Saving £100 Per Bus-Year
Page 46
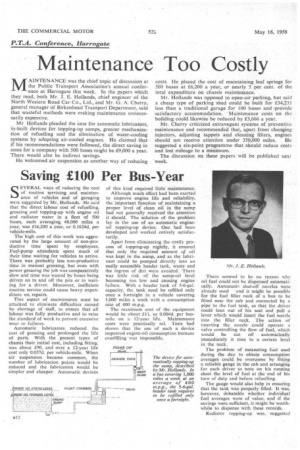
Page 47
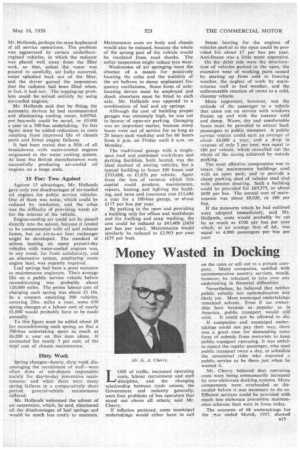
If you've noticed an error in this article please click here to report it so we can fix it.
SEVERAL ways of reducing the cost of routine servicing and maintenance of vehicles and of garaging were suggested by Mr. Hollands. He said that the direct labour cost of refuelling, greasing and topping-up with engine oil and radiator water in a fleet of 500 buses, each averaging, 48,000 miles a year, was £16,240 a year, or 0.1624d. per vehicle-mile.
The'high cost of this work was aggravated by the large amount of non-productive time *spent by employees. Fuel-pump attendants spent much of their time waiting for vehicles to arrive. There was probably less non-productive time in manual greasing, but even with power greasing the job was comparatively slow and time was wasted by buses being driven on to and off the pits or in waiting for a driver. Moreover, inefficient routine service could cause heavy expenditure on, repairs.
This aspect of maintenance must be attacked to eliminate difficulties caused by shortage of staff, to ensure that all labour was fully productive and to raise the standard of work to prevent excessive wear or failures.
Automatic lubricators reduced the cost of greasing and prolonged the life of parts. With the present types of chassis their initial cost, including fitting, was about DO, and over a 12-year life cost only 0.037d. per vehicle-mile. When air suspension became common, the number of lubrication points would be reduced and the lubricators would be simpler and cheaper. Automatic devices of this kind required little maintenance.
Although much effort had been exerted to improve engine life and reliability, the important function of maintaining a proper level of clean oil in the sump had not generally received the attention it should. The solution of the problem lay in the use of an automatic engineoil topping-up device. One had been developed and worked entirely satisfactorily.
Apart from eliminating the costly process of topping-up nightly, it ensured that only the required amount of oil was kept in the sump, and as the lubricant could be pumped directly into an easily accessible header tank, waste and the ingress of dirt were avoided. There was little risk of the sump-oil level becoming too low and causing engine failure. With a header tank of 5-6-gal. capacity, the tank need be refilled only once a fortnight in a vehicle covering 1,000 miles a week with a consumption rate of 400 m.p.g.
The maximum cost of the equipment would be about £11, or 0.004d. per busmile on a 12-year life. Maintenance costs were practically nil. Tests had shown that the use of such a device improved engine-oil consumption because overfilling was impossible. There seemed to be no reason why oil fuel could not be dispensed automatically. Automatic shut-off nozzles were already used and it might be possible for the fuel filler neck of a bus to be fitted near the cab and connected by a pipe to the fuel tank, so that the driver could lean out of his seat and pull a lever which would insert the fuel nozzle into the filler neck. The action of inserting the nozzle could operate a valve controlling the flow of fuel, which would be cut off automatically immediately it rose to a certain level in the neck.
The problem of measuring fuel used during the day to obtain consumption averages could be overcome by fitting a reliable gauge in the cab and arranging for each driver to note on his running sheet the level of fuel at the end of his turn of duty and before refuelling.
The gauge would also help in ensuring that the tank was properly filled. It was, however, debatable whether individual fuel averages were of value, and if the savings were sufficient, it might be worthwhile to dispense with these records.
Radiator topping-up was, suggested Mr. Hollands, perhaps the most haphazard of all service operations. The problem was aggravated by certain underfloorcngined vehicles, in which the radiator was placed well away from the filler neck, so that, unless the water was poured in carefully, air locks occurred, water splashed back out of the filler, and the driver gained the impression that the radiator had been filled when, in fact, it had not. The topping-up problem could be solved entirely by using air-cooled engines.
