THOROUGH MAINTENAN1 ;CHEME FOR CHEMICALS FLEET
Page 50

Page 51
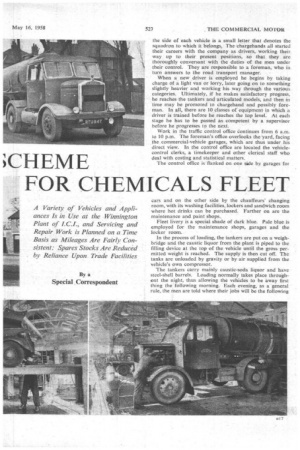
Page 52
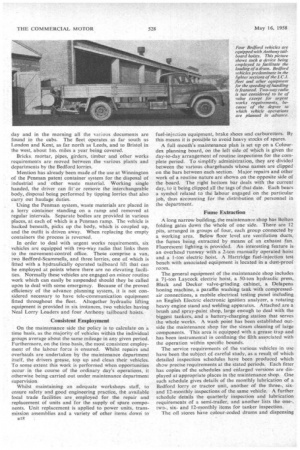
Page 55
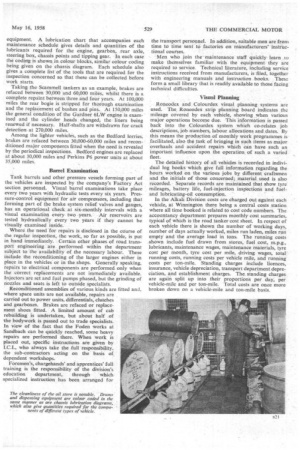
If you've noticed an error in this article please click here to report it so we can fix it.
A Variety of Vehicles and Appliances Is in Use at the -Witmington Plant of I.C.I., and Servicing and Repair Work is Planned on a Time Basis as Mileages Are Fairly Consistent: Spares Stocks Are Reduced by Reliance Upon Trade Facilities
By a
Special Correspondent
ADVANCED ideas in fleet control, including a " squadron " system and the use of two-way radio, are practised at the Winnington plant of Imperial Chemical Industries, Ltd., at Northwich, Cheshire. The Alkali Division headquarters are situated there and, apart from the tankers, a varied fleet is employed to deal with ancillary duties. These include inter-plant traffic, canteen and other works services, waste-material disposal, fire prevention, road sweeping and ambulance facilities.
The tanker fleet at Winnington numbers 28, the largest units being four Foden articulated eight-wheelers of 22 tons gross, having tanks of about 1,600-gal. capacity. These vessels are designed to carry caustic liquor. There are 19 Scarnmells of similar design but of about 2,000-gal. capacity, plus six rigid Fodens, three of which are 12-ton fourwheelers and three 19-ton six-wheelers.
Tractors and Semi-trailers What may be described as the works fleet consists principally of 24 Bedford lorries dnd three vans. Of the Bedfords, 12 are tippers equipped for employment with Penman containers, the remainder comprising five tippers and seven platform-bodied vehicles. This section of the fleet includes also 10 Bedford-Scammell tractive units and . a-Scarnmell Scarab, employed in conjunction with 51 semitrailers of 6-8-ton capacity. Four of the semi-trailers are large vans to carry empty packages, four are tankers for internal use, 12 are tippers mainly for refuse, four are 20-ft. semi-trailers, and 13 are low-loaders. The remainder are platform. types of ordinary deck height and varying lengths. One semi-trailer is specially designed to take works tools from the plants into the maintenance section.
Th-ree light vans are employed to carry such items as canteen meals from the central kitchen to the smaller dining rooms arid to distribute small articles requiring protection from the weather or other special treatment. Miscellaneous vehicles include two Victor electric tractors, Austin and Daimler ambulances, a Bedford fire-engine, a Lewin road sweeper, a Foden low-loader and three Land-Rover' fire patrol vehicles. Many other items of mobile equipment are employed, such as fork-lift trucks, cranes and bulldozers, these again being under departmental control.
The fleet operated by the transport department is divided into four sections known as' squadrons. A mobile chargehand is in control of each squadron. Painted in white on
B16 .
the side of each vehicle is a small letter that denotes the squadron to which it belongs, The chargehands all started their careers with the company as drivers, working their way up to their present positions, so that they , are thoroughly conversant with the duties of the men under their control. They are responsible to a foreman, who in turn answers to the road transport manager.
When a new driver is employed he begins by taking charge of a light van or lorry, later going on to something slightly heavier and working his way through the various categories. Ultimately, if he makes satisfactory progress, he reaches the tankers and articulated models, and then in time may he promoted to chargehand and possibly foreman. In all, there are 10 classes of equipment in which a driver is trained before he reaches the top level. At each stage he has to be passed as competent by a supervisor before he progresses to the next.
