Mercedes-Benz USA
Page 40
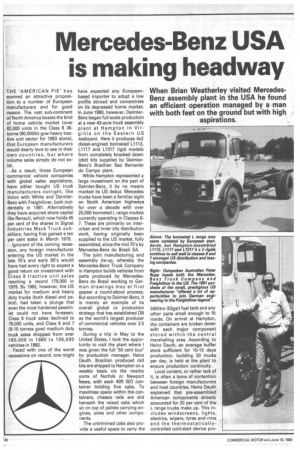
Page 41
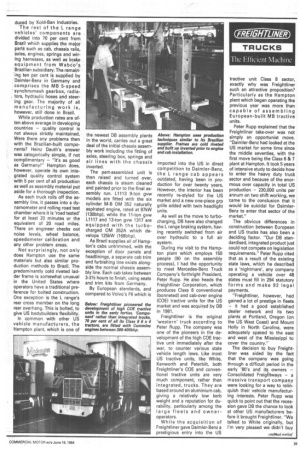
Page 42
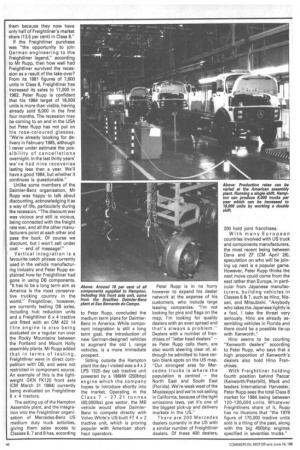
If you've noticed an error in this article please click here to report it so we can fix it.
is making headway.
THE 'AMERICAN PIE' has seemed an attractive proposition to a number of European manufacturers and for good reason. The vast sub-continent of North America boasts the kind of home vehicle market (over 82,000 units in the Class 8 36tonne (80,0001b) gcw heavy tractive unit sector for 1983 alone), that European manufacturers would dearly love to see in their own countries, but where volume sales simply do not exist.
As a result, those European commercial vehicle companies with global sales aspirations, have either bought US truck manufacturers outright, like Volvo with White and DaimlerBenz with Freightliner, both incidentally in 1981. Alternatively they have acquired share capital like Renault, which now holds 45 per cent of the shares in Signal Industries Mack Truck subsidiary, having first gained a ten per cent stake in March 1979.
Ignorant of the coming recession, any foreign manufacturer entering the US market in the late 70's and early 80's would have had every right to expect a good return on investment with Class 8 tractive unit sales reaching a record 179,000 in 1979. By 1982, however, the US market for medium and heavy duty trucks (both diesel and petrol), had taken a plunge that even the most hardened pessimist could not have foreseen. Class 8 truck sales declined to 76,000 units, and Class 6 and 7 (9-15 tonnes gvw) medium duty truck sales dropped from over 180,000 in 1980 to 106,000 vehicles in 1982.
Faced with one of the worst recessions on record, one might have expected any Europeanbased importer to adopt a low profile abroad and concentrate on its depressed home market. In June 1980, however, DaimlerBenz began full-scale production at a new 43-acre truck assembly plant at Hampton in Virginia on the Eastern US seaboard. Here it produces 4x2 diesel-engined bonneted L1113, L1117 and L1317 rigid models from completely knocked down (ckd) kits supplied by DaimlerBenz's Brazilian Sao Bernardo do Campo plant.
While Hampton represented a large investment on the part of Daimler-Benz, it by no means marked its US debut. Mercedes trucks have been a familiar sight on North American highways for over a decade with over 25,000 bonneted L range models currently operating in Classes 67. These are primarily on interurban and inner city distribution work, having originally been supplied to the US market, fully assembled, since the mid 70's by Mercedes-Benz do Brasil SA.
The joint manufacturing and assembly tie-up, whereby the Mercedes-Benz Truck Company in Hampton builds vehicles from parts produced by MercedesBenz do Brasil working to German drawings may at first appear a round-about process. But according to Daimler-Benz, it is merely an example of its overall global cv production strategy that has established DB as the world's largest producer of commercial vehicles over 3,5 tonnes.
During a trip in May to the United States, I took the opportunity to visit the plant where I was given the full '50 cent tour' by production manager, Heinz Dauth. Brazilian produced ckd kits are shipped to Hampton on a weekly basis via the nearby ports of Norfolk or Newport News, with each 40ft ISO container holding five cabs. To maximise space within the containers, chassis rails are slid beneath the raised cabs which sit on top of pallets carrying engines, axles and other components.
The untrimmed cabs also provide a useful space to carry the 2401itre (53ga1) fuel tank and any other parts small enough to fit inside. On arrival at Hampton, the containers are broken down with each major component stored within the central marshalling area. According to Heinz Dauth, an average buffer stock sufficient for 10-15 days production, building 20 trucks per day, is held at the plant to ensure production continuity.
