CHIPS WITH VERYTHING
Page 39
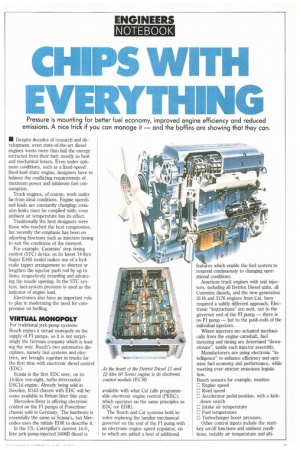
Page 40
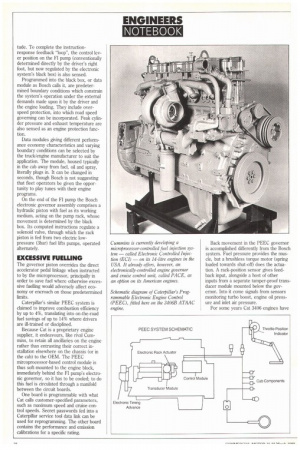
Page 41
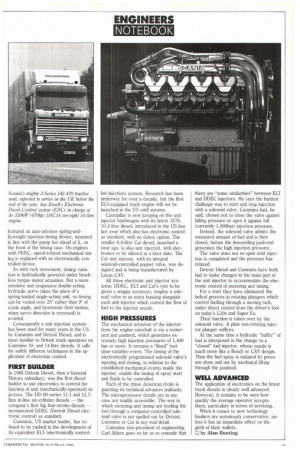
If you've noticed an error in this article please click here to report it so we can fix it.
Pressure is mounting for better fuel economy, improved engine efficiency and reduced emissions. A nice trick if you can manage it — and the boffins are showing that they can.
• Despite decades of research and development, even state-of-the-art diesel engines waste more than half the energy extracted from their fuel; mostly as heat and mechanical losses. Even under optimum conditions, such as a fixed-speed/ fixed-load static engine, designers have to balance the conflicting requirements of maximum power and minimum fuel consumption.
Truck engines, of course, work under far-from ideal conditions. Engine speeds and loads are constantly changing; emission limits must be complied with; even ambient air temperature has its effect.
Traditionally the best designers were those who reached the best compromise, but recently the emphasis has been on adjusting functions such as injection timing to suit the conditions of the moment.
For example, Cummins' step timing control (STC) device on its latest 14-litre Super E465 model makes use of a hydraulic tappet arrangement to shorten or lengthen the injector push rod by up to 5rnm, respectively retarding and advancing the nozzle opening. In the STC system, fuel-system pressure is used as the indicator of engine load.
Electronics also have an important role to play in moderating the need for compromise on fuelling.
VIRTUAL MONOPOLY
For traditional jerk-pump systems Bosch enjoys a virtual monopoly on the supply of Ft pumps, so it is not surprisingly the German company which is leading the way: Bosch's two automotive disciplines, namely fuel systems and electries, are brought together in trucks for the first time with electronic diesel control (EDC).
Scania is the first EDC user, on its 14-litre vee-eight, turbo-intercooled DSC14 engine. Already being sold in Sweden, R143 chassis with EDC will become available in Britain later this year.
Mercedes-Benz is offering electronic control on the FT pumps of Powerliner chassis sold in Germany. The hardware is essentially the same as Scania's, but Mercedes uses the initials EDR to describe it.
In the US, Caterpillar's current 14.6; litre jerk-pump-injected 3406B diesel is
available with what Cat calls programmable electronic engine control (PEEC), which operates on the same principles as EDC (or EDR).
The Bosch and Cat systems both involve replacing the familiar mechanical governor on the end of the Fl pump with an electronic engine speed regulator, on to which are added a host of additional
features which enable the fuel system to respond continuously to changing operational conditions.
American truck engines with unit injectors, including all Detriot Diesel units, all Cummins diesels, and the new-generation 3116 and 3176 engines from Cat, have required a subtly different approach. Electronic "instructions" are sent, not to the governor end of the Fl pump — there is no Fl pump — but to the push-rods of the individual injectors.
Where injectors are actuated mechanically from the engine camshaft, fuel metering and timing are determind "downstream", inside each injector assembly. Manufacturers are using electronic "intelligence" to enhance efficiency and optimise fuel economy and performance, while meeting ever-stricter emissions legislation.
Bosch sensors for example, monitor: C Engine speed • Road speed
o Accelerator pedal position, with a kickdown switch
O Intake air temperature O Fuel temperature 0 Turbocharger boost pressure.
Other control inputs include the startkey on/off functions and ambient conditions, notably air temperature and alti tude. To complete the instructionresponse feedback "loop", the control lever position on the Fl pump (conventionally determined directly by the driver's right foot, but now regulated by the electronic system's black box) is also sensed.
Programmed into the black box, or data module as Bosch calls it, are predetermined boundary conditions which constrain the system's operation under the external demands made upon it by the driver and the engine loading. They include overspeed protection, into which road speed governing can be incorporated. Peak cylinder pressure and exhaust temperature are also sensed as an engine protection function.
Data modules giving different performance economy characteristics and varying boundary conditions can be selected by the truck/engine manufacturer to suit the application. The module, housed typically in the cab away from fuel, oil and spray, literally plugs in. It can be changed in seconds, though Bosch is not suggesting that fleet operators be given the opportunity to play tunes with their engine programs.
