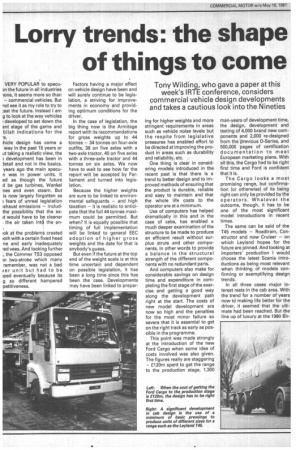
Page 63
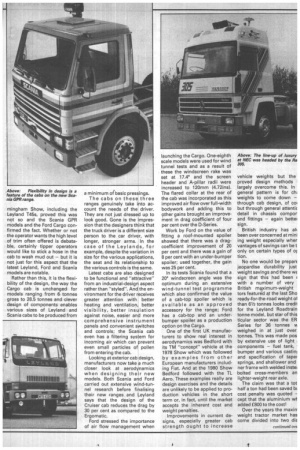
Page 64
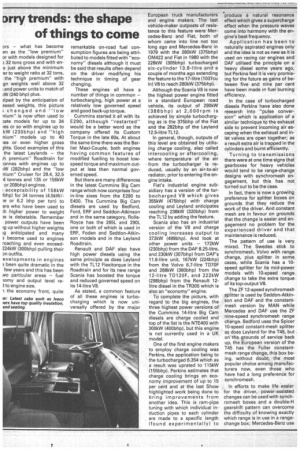
Page 65
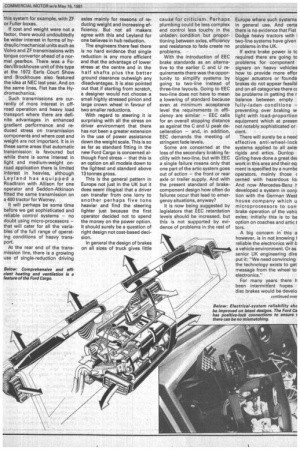
Page 66
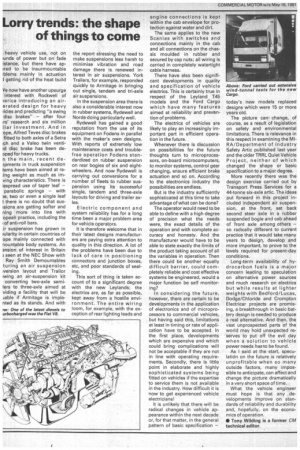
If you've noticed an error in this article please click here to report it so we can fix it.
Tony Wilding, who gave a paper at this week's IRTE conference, considers commercial vehicle design developments and takes a cautious look into the Nineties
VERY POPULAR to specu)n the future in all industries lone, it seems more so than — commercial vehicles. But lot see it as my role to try to )ast the future. Instead I am g to look at the way vehicles developed to set down the ent stage of the game and blish indications for the -e.
,hide design has come a way in the past 15 years or at taking a realistic view, the
development has been in Jetail and not in the basics. years ago the main specun was in power units. It ed as though the future d be gas turbines, Wankel nes and even steam. But is now largely forgotten as ) fears of unreal legislation xhaust emissions — includthe possibility that the ex3t would have to be cleaner the air taken int6 the en
iok at the problems created loth with a certain fixed head ne and early inadequately ,ed vees. And looking further , the Commer TS3 opposed )n two-stroke which many remember, was not a bad ver unit but had to be iped eventually because its g so different hampered petitiveness.
Factors having a major effect on vehicle design have been and will surely continue to be legislation, a striving for improvements in economy and providing optimum conditions for the driver.
In the case of legislation, the big thing now is the Armitage report with its recommendations for gross weights up to 44 tonnes — 34 tonnes on four-axle outfits, 38 on five axles with a two-axle tractor, 40 on five axles with a three-axle tractor and 44 tonnes on six axles. We now have to wait to see how far the report will be accepted by Parliament and turned into legislation.
Because the higher weights are sure to be linked to environmental safeguards — and high taxation — it is realistic to anticipate that the full 44 tonnes maximum could be permitted. But when? It is equally possible that timing of full implementation will be linked to general EEC adoption of higher gross weights and the date for that is anybody's guess.