Local content, or rather lack of it, is often a bone of contention between foreign manufacturers and host countries. Heinz Dauth explained that pre-assembled American components already accounted for 20 per cent of the L range trucks make up. This in cludes windscreens, lights, electrics, wipers, tyres and rims and the thermostaticallycontrolled cold-start device pro duced by Kold-Ban Industries.
The rest of the L range vehicles' components are divided into 70 per cent from Brazil which supplies the major parts such as cab, chassis rails, -axles, engines, springs and wiring harnesses, as well as brake equipment from Wabco's Brazilian subsidiary. The remaining ten per cent is supplied by Daimler-Benz in Germany and :comprises the MB 5-speed synchromesh gearbox, radiators, hydraulic hoses and steering gear. The majority of all manufacturing work is, however, still done in Brazil.
While production rates are often above average in developing countries — quality control is not always strictly maintained. Were there any problems then with the Brazilian-built components? Heinz Dauth's answer was categorically simple, if not complimentary — "it's as good as Germany!" Hampton does, however, operate its own integrated quality control system with 5 per cent of all production as well as assembly material put aside for a thorough inspection.
As each truck rolls off the assembly line, it passes into a dynamometer and rolling road test chamber where it is 'road tested' for at least 20 minutes or the equivalent of 20 road miles. There an engineer checks out noise levels, wheel balance, speedometer calibration and any other problem areas.
Not surprisingly, not only does Hampton use the same materials but also similar production methods to Brazil. The predominantly cold riveted ladder frame is somewhat unusual in the United States where operators have a traditional preference for bolted construction. One exception is the L range's rear cross member on the long rear overhang. This is bolted, to give US bodybuilders flexibility.
In common with other US vehicle manufacturers, the Hampton plant, which is one of the newest DB assembly plants in the world, carries out a great deal of the initial chassis assembly work including the fitting of axles, steering box, springs and air lines with the chassis inverted.
The part-assembled unit is then raised and turned over, each chassis is steam cleaned and painted prior to the final assembly run. L1113 9-ton gvw models are fitted with the six cylinder M-B OM 352 naturally aspirated engine, rated at 97kW (130bhp), while the 11-ton gvw L1117 and 13-ton gvw 1317 are equipped with the turbocharged OM 352A which develops 125kW (168bhp).
As Brazil supplies all of Hampton's cabs untrimmed, with the exception of door panels and headlinings, a separate cab trim and furbishing line exists alongside the normal chassis assembly line. Each cab takes between 3-31/2 hours to finish, using seats and trim kits from Germany.
By European standards, and compared to Volvo's F6 which is imported into the US in direct competition to Daimler-Benz, the L range cab appears outdated, having been in production for over twenty years. However, the interior has been recently re-styled for the US market and a new one-piece grp grille added with twin headlight units.
As well as the move to turbocharging, DB have also changed the L range braking system, having recently switched from air over hydraulic to a full air system.
During my visit to the Hampton plant which employs 150 people (90 on the assembly process), I had the opportunity to meet Mercedes-Benz Truck Company's forthright President, Peter Rupp. He also heads the Freightliner Corporation, which .produces Class 8 conventional (bonneted) and cab-over engine (COE) tractive units for the US market and was acquired by DB in 1981.
Freightliner is the original 'western' truck according to Peter Rupp. The company was one of the pioneers in the development of the high COE tractive unit immediately after the war, to counter various state vehicle length laws. Like most US tractive units, like White, Kenworth and Peterbilt, both Freightliner's COE and conventional tractive units are very much component, rather than integrated, trucks. They are based around an aluminium cab, giving a relatively low kerb weight and a reputation for durability, particularly among the large fleets and owneroperators.
While the acquisition of Freightliner gave Daimler-Benz a prestigious entry into the US tractive unit Class 8 sector, exactly why was Freightliner such an attractive proposition? Particularly as the Hampton plant which began operating the previous year was more than capable of assembling European-built MB tractive units.
Peter Rupp explained that the Freightliner take-over was not simply an opportunist move. "Daimler-Benz had looked at the US market for some time since the middle seventies, with the first move being the Class 6 & 7 plant at Hampton. It took 5 years of intensive study to decide how to enter the heavy duty truck sector and because of the enormous over capacity in total US production — 230,000 units per annum on two shift working, we 'came to the conclusion that it would be suicidal for DaimlerBenz to enter that sector of the market."
The obvious differences in construction between European and US trucks has also been a deciding factor. "Our DB standardised, integrated product just could not compete on legislation requirements." Peter Rupp cited that as a result of the existing state laws, which he described as a 'nightmare', any company operating a vehicle over 48 states must fill in 294 statutory forms and make 92 legal payments.
"Freightliner, however, had gained a lot of prestige in fleets — it had a good established dealer network and its two plants at Portland, Oregon (on the US West Coast) and Mount Holly in North Carolina, were adequately spaced to the east and west of the Mississippi to cover the country."