Work in the traffic control office Continues from 6 a.m. to 10 p.m. The foreman's office overlooks the yard, facing the commercial-vehicle garages, which are thus under his direct view. In the control office are located the vehiclecontrol clerks, a timekeeper and other clerical staff who deal with costing and statistical matters.
The control office is flanked on one side by garages for cars and on the other side by the chauffeurs' changing room, with its washing facilities, lockers and sandwich room where hot drinks can be purchased. Farther on are the maintenance and paint shops.
Fleet livery is a special shade of dark blue. Pale blue is employed for the maintenance shops, garages and the locker room.
In the process of loading, the tankers are put on a weighbridge and the caustic liquor from the plant is piped to the filling device at the top of the vehicle until the gross permitted weight is reached. The supply is then cut off. The tanks are unloaded by gravity or by air supplied from the vehicle's own compressor.
The tankers carry mainly caustic-soda liquor and have steel-shell barrels. Loading normally takes place throughout the night, thus allowing the vehicles to be away first thing the following morning. Each evening, as a general rule, the men are told where their jobs will be the following day and in the morning all the various documents are found in the cabs. The fleet operates as far south as London and Kent, as far north as Leeds, and to Bristol in the west, about lm. miles a year being covered.
Bricks, mortar, pipes, girders, timber and other works requirements are moved between the various plants and departments by the Bedford lorries.
Mention has already been made of the use at Winnington of the Penman patent container system for the disposal of industrial and other waste material. Working single handed, the driver can fit'or remove the interchangeable body, disposal being performed by tipping lorries that also carry out haulage duties.
Using the Penman system, waste materials are placed in a lorry container standing on a ramp and removed at regular intervals. Separate bodies are provided in various places, at each of which is a Penman ramp. The vehicle is backed beneath, picks up the body, which is coupled up, and the outfit is driven away. When replacing the empty containers the process is reversed.
In order to deal with urgent works requirements, six vehicles are equipped with two-way radio that links them to the movement-control office. These comprise a van, two Bedford-Scammells, and three lorries, one of which is fitted with a hydraulically operated tailboard lift that can be employed at points where there are no elevating facilities. Normally these vehicles are engaged on minor routine work which can easily be suspended should they be called upon to deal with some emergency. Because of the proved efficiency of the advance planning system, it is not considered necessary to have tele-communication equipment fitted throughout the fleet. Altogether hydraulic lifting equipment is provided in six instances, two vehicles having Neal Lorry Loaders and four Anthony tailboard hoists.
Consistent Employment
On the maintenance side the policy is to calculate on a time basis, as the majority of vehicles within the individual groups average about the same mileage in any given period. Furthermore, on the time basis, the most consistent employment of the labour force is ensured. Whilst repairs and overhauls are undertaken by the maintenance department itself, the drivers grease, top up and clean their vehicles. To some extent this work is performed when opportunities occur. in the course of the ordinary day's operations, it otherwise being carried out under maintenance department supervision.
Whilst maintaining an adequate workshops staff, to ensure safety and good engineering practice, the available local trade facilities are employed for the repair and replacement of units and for the supply of spare components. Unit replacement is applied to power units, transmission assemblies and a variety of other items down to al fuel-injection equipment, brake shoes and carburetters. By this means it is possible to avoid heavy stocks of spares.
A full month's maintenance plan is set up on a Colourdes planning board, on the left side of which is given the day-to-day arrangement of routine inspections for the complete period. To simplify administration, they are divided between the various chargehands whose names are clipped on the bars between each section. Major repairs and Other work of a routine nature are shown on the opposite side of the board. The right bottom bar deals with the current day, to it being clipped all the tags of that date. Each bears a symbol related to the labour engaged on the particular job, thus accounting for the distribution of personnel in the department.
Fume Extraction A long narrow building, the maintenance shop has Bolton folding gates down the whole of one side. There are 12 pits, arranged in groups of four, each group connected by a working area. Below floor level are ventilation ducts, the fumes being extracted by means of an exhaust fan. Fluorescent lighting is provided. An interesting feature is an overhead -runway with a 2-ton manually operated hoist and a 1-tonelectric hoist. A Hartridge fuel-injection test bench with associated equipment is located in a dust-proof room.
The general equipment of the maintenanoe shop includes a 7+-ton Laycock electric hoist, a 50-ton hydraulic press. Black and Decker valve-grinding cabinet, a Delapena honing machine, a paraffin washing tank with compressedair connections, a mobile electrical testing panel including an English Electric electronic ignition analyzer, a rotating heavy engine stand and welding apparatus. Attached are a brush and spray-paint shop, large enough to deal with the biggest tankers, and a battery-charging station that serves the whole works. A wash point has been established outside the maintenance shop for the steam cleaning of large components. This area is equipped with a grease trap and has been instrumental in confining the filth associated with the operation within specific bounds.