But even if the future at the top end of the weight scale is at this time uncertain and dependent on possible legislation, it has been a long time since this has been the case. Developments may have been linked to prepar
ing for higher weights and more stringent requirements in areas such as vehicle noise levels but the respite from legislative pressures has enabled effort to be directed at improving the product in areas such as durability and reliability, etc.
One thing is clear in considering models introduced in the recent past is that there is a trend to better design and to improved methods of ensuring that the product is durable, reliable and easy to maintain and that the whole life costs to the operator are at a minimum.
Use of computers has helped dramatically in this and in the case of cabs, has enabled a much deeper examination of the structure to be made to produce an efficient result without surplus struts and other components. In other words to provide a balance in the structural strength of the different components with no redundant parts.
And computers also make for considerable savings on design time and expenditure in completing the first stage of the exercise and getting a good way along the development path right at the start. The costs of new model development are now so high and the penalties for the most minor failure so severe that it is essential to get on the right track as early as possible in the programme.
This point was made strongly at the introduction of the new Ford Cargo when some idea of costs involved was also given. The figures really are staggering — £120m spent to get the range to the production stage, 1,300 man-years of development time, the design, development and testing of 4,000 brand new components and 2,000 re-designed from the previous D-Series, and 500,000 pages of certification documentation to meet European marketing plans. With all this, the Cargo had to be right first time and Ford is confident that it is.
The Cargo looks a most promising range, but confirmation (or otherwise) of its being right can only be provided by the operators. Whatever the outcome, though, it has to be one of the most significant model introductions in recent times.
The same can be said of the T45 models — Roadtrain, Constructor and now Cruiser — on which Leyland hopes for the future are pinned. And looking at importers' production I would choose the latest Scania introductions as being most relevant when thinking of models confirming or exemplifying design trends.
In all three cases major interest rests in the cab area. With the trend for a number of years now to making life better for the driver, it seemed that the ultimate had been reached. But the line up of luxury at the 1980 Bir mingham Show, including the Leyland T45s, proved this was not so and the Scania GPR models and the Ford Cargo confirmed the fact. Whether or not the operator wants the high level of trim often offered is debatable, certainly tipper operators would like to stick a hose in the cab to wash mud out but it is not just for this aspect that the latest Leyland, Ford and Scania models are notable.
Rather than this, it is the flexibility of the design, the way the Cargo cab is unchanged for models ranging from 6 tonnes gross to 28.5 tonnes and clever design of components enables various sizes of Leyland and Scania cabs to be produced from a minimum of basic pressings.
The cabs on these three ranges genuinely take into account the needs of the driver. They are not just dressed up to look good. Gone is the impression that the designers think that the truck driver is a different size person to the car driver, with longer, stronger arms. In the case of the Leylands, for example, despite the variation in size for the various applications, the seat and its relationship to the various controls is the same.
Latest cabs are also designed to be functional and "attractive" from an industrial-design aspect rather than "styled". And the environment for the driver receives greater attention with better heating and ventilation, better visibility, better insulation against noise, easier and more comprehensive instrument panels and convenient switches and controls; the Scania cab even has a filtering system for incoming air which can prevent even small particles of pollen from entering the cab.
Looking at exterior cab design, manufacturers now take a much closer look at aerodynamics when designing their new models. Both Scania and Ford carried out extensive wind-tunnel research before finalising their new ranges and Leyland says that the design of the Cruiser cab reduces the drag by 30 per cent as compared to the Ergornatic.
Ford stressed the importance of air flow management when launching the Cargo. One-eighth scale models were used for wind tunnel tests and as a result of these the windscreen Take was set at 17.4° and the screen header and A-pillar radii were increased to 120mrn (4.72ins). The flared collar at the rear of the cab was incorporated as this improved air flow over full-width bodywork and adding this to other gains brought an improvement in drag coefficient of four per cent over the 0-Series.
Work by Ford on the value of fitting a roof-mounted spoiler showed that there was a dragcoefficient improvement of 20 per cent and there was a gain of 8 per cent with an under-bumper spoiler; used together, the gain was 25 per cent.
In its tests Scania found that a 20° windscreen angle was the optimum during an extensive wind-tunnel test programme which also confirmed the value of a cab-top spoiler which is available as an approved accessory for the range; Ford has a cab-top and an underbumper spoiler as a production option on the Cargo.