The decision to buy Freightliner was aided by the fact that the company was going through a difficult period in the early '80's and its owners — Consolidated Freiglitways — a massive transport company were looking for a way to relinquish their vehicle manufacturing interests. Peter Rupp was quick to point out that the recession gave DB the chance to look at other US manufacturers before it brought Freightliner. "We talked to White originally, but I'm very pleased we didn't buy them because they now have only half of Freightliner's market share (13.5 per cent) in Class 8."
If the Freightliner purchase was "the opportunity to join German engineering to the Freightliner legend," according to Mr Rupp, then how well had Freightliner survived the recession as a result of the take-over? From its 1981 figures of 7,600 units in Class 8, Freightliner has increased its sales to 11,000 in 1983. Peter Rupp is confident that his 1984 target of 18,000 units is more than viable, having already sold 6,000 in the first four months. The recession may be coming to an end in the USA but Peter Rupp has not put on his rose-coloured glasses. "We're already booking for delivery in February 1985, although I never under estimate the possibility of cancellations overnight. In the last thirty years' we've had nine recoveries lasting less than a year. We'll have a good 1984, but whether it continues is questionable."
Unlike some members of the Daimler-Benz organisation, Mr Rupp was happy to talk about discounting, acknowledging it as a way of life, particularly during the recession. "The discount war was vicious and still is vicious, being connected with the freight rate war, and all the other manufacturers point at each other and pass the buck. Of course we discount, but I won't sell under cost — end of message!"
Vertical integration is a favourite catch phrase currently used in the vehicle manufacturing industry and Peter Rupp explained how far Freightliner had gone in using DB components. "It has to be a long term aim as America is the most conservative trucking country in the world." Freightliner, however, are currently testing DB axles, including hub reduction units and a Freightliner 6 x 4 tractive unit fitted with an OM 422 14 litre engine is also being evaluated on a regular run over the Rocky Mountains between the Portland and Mount Holly assembly plants. Mr Rupp added that in terms of testing, Freightliner were in direct competition with DB, and were not restricted in component source. An example of this is the lightweight GKN FK120 front axle (CM March 31 19841 currently being evaluated on Freightliner 6 x 4 tractors.
The setting up of the Hampton Assembly plant, and the integration into the Freightliner organisation of Mercedes-Benz US medium duty truck activities, giving them sales access to Classes 6, 7 and 8 has, according to Peter Rupp, concluded the medium term plans for DaimlerBenz in America. While component integration is still a long term goal, the introduction of new German-designed vehicles to augment the old L range vehicles, is a more immediate prospect.
Sitting outside the Hampton plant the day I visited was a 4 x 2 LPS 1525 day cab tractive unit powered by a 186kW (250bhp) engine which the company hopes to introduce shortly into the market. Operating in the Class 7 — 27.21 tonnes (60,000Ibs) gcw sector, the MB vehicle would allow DaimlerBenz to compete directly with Volvo White's US-built F7 4 x 2 tractive unit, which is proving popular with American shorthaul operators. Peter Rupp is in no hurry however to expand his dealer network at the expense of his customers, who include large leasing companies. "I'm not looking for pins and flags on the map, I'm looking for quality dealers with an even spread and that's always a problem." Dealers with a number of franchises of "letter head dealers" — as Peter Rupp calls them, are also worth steering clear of, although he admitted to have certain blank spots on the US map. "Our strongest area for Mercedes trucks is where the population is centred — the North East and South East (Florida). We're weak west of the Mississippi and we're not selling in California, because of the tight emissions laws, yet it's one of the biggest pick-up and delivery markets in the US."
There are 200 Mercedes dealers currently in the US with a similar number of Freightliner dealers. Of these 400 dealers, 200 hold joint franchises.
With many European countries involved with US truck and components manufacturers, the most recent being between Dana and ZF (CM April 28), speculation on who will be joining up next is a popular game. However, Peter Rupp thinks the next move could come from the east rather than Europe, in particular from Japanese manufacturers, building vehicles in Classes 6 & 7, such as Hino, Nissan, and Mitsubishi. "Anybody who takes the Japanese lightly is a fool, I take the threat very seriously. Hino are already assembling vehicles in Florida and there could be a possible tie-up with Kenworth."
Hino seems to be courting "Kenworth dealers" according to Peter Rupp, who says that a high proportion of Kenworth's dealers also hold Hino Franchises.
With Freightliner holding fourth position behind Paccar (Kenworth/Peterbilt), Mack and leaders International Harvester, Peter Rupp sees the total Class 8 market for 1984 being between 120-130,000 units. Whatever Freightliners share of it, Rupp has no illusions that "the 1979 figure of 170,000 tractive units sold is a thing of the past, along with the big 450bhp engines specified in seventies trucks."