WEIGHTING FOR GRIP
Page 121
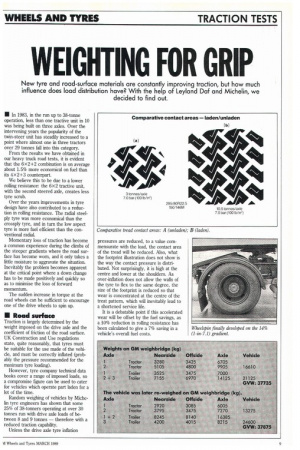
Page 122
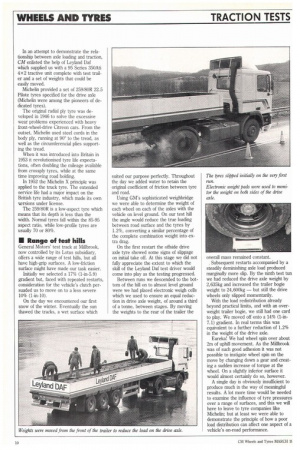
If you've noticed an error in this article please click here to report it so we can fix it.
New tyre and road-surface materials are constantly improving traction, but how much influence does load distribution have? With the help of Leyland Daf and Michelin, we decided to find out.
• In 1983, in the run up to 38-tonne operation, less than one tractive unit in 10 was being built on three axles. Over the intervening years the popularity of the twin-steer unit has steadily increased to a point where almost one in three tractors over 29 tonnes fall into this category.
From the results we have obtained in our heavy truck road tests, it is evident that the 6x2+2 combination is on average about 1.5% more economical on fuel than its 4 x 2 +3 counterpart.
We believe this to be due to a lower rolling resistance: the 6x2 tractive unit, with the second steered axle, creates less tyre scrub.
Over the years improvements in tyre design have also contributed to a reduction in rolling resistance. The radial steelply tyre was more economical than the crossply tyre, and in turn the low aspect tyre is more fuel efficient than the conventional radial.
Momentary loss of traction has become a common experience during the climbs of the steeper gradients where the road surface has become worn, and it only takes a little moisture to aggravate the situation. Inevitably the problem becomes apparent at the critical point where a down change has to be made positively and quickly so as to minimise the loss of forward momentum.
The sudden increase in torque at the road wheels can be sufficient to encourage one of the drive wheels to spin up.
• Road surface
Traction is largely determined by the weight imposed on the drive axle and the coefficient of friction of the road surface. UK Construction and Use regulations state, quite reasonably, that tyres must be suitable for the use made of the vehicle, and must be correctly inflated (probably the pressure recommended for the maximum tyre loading).
However, tyre company technical data books cover a range of imposed loads, so a compromise figure can be used to cater for vehicles which operate part laden for a lot of the time.
Random weighing of vehicles by Michelin tyre engineers has shown that some 25% of 38-tonners operating at over 30 tonnes run with drive axle loads of between 8 and 9 tonnes — therefore with a reduced traction capability.
Unless the drive axle tyre inflation pressures are reduced, to a value commensurate with the load, the contact area of the tread will be reduced. Also, what the footprint illustration does not show is the way the contact pressure is distributed. Not surprisingly, it is high at the centre and lower at the shoulders. As over-inflation does not allow the walls of the tyre to flex to the same degree, the size of the footprint is reduced so that wear is concentrated at the centre of the treat pattern, which will inevitably lead to a shortened service life.
It is a debatable point if this accelerated wear will be offset by the fuel savings, as a 10% reduction in rolling resistance has been calculated to give a 7% saving in a vehicle's overall fuel costs. In an attempt to demonstrate the relationship between axle loading and traction, CM enlisted the help of Leyland Daf which supplied us with a 95 Series 350Ati 4 X 2 tractive unit complete with test trailer and a set of weights that could be easily moved.
Michelin provided a set of 259/80R 22.5 Pilote tyres specified for the drive axle (Michelin were among the pioneers of dedicated tyres).
The original radial ply tyre was developed in 1946 to solve the excessive wear problems experienced with heavy front-wheel-drive Citreon cars. From the outset, Michelin used steel cords in the body ply, running at 900 to the tread, as well as the circumferencial plies supporting the tread.
When it was introduced into Britain in 1953 it revolutionised tyre life expectations, often doubling the mileage available from crossply tyres, while at the same time improving road holding.
In 1952 the Michelin X principle was applied to the truck tyre. The extended service life had a major impact on the British tyre industry, which made its own versions under license.
The 259/80R is a low-aspect tyre which means that its depth is less than the width. Normal tyres fall within the 85-95 aspect ratio, while low-profile tyres are usually 70 or 80%.
• Range of test hills
General Motors' test track at Millbrook, now controlled by its Lotus subsidiary, offers a wide range of test hills, but all have high-grip surfaces. A low-friction surface might have made our task easier.
Initially we selected a 17% (1-in-5.9) gradient but, faced with repeated restarts, consideration for the vehicle's clutch persuaded us to move on to a less severe 10% (1-in-10).
On the day we encountered our first snow of the winter. Eventually the sun thawed the tracks, a wet surface which suited our purpose perfectly. Throughout the day we added water to retain the original coefficient of friction between tyre and road.
Using GM's sophisticated weighbridge we were able to determine the weight of each wheel on each of the axles with the vehicle on level ground. On our test hill the angle would reduce the true loading between road surface and the tyres by 1.2%, converting a similar percentage of the complete combination weight into extra drag.
On the first restart the offside drive axle tyre showed some signs of slippage on initial take off. At this stage we did not fully appreciate the extent to which the skill of the Leyland Daf test driver would come into play as the testing progressed.
Between runs we descended to the bottom of the hill on to almost level ground were we had placed electronic weigh cells which we used to ensure an equal reduction in drive axle weight, of around a third of a tonne, between stages. By moving the weights to the rear of the trailer the overall mass remained constant.
, Subsequent restarts accompanied by a steadily deminishing axle load produced marginally more slip. By the ninth test tun we had reduced the drive axle weight by 2,635kg and increased the trailer bogie weight to 24,600kg — but still the drive wheels only slipped momentarily.
With the load redistribution already beyond practical limits, and with an overweight trailer bogie, we still had one card to play. We moved off onto a 14% (1-in7.1) gradient. In real terms this was equivalent to a further reduction of 1.2% in the weight of the drive axle.
Eureka! We had wheel spin over about 2m of uphill movement. As the Milibrook was of such good adhesion it was not possible to instigate wheel spin on the move by changing down a gear and creating a sudden increase of torque at the wheel. On a slightly inferior surface it would almost certainly do so, however.
A single day is obviously insufficient to produce much in the way of meaningful results. A lot more time would be needed to examine the influence of tyre pressures over a range of surfaces, and this we will have to leave to tyre companies like Michelin; but at least we were able to demonstrate the principle of how a poor load distribution can affect one aspect of a vehicle's on-road performance.