Mr. Hollands said that by fitting the automatic devices he had recommended and eliminating cooling water, 0.0974d. per bus-mile could be saved, or £9,000 a year in a 500-bus undertaking. To this figure must be added reductions in costs resulting from improved life of chassis parts and fewer engine failures.
It had been stated that a fifth of all breakdowns with• water-cooled engines originated in the• water cooling system. At least five British manufacturers were successfully producing air-cooled oil engines on a large. scale.
15. For: Two Against
• Against 15 advantages, Mr. Hollands gave only two disadvantages of air-cooled oil engines for public service vehicles. One of them was noise, which could be reduced by insulation, and the other was the difficulty of providing warm air for the interior of the vehiele.
Engine-cooling air could not be passed directly into the saloon, because it tended to be contaminated with oil and exhaust fumes, but an air-to-air heat exchanger might be developed. The -standard of saloon heating on many present-day vehicles with water-cooled engines was, in any event, far from satisfactory, and an alternative system, employing waste engine heat, was urgently required.
Leaf springs had been a great nuisance to maintenance engineers. Their average life on a public service vehicle before reconditioning was probably about 120,000 miles. The prime labour cost of changing each spring was about El 10s. In a concern operating 500 vehicles, covering 20m. miles a year, some 650 spring changes at a labour cost of nearly £1,000 would probably have to be made annually.
To this figure must be added about £8 for reconditioning each spring, so that a 500-bus undertaking spent as much as £6,200 a year on this item alone. It accounted for nearly 5 per cent, of the total cost of chassis maintenance,
Dirty Work
Spring changes—heavy, dirty work discouraging the recruitment of staff—were often done at sub-depots responsible mainly for day-to-day preventive maintenance, and when there were many spring failures in a comparatively short period, general-vehicle maintenance suffered.
Mr. Hollands welcomed the advent of air suspension, which, he said, eliminated all the disadvantages of leaf springs and would be much less costly to maintain. Maintenance costs on body and chassis would also be reduced, because the whole of the sprung part of the vehicle would be insulated from road shocks. The softer suspension might reduce tyre wear.
Weaknesses of air springing were the absence of a means for positively locating the axles and the inability of the air bellows to damp unpleasant frequency oscillations., Some form of axlelocating device must be employed and shock absorbers must be fitted to each axle. Mr. Hollands was opposed to a combination of leaf and air springs.
Although the cost of building proper garages was extremely high, he was not in favour of open-air parking. Garaging was an important matter, because many buses Were out of service for as long as 20 hours each weekday and for 60 hours from 6 p.m. on Friday until 6 a.m. on Monday.
The traditional garage with a singlespan roof and combined workshops and parking facilities, both heated, was the ideal method of storing vehicles, but a typical building to house 100 buses cost £103,608, or. £1,036 per vehicle. Apart from the loss of revenue which this .capital could produce, maintenance, repairs, heating and lighting the building, and rates and insurance cost £11,686 a year for a 100-bus garage, or about £117 per bus per year.
By parking in the open and providing a building only for offices and workshops and for fuelling and soap washing, the cost could be reduced to £43,400 (£434 per bus per year). Maintenance would similarly be reduced to £3,903 per year (£39 per bus). Steam heating for the engines of vehicles parked in the open could be provided for about £7 per bus per year. Anti-freeze was a little more expensive.
On the debit side were the deterioration of vehicles parked in the open, the excessive wear of working parts caused by starting up from cold in freezing weather, the neglect of work by maintenance staff in bad weather, and the unfavourable reaction of crews to a cold, clammy vehicle.
More important, however, was the attitude of the passenger to a vehicle that came out on service with windows frozen up and with the interior cold and damp. Warm, dry and comfortable buses must be provided to attract back passengers to public transport. A public service vehicle could earn an average of about £4,000 a year, and a . drop in revenue of only 2 per 'cent. was equal to £80 per vehicle, which cancelled out the whole of the saving achieved by outside parking.
The most effective compromise was to retain the maintenance buildings used with an open park, and to provide a cheap parking shed of tubular steel clad with asbestos sheeting. Such a building could be providedfor £69,373, or about £690 per bus. The annual cost of maintenance was about £8,020, or £80 per bus.
If the measures which he had outlined were adopted immediately, said Mr. Ffollands, costs would probably be cut by as much as £100 per bus per year which, at an average fare of 6d., was equal to 4,000 passengers per bus per year.