One of the first UK manufacturers to show real interest in aerodynamics was Bedford with its TM "concept" vehicle at the 1978 Show which was followed by examples from other European manufacturers including Fiat. And at the 1980 Show Bedford followed with the TL Aero. These examples really are design exercises and the details are unlikely to be applied to production vehicles in the short term or, in fact, until the market accepts the inherent cost and weight penalties.
Improvements in current designs, especially greater cab strength ought to increase vehicle weights but the proved design methods largely overcome this. In general pattern is for chr weights to come down through cab design, of col but through general attentic detail in chassis compor and fittings again better sign.
British industry has al% been over concerned at mini ing weight especially wher vantages of savings can be t only on certain types of of ti on.
No one would be prepare jeopardise durability just weight savings and there wz sign that this had been ( with a number of very British maximum-weight tors featured at the last Sho ready-for-the-road weight ol than 61/2 tonnes looks credii for the Leyland Roadtrain tonne model, but star of this ticular sector was the ER Series for 36 tonnes vs weighed in at just over tonnes. This was made pos by extensive use of light . components fuel tank, bumper and various castinj and specification of taper springs, and shallower and ner frame with welded instei bolted cross-members an lighter-weight rear axle.
The claim was that a tot half a ton had been saved bL cost penalty was quoted cept that the aluminium sArl' added £800 to the cost!
Over the years the maxirr weight tractor market has come divided into two dis
ors — what has become N n as the "low premium" or with models designed for ) 32 tons gross and with ens just above the minimum rer to weight ratio at 32 tons, the "high premium" with gn weights well above 32 ; and power units to match of W(240 bhp) plus.
?.Iped by the anticipation of aased weights, this picture ; changed and "low nium" is now often used to 7,ate models for up to 34 les or so with engines up to kW (230bhp) and "high nium" models up to 40 ins or even higher gross jilts. Good examples of this the latest Leylands — the lh premium" Roadtrain for :onnes with engines up to (282bhp) and the "low nium" Cruiser for 28.4, 32.5 4 tonnes and 135 or 156kW or 209bhp) engines.
acceptability of 156kW bhp) for 34 tonnes (4.5kW/le or 6.2 bhp per ton) to ers who have been used to ;I) higher power to weight )s is debatable. Remember power outputs have been ig up without higher weights ig anticipated and many D become used to engines reaching and even exceed224kW (300bhp) pulling their on outfits.
evelopments in engines been quite dramatic in the few years and this has been No particular areas — fuel lomy and output level reto engine size.
the economy front, quite remarkable on-road fuel consumption figures are being attributed to models fitted with "economy" diesels although it must be said that results often depend on the driver modifying his technique in timing of gear changing.
These engines all have a number of things in common — turbocharging, high power at a relatively low governed speed and good back-up torque.
Cummins started it all with its E290, although "restarted" would be a better word as the company offered its Custom Torque in the late 60s. At about the same time there was the BerHet Maxi-Couple, both engines having common features of modified fuelling to boost lowspeed torque and maximum output at less than normal governed speed.
But there are many differences in the latest Cummins Big Cam range which now comprises four in-line sixes from the E290 to E400. The Cummins Big Cam diesels are used by Bedford, Ford, ERF and Seddon-Atkinson and in the same category, RollsRoyce has the 265L and 290L one or both of which is used in ERE, Foden and Seddon-Atkinson models and in the Leyland Roadtrain.
Renault and DAF also have high power diesels using the same principle as does Leyland with the TL12 Flexitorque in the Roadtrain and for its new range Scania has boosted the torque and reduced governed speed on its 14-litre V8.
As stated, a common feature of all these engines is turbocharging which is now universally offered by the major European truck manufacturers and engine makers. The last vehicle-maker outposts of resistance to this feature were Mercedes-Benz and Fiat, both of whom came into line not too long ago and Mercedes-Benz in 1979 with the 280kW (375bhp) 0M422 and Fiat in 1980 with the 228kW (305bhp) turbocharged six-cylinder 13.8-litre and a couple of months ago extending the feature to the 17-litre (10370u in) V8 to reach 280kW (375bhp).
