LEVATING FFICIENCY
Page 43
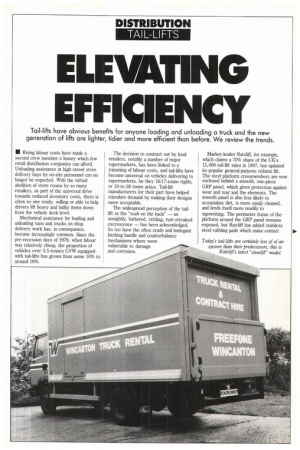
Page 44
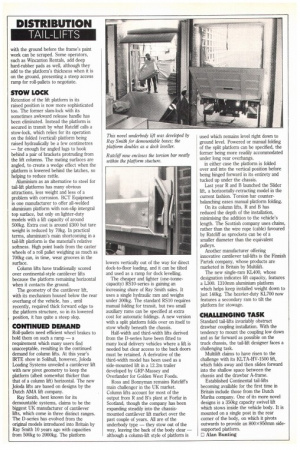
If you've noticed an error in this article please click here to report it so we can fix it.
Tail-lifts have obvious benefits for anyone loading and unloading a truck and the new generation of lifts are lighter, tidier and more efficient than before. We review the trends.
• Rising labour costs have made a second crew member a luxury which few retail distribution companies can afford. Unloading assistance at high street store delivery bays by on-site personnel can no longer be expected. With the virtual abolition of store rooms by so many retailers, as part of the universal drive towards reduced inventory costs, there is often no one ready, willing or able to help drivers lift heavy and bulky items down from the vehicle deck level.
Mechanical assistance for loading and unloading vans and trucks on shop delivery work has, in consequence, become increasingly common. Since the pre-recession days of 1979, when labour was relatively cheap, the proportion of vehicles over 3.5-tonnes GVW equipped with tail-lifts has grown from some 10% to around 18%. The decision to contract out by food retailers, notably a number of major supermarkets, has been linked to a trimming of labour costs, and tail-lifts have become universal on vehicles delivering to supermarkets, be they 16/17-tonne rikids, or 24-to-38 tonne artics. Tail-lift manufacturers for their part have helped stimulate demand by making their designs more acceptable.
The widespread perception of the taillift as the "scab on the back" — an unsightly, battered, rattling, rust-streaked excrescence — has been acknowledged. So too have the often crude and inelegant latching handle and counterbalance mechanisms where were vulnerable to damage and corrosion. Market-leader Ratcliff, for example, which claims a 70% share of the UK's 11,000 tail-lift sales in 1987, has updated its popular general-purpose column lift. The steel platform crossmembers are now enclosed behind a smooth, one-piece GRP panel, which gives protection against wear and tear and the elements. The smooth panel is also less likely to accumulate dirt, is more easily cleaned, and lends itself more readily to signwriting. The perimeter frame of the platform around the GRP panel remains exposed, but Ratcliff has added stainless steel rubbing pads which make contact with the ground before the frame's paint work can be scraped. Some operators, such as Wincanton Rentals, add deep hard-rubber pads as well, although they add to the platform's thickness when it is on the ground, presenting a steep access ramp for roll-pallets to negotiate.
STOW LOCK
Retention of the lift platform in its raised position is now more sophisticated too. The former slam-lock with its sometimes awkward release handle has been eliminated. Instead the platform is secured in transit by what Ratcliff calls a stow-lock, which relies for its operation on the folded (vertical) platform being raised hydraulically be a few centimetres — far enough for angled lugs to hook behind a pair of brackets protruding from the lift columns. The mating surfaces are angled, to create a wedge effect when the platform is lowered behind the latches, so helping to reduce rattle.
Aluminium as an alternative to steel for tail-lift platforms has many obvious attractions, less weight and less of a problem with corrosion. BCT Equipment is one manufacturer to offer all-welded aluminium platform with non-slip intergral top surface, but only on lighter-duty models with a lift capacity of around 500kg. Extra cost is around £300 but tare weight is reduced by 70kg. In practical terms, aluminium's main shortcoming in a tail-lift platform is the material's relative softness. High point loads from the caster wheels of a roll pallet weighing as much as 700kg can, in time, wear grooves in the surface.