On the end of the Fl pump the Bosch electronic governor assembly comprises a hydraulic piston with fuel as its working medium, acting on the pump rack, whose movement is determined by the black box. Its computed instructions regulate a solenoid valve, through which the rack piston is fed from two electric lowpressure (3bar) fuel lifts pumps, operated alternately.
EXCESSIVE FUELLING
The governor piston overrides the direct accelerator pedal linkage when instructed to by the microprocessor, principally in order to save fuel where otherwise excessive fuelling would adversely affect economy or encroach on those predetermined limits.
Caterpillar's similar PEEC system is claimed to improve combustion efficiency by up to 4%, translating into on-the-road fuel savings of up to 14% where drivers are ill-trained or disciplined.
Because Cat is a proprietary engine supplier, it endeavours, like rival Cummins, to retain all ancillaries on the engine rather than entrusting their correct installation elsewhere on the chassis (or in the cab) to the OEM. The PEEC mircoprocessor-based control module is thus soft-mounted to the engine block, immediately behind the FT pump's electronic governor, so it has to be cooled; to do this fuel is circulated through a manifold between the circuit boards.
One board is programmable with what Cat calls customer-specified parameters, such as maximum speed and cruise control speeds. Secret passwords fed into a Caterpillar service tool data link can be used for reprogramming. The other board contains the performance and emission calibrations for a specific rating. Back movement in the PEEC governor is accomplished differently from the Bosch system. Fuel pressure provides the muscle, but a brushless torque motor (spring loaded towards shut-off) does the actuation. A rack-position sensor gives feedback input, alongside a host of other inputs from a separate tamper-proof transducer module mounted below the governor. Into it come signals from sensors monitoring turbo boost, engine oil pressure and inlet air pressure.
For some years Cat 3406 engines have featured an auto-advance Spring-andflyweight injection-timing device, mounted in line with the pump but ahead of it, on the front of the timing case. On engines with PEEC, speed-related mechanical timing is replaced with an electronically controlled device.
As with rack movement, timing variation is hydraulically powered under brushless torque motor actuation. But a more sensitive and responsive double-acting hydraulic servo takes the place of a spring-loaded single-acting unit, so timing can be varied over 25° rather than 9° of crank angle, and hysteresis (lost motion, when servo direction is reversed) is avoided.
Consequently a unit injection system has been used for many years in the US by Cummins and Detroit Diesel, and is most familiar to British truck operators on Cummins 10and 14-litre diesels. It calls for subtly different techniques in the application of electronic control.
FIRST BUILDER
In 1985 Detroit Diesel, then a General Motors subsidiary, was the first diesel builder to use electronics to control the function of unit (mechanically-operated) injectors. The DD 60-series 11.1 and 12.7litre in-line six-cylinder diesels — the company's first big four-stroke diesels incorporated DDEC (Detroit Diesel electronic control) as standard.
Cummins, US market leader, has refused to be rushed in the development of its equivalent ECI (electronically control led injection) system. Research has been underway for over a decade, but the first ECI-equipped truck engine will not be launched in the US until autumn.
Caterpillar is now jumping on the unit injector bandwagon with its latest 3176, 10.2-litre diesel, introduced in the US late last year which also has electronic control as standard, with no delete option. The smaller 6.6-litre Cat diesel, launched a year ago, is also unit injected, with electronics to be offered at a later date. The Cat unit injector, with its integral solenoid-controlled poppet valve, was designed and is being manufactured by Lucas CAV.
All three electronic unit injector systems: DDEC, ECI and Cat's (yet to be given a snappy acronym), employ a solenoid valve in an extra housing alongside each unit injector which control the flow of fuel to the injector nozzle.
HIGH PRESSURES
The mechanical actuation of the injector from the engine camshaft is via a rockerarm and pushrod, which generates extremely high injection pressures of 1,400 bar or more. It remains a "fixed" (not time-variable) event. The timing of the electronically programmed solenoid valve's opening and closing, in relation to the established mechanical events inside the injector, enable the timing of spray start and finish to be controlled.
Each of the three American rivals is guarding its technical advances jealously. The microprocessor details are in any case not readily accessible. The way in which metering and timing are feeding the fuel through a computer-controlled solenoid valve is not spelled out by Detriot, Cummins or Cat in any real detail.
Cummins vice-president of engineering Carl Alders goes so far as to concede that there are "some similarities" between ECI and DDEC injectors. He says the hardest challange was to start and stop injection with a solenoid valve. Cummins had, he said, chosen not to close the valve against falling pressure or open it against full (currently 1,000bar) injection pressure.
Instead, the solenoid valve admits the measured amount of fuel and is then closed, before the descending push-rod generates the high injection pressure.
The valve does not re-open until injection is completed and the pressure has relaxed.
Detroit Diesel and Cummins have both had to make changes in the main part of the unit injector to accommodate the electronic control of metering and timing.
For a start they have eliminated the .helical grooves in rotating plungers which control fuelling through a moving rack, under direct control from the driver's foot on today's LlOs and Super Es.
Their function is taken over by the solenoid valve. A plain non-rotating injector plunger suffices.
At the same time a hydraulic "buffer" of fuel is interposed in the change to a "closed" fuel injector, whose nozzle is much more like a Bosch or CAV design. Thus the fuel spray is initiated by pressure alone and not by mechnical lifting through the pushrod.
WELL ADVANCED
The application of electronics on the latest truck diesels is clearly well advanced. However, it remains to be seen how quickly the average operator accepts them, particulary in terms of servicing.
When it comes to new technology hauliers are notoriously conservative, unless it has an immediate effect on the girth of their wallets.
0 by Alan Bunting