'We conduct stringent tests sometimes with alarming results'
Page 55
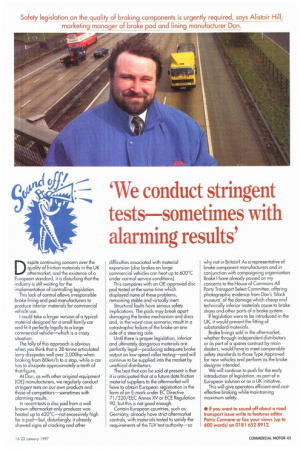
If you've noticed an error in this article please click here to report it so we can fix it.
Despite continuing concern over the quality of friction materials in the UK aftermarket, and the existence of a European standard, it is disturbing that the industry is still waiting for the implementation of controlling legislation.
This lack of control allows irresponsible brake lining and pad manufacturers to produce inferior materials for commercial vehicle use.
I could take a larger version of a typical material designed for a small family car and fit it perfectly legally to a large commercial vehicle—which is a crazy situation.
The folly of this approach is obvious when you think that a 38-tonne articulated lorry dissipates well over 3,000hp when braking from 80km/h to a stop, while a car has to dissipate approximately a tenth of that figure.
At Don, as with other original equipment 10E) manufacturers, we regularly conduct stringent tests on our own products and those of competitors—sometimes with alarming results.
In recent tests a disc pad from a well known aftermarket-only producer was heated up to 420°C—not excessively high for a pad—but, disturbingly, it already showed signs of cracking and other
difficulties associated with material expansion (disc brakes on large commercial vehicles can heat up to 600'C under normal service conditions).
This compares with an OE-approved disc pad tested at the some time which displayed none of these problems, remaining stable and virtually inert. Structural faults have serious safety implications. The pads may break apart damaging the brake mechanism and discs and, in the worst case scenario, result in a catastrophic Failure of the brake on one side of a steering axle. Until there is proper legislation, inferior and ultimately dangerous materials are perfectly legal—producing adequate brake output on low-speed roller testing—and wiLl continue to be supplied into the market by unethical distributors.
The best that can be said at present is that it is anticipated that at a future date friction material suppliers to the aftermarket will have to obtain European registration in the form of an E-mark under EC Directive 71/320/EEC Annex XV or ECE Regulation 90, but this is not good enough. Certain European countries, such as Germany, already have strict aftermarket controls, with materials tested to satisfy the requirements of the TO/ test authority—so
why not in Britain? As a representative of brake component manufacturers and in conjunction with campaigning organisation Brake I have already passed on my concerns to the House of Commons All Party Transport Select Committee, offering photographic evidence from Don's 'black museum' of the damage which cheap and technically inferior materials cause to brake shoes and other parts of a brake system.
If legislation were to be introduced in the UK, it would prevent the fitting of substandard materials.
Brake linings sold in the aftermarket, whether through independent distributors or as part of a spares contract by main dealers, would have to meet comparable safety standards to those Type Approved For new vehicles and perform as the brake designer intended. We will continue to push for the early introduction of legislation, as part of a European solution or as a UK initiative. This will give operators efficient and costeffective braking while maintaining maximum safety.
• If you want to sound off about a road transport issue write to features editor Patric Cunnane or fax your views (up to 600 words) on 0181 652 8912.