Although the Scania V8 is now the highest power engine fitted in a standard European road vehicle, its output of 290kW (388 bhp) at 2,000rpm is achieved by simple turbocharging as is the 375bhp of the Fiat and the 282bhp of the Leyland 12.5-litre TL12.
In general, though, outputs of this level are obtained by utilising charge cooling, also called intercooling or aftercooling, where temperature of the air from the turbocharger is reduced, usually by an air-to-air radiator, prior to entering the engine intake.
Fiatrs industrial engine subsidiary has a version of the turbocharged V8 which gives 355kW (475bhp) with charge cooling and Leyland anticipates reaching 238kW (320bhp) from the TL12 by adding the feature.
Scania also has an industrial version of the V8 and charge cooling increases output to 372kW (499bhp). And look at other power units — 172kW (230bhp) from the DAF 8.25-litre, and 230kW (307bhp) from DAF's 11.6-litre unit, 167kW (224bhp) from the Volvo 6.7-litre TD7OF and 268kW (360bhp) from the 12-litre TD120F, and 222kW (298bhp) from the Renault 12litre diesel in the TR305 which is also an "economy" engine.
To complete the picture, with regard to the big engines, the three highest power versions of the Cummins 14-litre Big Cam diesels are charge cooled and top of the list is the NTE400 with 300kW (400bhp), but this engine is not currently used in a UK model.
One of the first engine makers to employ charge cooling was Perkins, the application being to the turbocharged 6.354 which as a result was uprated to 115kW (155bhp). Perkins estimates that charge cooling brings an economy improvement of up to 15 per cent and at the last Show highlighted work being done to bring improvements from another idea. This is ram-pipe tuning with which individual induction pipes to each cylinder are made to a specific length (found experimentally) to produce a natural resonance effect which gives a supercharge effect when the pressure waves come into harmony with the engine's beat frequency.
Application has been to naturally aspirated engines only and the idea is not as new as it is used on racing car engines and DAF utilised the principle on a heavy diesel some years ago, but Perkins feel it is very promising for the future as gains of between five and nine per cent have been made in fuel burning efficiency.
In the case of turbocharged diesels Perkins have also done research into "pulse conversion" which is application of a similar technique to the exhaust side to prevent incoming air escaping when the exhaust and inlet valves are open together; as a result extra air is trapped in the cylinders and burnt efficiently.
Turning to transmissions there were at one time signs that gearboxes for heavy vehicles would tend to be range-change designs with synchromesh engagement, but this has not turned out to be the case.
In fact, there is now a growing preference for splitter boxes on grounds that they reduce the work of the driver. And constant mesh are in favour on grounds that the change is easier and engagement no problem for the experienced driver and that maintenance is reduced.
The pattern of use is very mixed. The Swedes stick to synchromesh, Volvo with range change, plus splitter in some cases, while Scania has a 10speed splitter for its mid-power models with 10-speed range change to take the extra torque of its top-output V8.
The ZF 12-speed synchromesh splitter is used by Seddon-Atkinson and DAF and the constantmesh version by MAN while Mercedes and DAF use the ZF nine-speed synchromesh range change. Bedford uses the Spicer 10-speed constant-mesh splitter as does Leyland for the T45, but on the grounds of service back up, the European version of the T45 has the Fuller constantmesh range change, this box being, without doubt, the most popular choice among manufacturers now, even those who have had a long preference for synchromesh.
In efforts to make life easier for the driver, power-assisted changes can be used with synchromesh boxes and a double-H gearshift pattern can overcome the difficulty of knowing exactly which range is in use in a rangechange box; Mercedes-Benz use this system for example, with ZF or Fuller boxes.
If cost and weight were not a factor, there would undoubtedly be wider interest in forms of hydraulic/mechanical units such as Volvo and ZF transmissions with torque convertor ahead of a normal gearbox. There was a Foden/Brockhouse unit of this type at the 1972 Earls Court Show and Brockhouse also featured the idea at NEC last year. And on the same lines, Fiat has the Hydromechanica.
Such transmissions are currently of more interest in offroad operation and heavy load transport where there are definite advantages in enhanced gradient performance and reduced stress on transmission components and where cost and weight are not important. It is in these same areas that automatic transmission is favoured but while there is some interest in light and medium-weight onroad application there is limited interest in heavies, although Leyland has equipped a Roadtrain with Allison for one operator and Seddon-Atkinson fitted the same transmission on a 400 tractor for Watney.