The service requirements of the various vehicles in use have been the subject of careful study, as a result of which detailed inspection schedules have been produced which show precise requirements at the stated periods. Each fitter has copies of the schedules and enlarged versions are displayed at appropriate places in the maintenance shop. One such schedule gives details of the monthly lubrication of a Bedford lorry or tractor unit, another of the three-, sixand 12-monthly inspections of the same vehicle. A further schedule details the quarterly inspection and lubrication requirements of a semi-trailer, and another lists the one-, two-, sixand 12-monthly items for tanker inspection.
The oil stores have colour-coded drums and dispensing equipment, A lubrication chart that accompanies each maintenance schedule gives details and quantities of the lubricants required for the engine, gearbox, rear axle, steering box, chassis points and tipping gear. In each case the coditrg is showtkin colour blocks, similar colour coding being given on the chassis diagram. Each schedule also gives a complete list of the tools that are required for the inspection concerned so that these can be collected before work starts, Taking the Scammell tankers as an example, brakes are refaced between 30;000 and 60000 miles, whilst there is a complete repaint between three and four years. At 100,000 miles the rear bogie is stripped for thorough examination and the replacement of bushes and pins. At 150,000 miles the general condition of the Gardner 6LW engine is exam ined and the cylinder heads changed, the liners being renewed if necessary. Half-shafts are withdrawn for crack detection at 270,000 miles.
Among the lighter vehicles, such as the Bedford lorries, brakes are refaced between 30,000-60,000 miles and reconditioned major components fitted when the need is revealed by the periodical inspections. Bedford engines are replaced at about 30,000 miles and Perkins P6 power units at about 35,000 miles,
Barrel Examination
Tank barrels and other pressure vessels forming part of the vehicles are inspected by the company's Factory Act section personnel. Visual barrel examinations take place every two years with hydraulic tests every six years. Pres sure-control equipment for air compressors, including that forming part of the brake system relief valves and gauges, has an operational check at six-monthly intervals with a visual examination every two • years. Air reservoirs are tested hydraulically every two years if they cannot be visually examined inside.
Where the need for repairs is disclosed in the course of the regular inspection, the work, so far as possible, is put in hand immediately. Certain other phases of road transport engineering are performed within the department subject to the availability of the necessary labour. These include the reconditioning of the larger engines either in place in the vehicles or in the shops. Generally speaking, repairs to electrical components are performed only when the correct replacements are not immediately available. Injectors arc set and fuel pumps phased, but the grinding of nozzles and seats is left to outside specialists.
Reconditioned assemblies of various kinds are fitted and. where spare units are not available, repairs are carried out to power units, differentials, clutches and gearboxes. Brakes are refaced or replacement shoes fitted. A limited amount of cab rebuilding is undertaken, but about half of the bodywork is passed out to trade specialists. In view of the fact that the Foden works at Sandbach can be quickly reached, some heavy repairs are performed there. When work is placed out, specific instructions are given by I.C.I., who always take the full responsibility. the sub-contractors acting on the basis of dependent workshops.
Foremen's, chargehands' and apprentices' full training is the responsibility of the division's education department, through which specialized instruction has been arranged for the transport personnel. In addition, suitable men are from time to time sent to factories on manufacturers' instructional courses.
Men who join the maintenance staff quickly learn to make themselves familiar with the equipment they are required to service. Technical literature, including service instructions received from manufacturers, is filed, together with engineering manuals and instruction books. These form a small library that is readily available to those facing technical difficulties.
Visual Planning Roneociex and Colourdex visual planning systems are used. The. Roneodex strip planning board indicates the mileage covered by each vehicle, showing when various major operations become due. This information is passed back into the Colourdex system which co-relates job descriptions, job numbers, labour allocations and dates. By this means the production of monthly work programmes is• facilitated, also the task of bringing in such items as major overhauls and accident repairs which can have such an important influence upon the operation of such a varied fleet.
The detailed history of all vehicles is recorded in individual log books which give full information regarding the hours worked on the various jobs by different craftsmen and the initials of those concerned; material used is also recorded. Separate records are maintained that show tyre mileages, battery life, fuel-injection inspections and fueland lubricating-oil consumption.
In the Alkali Division costs are charged out against each vehicle, at Winnington there being a central costs station where all time booked is related to cost code numbers. The accountancy department prepares monthly cost summaries, typical of which is the road tanker cost sheet. In respect of each vehicle there is shown the number of working days, number of days actually worked, miles run laden, miles run empty and the average load in tons. The running costs shown include fuel drawn from stores, fuel cost, m.p.g., lubricants, maintenance wages, maintenance materials, tyre cost per month, tyre cost per mile, driving wages, total running costs, running costs per vehicle mile, and running costs per ton-rnile. Standing charges include licences, insurance, vehicle depreciation, transport department depreciation, and establishment charges. The standing charges are again split up into their proportions per day, per vehicle-mile and per ton-mile. Total costs are once more broken down on a vehicle-mile and ton-mile basis.