Column lifts have traditionally scored over continental-style cantilever lifts because the platform remaining horizontal when it contacts the ground.
The geometry of the cantilever lift, with its mechanism housed below the rear overhang of the vehicle, has, until recently, required thick forward edge to the platform structure, so in its lowered position, it has quite a steep slop.
CONTINUED DEMAND
Roll-pallets need efficient wheel brakes to hold them on such a ramp — a requirement which many users find unacceptable, resulting in the continued demand for column lifts. At this year's IRTE show in Solihull, however, Joloda Loading Systems unveiled a cantilever lift with new pivot geometry to keep the platform (albeit somewhat thicker than that of a column lift) horizontal. The new Joloda lifts are based on designs by the Dutch AMA lift company.
Ray Smith, best known for its demountable systems, claims to be the biggest UK manufacturer of cantilever lifts, which come in three distinct ranges. The D-series has evolved from the original models introduced into Britain by Ray Smith 10 years ago with capacities from 500kg to 2000kg. The platform lowers vertically out of the way for direct dock-to-floor loading, and it can be tilted and used as a ramp for dock levelling.
The cheaper and lighter (one-tonnecapacity) RS10-series is gaining an increasing share of Ray Smith sales. It uses a single hydraulic ram and weighs under 300kg. The standard RS10 requires manual folding for transit, but two small auxiliary rams can be specified at extra cost for automatic foldings. A new version with a split platform folds over on itself to stow wholly beneath the chassis.
Half-width and third-width lifts derived from the D-series have been fitted to many local delivery vehicles where a lift is needed but clear access to the back doors must be retained. A derivative of the third-width model has been used as a side-mounted lift in a 12.2m trailer developed by GRP-Massey and Overlander for Golden West Foods.
Ross and Bonnyman remains Ratcliffs main challenger in the UK market. Column lifts account for most of the output from R and B's plant at Forfar in Scotland, though the company has been expanding steadily into the chassismounted cantilever lift market over the past couple of years. All are of the underbody type — they stow out of the way, leaving the back of the body clear — although a column-lift style of platform is
used which remains level right down to ground level. Powered or manual folding of the split platform can be specified, the former being more readily accommodated under long rear overhangs.
in either case the platform is folded over and into the vertical position before being hinged forward in its entirety and tucked up under the chassis.
Last year R and B launched the Slider lift, a horizontally-retracting model in the current fashion. Torsion bar counterbalanching eases manual platform folding.
On its column lifts, R and B has reduced the depth of the installation, minimising the addition to the vehicle's length. The Scottish company uses chains, rather than the wire rope (cable) favoured by Ratcliff as sprockets can be of a smaller diameter than the equivalent pulleys.
Another manufacturer offering innovative cantilever tail-lifts is the Finnish Partek company, whose products are marketed in Britain by Multilift.
The new single-ram KL400, whose designation indicates lift capacity, features a 1300. 1310mm aluminium platform which helps keep installed weight down to just 140kg. The heavier-duty KL700 now features a secondary ram to tilt the platform for stowage.
CHALLENGING TASK
Standard tail-lifts invariably obstruct drawbar coupling installation. With the tendency to mount the coupling low down and as far forward as possible on the truck chassis, the tail-lift designer faces a challenging task.
Multilift claims to have risen to the challenge with its KLTA-HV-1500 lift, which folds away and then slides forward into the shallow space between the chassis and the drawbar A-frame.
Established Continental tail-lifts becoming available for the first time in Britain include those from the Dutch Mariba company. One of its more novel designs is a 350kg capacity swivel lift which stows inside the vehicle body. It is mounted on a single post in the rear corner of the body, on which it pivots outwards to provide an 800 x 950mm sidesupported platform.
0 Alan Bunting