It will perhaps be some time before we get sophisticated and reliable control systems — no doubt using micro-processors — that will cater for all the variables of the full range of operating conditions of heavy transport.
At the rear end of the transmission line, there is a growing use of single-reduction driving axles mainly for reasons of reducing weight and increasing efficiency. But not all makers agree with this and Leyland for one believes in hub reduction.
The engineers there feel there is no hard evidence that single reduction is any more efficient and that the advantage of lower stress at the centre and in the half shafts plus the better ground clearance outweigh any disadvantages. It is also pointed out that if starting from scratch, a designer would not choose a small highly stressed pinion and large crown wheel in favour of two smaller reductions.
With regard to steering it is surprising with all the stress on driver environment that there has not been a greater extension in the use of power assistance down the weight scale. This is so as far as standard fitting in the new Ford Cargo is concerned although Ford stress — that this is an option on all models down to the lightest and standard above 13 tonnes gross.
This is the general pattern in Europe not just in the UK but it does seem illogical that a driver can transfer from one lorry to another perhaps five tons heavier and find the steering lighter just because the first operator decided not to spend the money on the power option. It should surely be a question of right design not cost-based decision.
In general the design of brakes on all sizes of truck gives little cause for criticism. Perhaps plumbing could be less complex and control less touchy in the unladen condition but proportioning between axles, efficiency and resistance to fade create no problems. • With the introduction of EEC brake standards as an alternative to the earlier C and U requirements there was the opportunity to simplify systems by going to two-line instead of three-line layouts. Going to EEC two-line does not have to mean a lowering of standard because even at minimum acceptance level the requirements in efficiency are similar — EEC calls for an overall stopping distance as against the C and U peak decelleration — and, in addition, EEC demands the meeting of stringent fade levels.
Some are concerned at the loss of the secondary braking facility with two-line, but with EEC a single failure means only that one part of the artic system goes out of action — the front or rear axle or trailer supply. And with the present standard of brakecomponent design how often do failures occur that lead to emergency situations, anyway?
It is now being suggested by legislators that EEC retardation levels should be increased, but this is not supported by evidence of problems in The rest of Europe where such systems in general use. And certa there is no evidence that Fiat Dodge heavy tractors with I two-line systems have given problems in the UK.
If extra brake power is to required there are going to problems for component signers on heavy vehicles how to provide more effor bigger actuators or founda brakes do not appear feasibl and on all categories there cc be problems in getting the r .balance between empty fully-laden• conditions — preventing over braking w light with load-proportion equipment which at presen not notably sophisticated or cient.
There will surely be a need effective anti-wheel-lock systems applied to all axle rigids and artics. Dunlop Girling have done a great de work in this area and their egi ment is specified by a numbE operators, mainly those cerned with hazardous lot And now Mercedes-Benz tdeveloped a system in conji tion with the German West house company which u microprocessors to con 'brake operation of the vehic exles; initially this is to be option on coaches and artic t tors.
A big concern in this a however, is in not knowing reliable the electronics will b a vehicle environment. Or as senior UK engineering dire -put it: "We need convincing the technology exists to get
m message from the wheel to electronics."
For many years there h been intermittent hopes disc brakes would be develo heavy vehicle use, not on lunds of power but on fade istance, but there have apffed to be insurmountable ■ blems mainly in actuation getting rid of the heat build
Ve now have another upsurge interest with Rockwell of lerica introducing an airerated design for heavy licles and predicting "a swing disc brakes" — after four Irs' research and six million liar investment. And in °per Alfred Teves disc brakes fitted to both axles of a Setra ich and a Valeo twin ventiTI disc brake has been dewed for heavy trucks.
n the main, recent de)pments in truck suspension terns have been aimed at re:ing weight as much as imving characteristics. There is lespread use of taper leaf — parabolic springs — with .1e, two or even a single leaf I there is no doubt that susisions are getting softer and ning more into line with opean practice, including the of anti-roll bars.
