FORD'S NEW 2.5 litre, direct injection, diesel engine (described in
Page 51
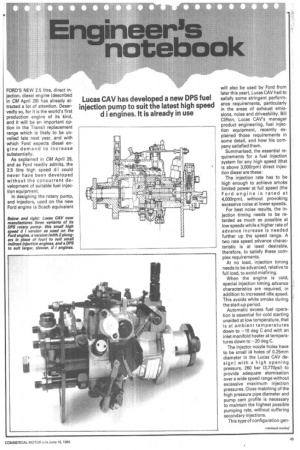
Page 52
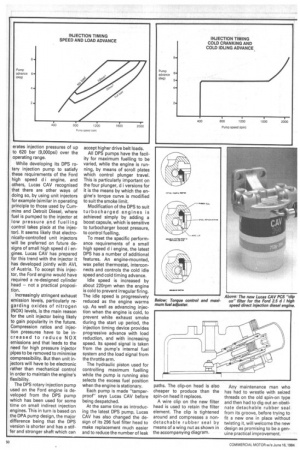
If you've noticed an error in this article please click here to report it so we can fix it.
CM April 28) has already attracted a lot of attention. Deservedly so, for it is the world's first production engine of its kind, and it will be an important option in the Transit replacement range which is likely to be unveiled late next year, and with which Ford expects diesel engine demand to increase substantially.
As explained in CM April 28, and as Ford readily admits, the 2.5 litre high speed d i could never have been developed without the concurrent development of suitable fuel injection equipment.
In designing the rotary pump, and injectors, used on the new Ford engine (a Bosch equivalent will also be used by Ford from later this year), Lucas CAV had to satisfy some stringent performance requirements, particularly in the areas of exhaust emissions, noise and driveability. Bill Clifton, Lucas CAV's manager product engineering, fuel injection equipment, recently explained those requirements in some detail, and how his company satisfied them.
Summarised, the essential requirements for a fuel injection system for any high speed (that is above 3,000rpm) direct injection diesel are these: The injection rate has to be high enough to achieve smoke limited power at full speed (the Ford engine is rated at 4,000rpm), without provoking excessive noise at lower speeds.
For best noise results, the injection timing needs to be retarded as much as possible at low speeds while a higher rate of advance increase is needed further up the speed range. A two rate speed advance characteristic is at least desirable, therefore, to satisfy these complex requirements.
At no load, injection timing needs to be advanced, relative to full load, to avoid misfiring.
When the engine is cold, special injection timing advance characteristics are required, in addition to increased idle speed. This avoids white smoke during the start-up period.
Automatic excess fuel operation is essential for cold starting unaided at low temperature, that is at ambient temperatures down to —10 deg C and with an inlet manifold heater at temperatures down to —20 deg C.
The injector nozzle holes have to be small (4 holes of 0.25mm diameter in the Lucas CAV design) with a high opening pressure, 260 bar (3,770psi) to provide adequate atomisation over a wide speed range without excessive maximum injection pressures. Close matching of the high pressure pipe diameter and pump cam profile is necessary to maintain the highest possible pumping rate, without suffering secondary injections.
This type of configuration gen erates injection pressures of up to 620 bar (9,000psi) over the operating range.
While developing its DPS rotary injection pump to satisfy these requirements of the Ford high speed d i engine, and others, Lucas CAV recognised that there are other ways of doing so, by using unit injectors for example (similar in operating principle to those used by Cummins and Detroit Diesel, where fuel is pumped to the injector at low pressure and fuelling control takes place at the injector). It seems likely that electronically-controlled unit injectors will be preferred on future designs of small high speed d i engines. Lucas CAV has prepared for this trend with the injector it has developed jointly with AVL of Austria. To accept this injector, the Ford engine would have required a re-designed cylinder head — not a practical proposition.
Increasingly stringent exhaust emission levels, particularly regarding oxides of nitrogen (NOX) levels, is the main reason for the unit injector being likely to gain popularity in the future. Compression ratios and injection pressures have to be increased to reduce NOX emissions and that leads to the need for high pressure injector pipes to be removed to minimise compressibility. But then unit injectors will have to be electronic rather than mechanical control in order to maintain the engine's flexibility.
The DPS rotary injection pump used on the Ford engine is developed from the DPS pump which has been used for some time on small indirect injection engines. This in turn is based on the DPA pump design, the major difference being that the DPS version is shorter and has a stiffer and stronger shaft which can accept higher drive belt loads.
All DPS pumps have the facility for maximum fuelling to be varied, while the engine is running, by means of scroll plates which control plunger travel. This is particularly important on the four plunger, d i versions for it is the means by which the engine's torque curve is modified to suit the smoke limit.
Modification of the DPS to suit turbocharged engines is achieved simply by adding a boost capsule, which is sensitive to turbocharger boost pressure, to control fuelling.
To meet the specific performance requirements of a small high speed d i engine, the latest DPS has a number of additional features. An engine-mounted, wax pellet thermostat, interconnects and controls the cold idle speed and cold timing advance.
Idle speed is increased by about 220rpm when the engine is cold to prevent irregular firing. The idle speed is progressively reduced as the engine warms up. As well as advancing injection when the engine is cold, to prevent white exhaust smoke during the start up period, the injection timing device provides progressive advance with load reduction, and with increasing speed. Its speed signal is taken from the pump's internal fuel system and the load signal from the throttle arm.
The hydraulic piston used for controlling maximum fuelling while the pump is running also selects the excess fuel position when the engine is stationary.
Each pump is made "tamperproof" says Lucas CAV before being despatched.
At the same time as introducing the latest DPS pump, Lucas CAV has also changed the design of its 296 fuel filter head to make replacement much easier and to reduce the number of leak paths. The clip-on head is also cheaper to produce than the spin-on head it replaces.
A wire clip on the new filter head is used to retain the filter element. The clip is tightened around and compresses a nondetachable rubber seal by means of a wing nut as shown in the accompanying diagram. Any maintenance man who has had to wrestle with seized threads on the old spin-on type and then had to dig out an obstinate detachable rubber seal from its groove, before trying to fit a new one in place without twisting it, will welcome the new design as promising to be a genuine practical improvement.