,ir suspension has grown in rularity in certain countries of ope mainly connected with n ountable body systems. An nsion of interest in Britain seen at the NEC Show with Ray ,Smith Demountables turing an air suspension version layout and Trailor wing an air-suspension kit converting two-axle semilers to three-axle aimed at viding a facility that will be J able if Armitage is implented as its stands. And with the report stressing the need to make suspensions less harsh to minimise vibration and road damage there is renewed interest in air suspensions. York Trailers, for example, responded quickly to Armitage in bringing out single, tandem and tri-axle air suspensions.
In the suspension area there is also a considerable interest now in rubber systems, Rydewell and Norde doing particularly well.
Rydewell has gained a good reputation from the use of its equipment on Fodens in parallel with the maker's own designs. With reports of extremely low maintenance costs and troublefree operation Fodens standardized on rubber suspension on rear bogies of six and eightwheelers. And now Rydewell is carrying out conversions for a number of fleets to rubber suspension using its successful single, tandem and three-axle layouts for driving and trailer axles.
Electric component and system reliability has for a long time been a major problem area for vehicle operators, It is therefore welcome that in their latest designs manufacturers are paying extra attention to quality in this direction, A lot of the problems have been due to lack of care in positioning connectors and junction boxes, etc, and poor standards of sealing.
This sort of thing is taken account of to a significant degree with the new Leylands; the electrics are, as far as possible, kept away from a hostile environ ment. The entire wiring loom, for example, with the exception of rear lighting leads and engine connections is kept within the cab envelope for protection against water and dirt.
The same applies to the new Scanias with switches and connections mainly in the cab and all connections on the chassis moulded in rubber and secured by cap nuts; all wiring is carried in completely watertight cable harness.
There have also been significant developments in quality and specification of vehicle electrics. This is certainly true in respect of the Leyland T45 models and the Ford Cargo which have many features aimed at reliability and prevention of problems.
The electrics of vehicles are likely to play an increasingly important part in efficient operation in the future.
Whenever there is discussion on possibilities for the future thoughts turn to microprocessors, on-board microcomputers, to monitor systems, control gear changing, ensure efficient brake actuation and so on. According to the electronics industry the possibilities are endless.
But is the industry sufficiently sophisticated at this time to take advantage of what can be done?
The operator would need to be able to define with a high degree of precision what the needs were, the exact details of the operation and with complete accuracy and honesty. And the manufacturer would have to be able to state exactly the limits of the product taking account of all the variables in operation. Then there could be another equally difficult barrier, could completely reliable and cost effective systems be engineered, would a major function be self monitoring?
In considering the future, however, there are certain to be developments in the application of electronics and of microprocessors to commercial vehicles, but having said this, limitations at least in timing or rate of application have to be accepted. In the first place, developments which are expensive and which could bring complications will not be acceptable if they are not in line with operating requirements. Secondly, there is little point in elaborate and highly sophisticated systems being fitted on vehicles if the expertise to service them is not available in the industry. How difficult it is now to get experienced vehicle electricians!
It is unlikely that there will be radical changes in vehicle ap pearance within the next decade or, for that matter, in the general pattern of basic specification — today's new models replaced designs which were 15 or more years old.
The picture can change, of course, as a result of legislation on safety and environmental limitations. There is relevance in this respect in examining the MIRA/ Depa rtment of Industry Safety Artie published last year and the older TRRL Quiet Vehicle Project, neither of which changed the shape or basic specification to a major degree.
More recently there was the design exercise carried out by Transport Press Services for a 44-tonne six-axle artic. The ideas put forward in this project included independent air suspension, at the front, set back second steer axle in a rubber suspended bogie and cab ahead of front axle among others — so radically different to current practice that it would take many years to design, develop and more important, to prove to the levels required for present-day conditions.
Long-term availability of hydrocarbon fuels is a major concern leading to speculation on alternative power sources and much research on electrics but while results at lighter weights with Bedford/Lucas, Dodge/Chloride and Crompton Electricar projects are promising, a breakthrough in basic battery design is needed to produce a real alternative. And then, the vast unprospected parts of the world may hold unexpected reserves to put off the evil day when a solution to vehicle power needs has to be found.
As I said at the start, speculation on the future is relatively unprofitable when so many outside factors, many impossible to anticipate, can affect and change the picture dramatically in a very short space of time.
What the vehicle engineer must hope is that any developments improve on standards of reliability and durability and, hopefully, on the economics of operation.
• Tony Wilding is a former CM technical editor.